高分子材料的耐热性范例(12篇)
来源:收集
高分子材料的耐热性范文篇1
【关键词】冲压模具材料强化处理技术材料分类
中图分类号:TB文献标识码:A文章编号:1009-914X(2013)35-237-01
冲压模具材料作为工业制造业重要的材料,而模具也是作为工业制造中的基本工艺设备,在工业生产制作过程中,能够有效地提高机械生产效率,充分利用冲压模板材料,使得产品的精度和复杂度不断地提高。这些优势是其它的工业加工技术所无所超越的,模具的良好运用,使得冲压模具材料能够广泛的运用于汽车、飞机、电子、家电等精密仪器的制作过程中。模具生产运用中,其工作技能不断地发展,促进了工业生产的发展,也使得各种模具种类不断地增加,工艺越来越精密,形状越来越多样。但是目前受到热处理技术的限制,使得模具的发展速度减缓,并且出现了一些质量上的问题。因此,必须对模具材料的种类进行分析,同时选取额适合的模具材料应对各种处理技术,保证模具在各个产业中运用的质量。
一、常见冲压模具材料
(一)模具材料种类
目前,在工业生产中常见的冲压模具材料大部分都包括了碳元素钢材、低合金钢材、高碳高镉钢材以及钢结硬质合金等材料。在这些材料之中,成本价格比较低、加工延展性能较好以及在热处理后强度较高的材料是碳元素钢材。它在使用过程中耐磨性能最好,其材料通常在尺寸较小、形状普通并且压力荷载力较小的模具中使用广泛。同时碳元素材料作为低合金钢材的基础,其成品是通过在材料中添加适量的合金元素而形成的。低合金钢材的优点在于它能够快速地在降低淬火冷却速度,将热处理力和组织力降低到最低点。使得材料不会受到淬火的影响而产生变形,出现开裂的倾向。高碳高镉钢材在生产过程中不仅其硬度、强度以及耐磨度是所有材料里最高,而且还具有较好的物体稳定性、淬硬性以及渗透性,热处理中受到高温而发生变形的效果很小。而钢结硬质合金是在硬质合金的基础上,添加了少量的铁粉和合金元素粘合剂而形成的,其硬度和耐磨性比钢结硬质更好。同时,在改造过程中添加了大量的碳化钛和碳化钨等材料作为强度质相,并且在制作过程中运用粉末治金的方法预烧而形成,使得这种冲压模具材料更为坚固耐用,能够适合在大量的工业技术生产中使用。
(二)模具材料性能
模具在使用过程中,首先要充分了解模具材料的使用性能和技术工艺,并且要根据具体实践工业生产的情况进行材料的选择,按照不同的产品的性能选择不同的模具。通常情况下,模具材料的主要性能主要有高强度、高硬度、延展性能强、耐磨性好以及抗腐蚀性能强等特点。模具的强度是工业生产材料抵抗外界环境压力而产生变形和断裂的技术支持。而模具的硬度高低将直接影响着模具的使用寿命,同时也关系到模具质量;良好的延展性能则能直接反映出材料在高压强的条件下所能受到的冲击载荷力以及抵抗材料脆性断裂,同时也是模具钢在生产运用中,特别是冲压用冷作模具钢性能的重要技术支撑;抗腐蚀性是指材料在高温高压的环境中不被氧化或者腐蚀,同时其压力载荷条件下能够有效的抵抗破坏。模具工艺技术性能主要包括热处理技术性能等。热处理技术对模具质量有着极大的影响,尤其是在实际生产过程中,冲压模具材料必须要有良好的淬硬性和高强度的渗透性,以此确保模具材料的强度及耐磨性能。
二、冲压模具材料的分类对热处理的影响
冲压模具材料的类型挫样,不同的冲压模具有着材料性能的要求也不同。如在汽车制造工业中,应用新进一批结构较为复杂的冲压模具,强化热处理技术后,模板的孔隙出现变形,甚至呈带状或块状分布。主要原因是碳化物膨胀系数比钢小,热处理时冲压模具材料因为内部膨胀,而在冷却系统中又受到内部模具内孔收缩,使得模具提高热处理技术。冲压模具材料的应该根据具体的冲压模具材料,强化其处理技术。以此确保模具材料质量和处理技术的顺利进行,因此根据具体的冲压模具材料进行合理选择。
为了能够强化冲压模具材料的处理技术,在生产运用中一般采用物理表面和化学表面的处理方式强化技术。一般情况而言,化学表面处理技术在强化中主要包括了材料表面扩散渗入和涂覆两种方法。其中,在材料表面扩散渗入的处理方法中首先是将冲压模具材料设置在特定的温度下,同时保证材料能够在密闭的空间中保持活力和戒指的温度,然后将化学介质渗透进模具表面,使得模具材料的表面化学成分和组织发生改变,增强其材料的耐磨性、耐蚀性以及耐压性等。而使用化学表面处理中主要包括的技术有渗氮、渗碳、碳氮共渗等;而另一种涂覆技术则是指在冲压模具材料的表面涂上一种新型的材料,此次来使模具材料表面性的耐压性增强,这种模具涂覆技术所运用的技术主要有化学镀、离子注入、化学气相沉积等;而在物理表面处理技术中其技术原理主要是指运用物理的办法强化对模具材料的处理技术,使得模具材料表面能够提高荷载力,增强材料表面法的抗腐蚀能力,提高力学性能。物理表面处理中主要运用的技术有激光表面淬火、高频淬火等,达到提高冲压模具材料表面的硬度、强度、耐磨性、抗腐蚀性能等。
三、结束语
冲压模具材料在材料生产过程中都应该保证其性能,保证生产正常运行工作以及热处理技术应该都保持在固定值上。冲压模具材料凭借在工业生产中的优势,广泛的运用在各个行业中,同时在生产活动中,模具样式多样容易因为材料选择上发生错误或者是在热处理技术上没有强化,使得生产过程中出现一定的错误。并且在一定的程度上影响到了模具使用的寿命,通过对不同种类的模具进行分析,热处理技术中采取不同的方式进行强化,加强模具使用的科学性,满足现代化工业生产的要求。
参考文献:
[1]陈雪菊,张超,陈慧.模具材料及其热处理对冷冲模具寿命的影响[J].科技信息,2010(04).
[2]张越.论冲压模具的选择[J].电子机械工程,2009(02).
高分子材料的耐热性范文
复合材料是指由两种或两种以上不同物质以不同方式组合而成的材料,它可以发挥各种材料的优点,克服单一材料的缺陷,扩大材料的应用范围。由于复合材料具有重量轻、强度高、加工成型方便、弹性优良、耐化学腐蚀和耐候性好等特点,已逐步取代木材及金属合金,广泛应用于航空航天、汽车、电子电气、建筑、健身器材等领域,在近几年更是得到了飞速发展。
随着科技的发展,树脂与玻璃纤维在技术上不断进步,生产厂家的制造能力普遍提高,使得玻纤增强复合材料的价格成本已被许多行业接受,但玻纤增强复合材料的强度尚不足以和金属匹敌。因此,碳纤维、硼纤维等增强复合材料相继问世,使高分子复合材料家族更加完备,已经成为众多产业的必备材料。目前全世界复合材料的年产量已达550多万吨,年产值达1300亿美元以上,若将欧、美的军事航空航天的高价值产品计入,其产值将更为惊人。从全球范围看,世界复合材料的生产主要集中在欧美和东亚地区。近几年欧美复合材料产需均持续增长,而亚洲的日本则因经济不景气,发展较为缓慢,但中国尤其是中国内地的市场发展迅速。据世界主要复合材料生产商PPG公司统计,2000年欧洲的复合材料全球占有率约为32%,年产量约200万吨。与此同时,美国复合材料在20世纪90年代年均增长率约为美国GDP增长率的2倍,达到4%~6%。2000年,美国复合材料的年产量达170万吨左右。特别是汽车用复合材料的迅速增加使得美国汽车在全球市场上重新崛起。亚洲近几年复合材料的发展情况与政治经济的整体变化密切相关,各国的占有率变化很大。总体而言,亚洲的复合材料仍将继续增长,2000年的总产量约为145万吨,预计2005年总产量将达180万吨。
从应用上看,复合材料在美国和欧洲主要用于航空航天、汽车等行业。2000年美国汽车零件的复合材料用量达14.8万吨,欧洲汽车复合材料用量到2003年估计可达10.5万吨。而在日本,复合材料主要用于住宅建设,如卫浴设备等,此类产品在2000年的用量达7.5万吨,汽车等领域的用量仅为2.4万吨。不过从全球范围看,汽车工业是复合材料最大的用户,今后发展潜力仍十分巨大,目前还有许多新技术正在开发中。例如,为降低发动机噪声,增加轿车的舒适性,正着力开发两层冷轧板间粘附热塑性树脂的减振钢板;为满足发动机向高速、增压、高负荷方向发展的要求,发动机活塞、连杆、轴瓦已开始应用金属基复合材料。为满足汽车轻量化要求,必将会有越来越多的新型复合材料将被应用到汽车制造业中。与此同时,随着近年来人们对环保问题的日益重视,高分子复合材料取代木材方面的应用也得到了进一步推广。例如,用植物纤维与废塑料加工而成的复合材料,在北美已被大量用作托盘和包装箱,用以替代木制产品;而可降解复合材料也成为国内外开发研究的重点。
另外,纳米技术逐渐引起人们的关注,纳米复合材料的研究开发也成为新的热点。以纳米改性塑料,可使塑料的聚集态及结晶形态发生改变,从而使之具有新的性能,在克服传统材料刚性与韧性难以相容的矛盾的同时,大大提高了材料的综合性能。
树脂基复合材料的增强材料
树脂基复合材料采用的增强材料主要有玻璃纤维、碳纤维、芳纶纤维、超高分子量聚乙烯纤维等。
1、玻璃纤维
目前用于高性能复合材料的玻璃纤维主要有高强度玻璃纤维、石英玻璃纤维和高硅氧玻璃纤维等。由于高强度玻璃纤维性价比较高,因此增长率也比较快,年增长率达到10%以上。高强度玻璃纤维复合材料不仅应用在军用方面,近年来民用产品也有广泛应用,如防弹头盔、防弹服、直升飞机机翼、预警机雷达罩、各种高压压力容器、民用飞机直板、体育用品、各类耐高温制品以及近期报道的性能优异的轮胎帘子线等。石英玻璃纤维及高硅氧玻璃纤维属于耐高温的玻璃纤维,是比较理想的耐热防火材料,用其增强酚醛树脂可制成各种结构的耐高温、耐烧蚀的复合材料部件,大量应用于火箭、导弹的防热材料。迄今为止,我国已经实用化的高性能树脂基复合材料用的碳纤维、芳纶纤维、高强度玻璃纤维三大增强纤维中,只有高强度玻璃纤维已达到国际先进水平,且拥有自主知识产权,形成了小规模的产业,现阶段年产可达500吨。
2、碳纤维
碳纤维具有强度高、模量高、耐高温、导电等一系列性能,首先在航空航天领域得到广泛应用,近年来在运动器具和体育用品方面也广泛采用。据预测,土木建筑、交通运输、汽车、能源等领域将会大规模采用工业级碳纤维。1997~2000年间,宇航用碳纤维的年增长率估计为31%,而工业用碳纤维的年增长率估计会达到130%。我国的碳纤维总体水平还比较低,相当于国外七十年代中、末期水平,与国外差距达20年左右。国产碳纤维的主要问题是性能不太稳定且离散系数大、无高性能碳纤维、品种单
一、规格不全、连续长度不够、未经表面处理、价格偏高等。
3、芳纶纤维
20世纪80年代以来,荷兰、日本、前苏联也先后开展了芳纶纤维的研制开发工作。日本及俄罗斯的芳纶纤维已投入市场,年增长速度也达到20%左右。芳纶纤维比强度、比模量较高,因此被广泛应用于航空航天领域的高性能复合材料零部件(如火箭发动机壳体、飞机发动机舱、整流罩、方向舵等)、舰船(如航空母舰、核潜艇、游艇、救生艇等)、汽车(如轮胎帘子线、高压软管、摩擦材料、高压气瓶等)以及耐热运输带、体育运动器材等。
4、超高分子量聚乙烯纤维
超高分子量聚乙烯纤维的比强度在各种纤维中位居第一,尤其是它的抗化学试剂侵蚀性能和抗老化性能优良。它还具有优良的高频声纳透过性和耐海水腐蚀性,许多国家已用它来制造舰艇的高频声纳导流罩,大大提高了舰艇的探雷、扫雷能力。除在军事领域,在汽车制造、船舶制造、医疗器械、体育运动器材等领域超高分子量聚乙烯纤维也有广阔的应用前景。该纤维一经问世就引起了世界发达国家的极大兴趣和重视。
5、热固性树脂基复合材料
热固性树脂基复合材料是指以热固性树脂如不饱和聚酯树脂、环氧树脂、酚醛树脂、乙烯基酯树脂等为基体,以玻璃纤维、碳纤维、芳纶纤维、超高分子量聚乙烯纤维等为增强材料制成的复合材料。环氧树脂的特点是具有优良的化学稳定性、电绝缘性、耐腐蚀性、良好的粘接性能和较高的机械强度,广泛应用于化工、轻工、机械、电子、水利、交通、汽车、家电和宇航等各个领域。1993年世界环氧树脂生产能力为130万吨,1996年递增到143万吨,1997年为148万吨,1999年150万吨,2003年达到180万吨左右。我国从1975年开始研究环氧树脂,据不完全统计,目前我国环氧树脂生产企业约有170多家,总生产能力为50多万吨,设备利用率为80%左右。酚醛树脂具有耐热性、耐磨擦性、机械强度高、电绝缘性优异、低发烟性和耐酸性优异等特点,因而在复合材料产业的各个领域得到广泛的应用。1997年全球酚醛树脂的产量为300万吨,其中美国为164万吨。我国的产量为18万吨,进口4万吨。乙烯基酯树脂是20世纪60年展起来的一类新型热固性树脂,其特点是耐腐蚀性好,耐溶剂性好,机械强度高,延伸率大,与金属、塑料、混凝土等材料的粘结性能好,耐疲劳性能好,电性能佳,耐热老化,固化收缩率低,可常温固化也可加热固化。南京金陵帝斯曼树脂有限公司引进荷兰Atlac系列强耐腐蚀性乙烯基酯树脂,已广泛用于贮罐、容器、管道等,有的品种还能用于防水和热压成型。南京聚隆复合材料有限公司、上海新华树脂厂、南通明佳聚合物有限公司等厂家也生产乙烯基酯树脂。1971年以前我国的热固性树脂基复合材料工业主要是军工产品,70年代后开始转向民用。从1987年起,各地大量引进国外先进技术如池窑拉丝、短切毡、表面毡生产线及各种牌号的聚酯树脂(美、德、荷、英、意、日)和环氧树脂(日、德)生产技术;在成型工艺方面,引进了缠绕管、罐生产线、拉挤工艺生产线、SMC生产线、连续制板机组、树脂传递模塑(RTM)成型机、喷射成型技术、树脂注射成型技术及渔竿生产线等,形成了从研究、设计、生产及原材料配套的完整的工业体系,截止2000年底,我国热固性树脂基复合材料生产企业达3000多家,已有51家通过ISO9000质量体系认证,产品品种3000多种,总产量达73万吨/年,居世界第二位。产品主要用于建筑、防腐、轻工、交通运输、造船等工业领域。在建筑方面,有内外墙板、透明瓦、冷却塔、空调罩、风机、玻璃钢水箱、卫生洁具、净化槽等;在石油化工方面,主要用于管道及贮罐;在交通运输方面,汽车上主要有车身、引擎盖、保险杠等配件,火车上有车厢板、门窗、座椅等,船艇方面主要有气垫船、救生艇、侦察艇、渔船等;在机械及电器领域如屋顶风机、轴流风机、电缆桥架、绝缘棒、集成电路板等产品都具有相当的规模;在航空航天及军事领域,轻型飞机、尾翼、卫星天线、火箭喷管、防弹板、防弹衣、鱼雷等都取得了重大突破。
热塑性树脂基复合材料
热塑性树脂基复合材料是20世纪80年展起来的,主要有长纤维增强粒料(LFP)、连续纤维增强预浸带(MITT)和玻璃纤维毡增强型热塑性复合材料(GMT)。根据使用要求不同,树脂基体主要有PP、PE、PA、PBT、PEI、PC、PES、PEEK、PI、PAI等热塑性工程塑料,纤维种类包括玻璃纤维、碳纤维、芳纶纤维和硼纤维等一切可能的纤维品种。随着热塑性树脂基复合材料技术的不断成熟以及可回收利用的优势,该品种的复合材料发展较快,欧美发达国家热塑性树脂基复合材料已经占到树脂基复合材料总量的30%以上。
高性能热塑性树脂基复合材料以注射件居多,基体以PP、PA为主。产品有管件(弯头、三通、法兰)、阀门、叶轮、轴承、电器及汽车零件、挤出成型管道、GMT模压制品(如吉普车座椅支架)、汽车踏板、座椅等。玻璃纤维增强聚丙烯在汽车中的应用包括通风和供暖系统、空气过滤器外壳、变速箱盖、座椅架、挡泥板垫片、传动皮带保护罩等。
滑石粉填充的PP具有高刚性、高强度、极好的耐热老化性能及耐寒性。滑石粉增强PP在车内装饰方面有着重要的应用,如用作通风系统零部件,仪表盘和自动刹车控制杠等,例如美国HPM公司用20%滑石粉填充PP制成的蜂窝状结构的吸音天花板和轿车的摇窗升降器卷绳筒外壳。
云母复合材料具有高刚性、高热变形温度、低收缩率、低挠曲性、尺寸稳定以及低密度、低价格等特点,利用云母/聚丙烯复合材料可制作汽车仪表盘、前灯保护圈、挡板罩、车门护栏、电机风扇、百叶窗等部件,利用该材料的阻尼性可制作音响零件,利用其屏蔽性可制作蓄电池箱等。
我国的热塑性树脂基复合材料的研究开始于20世纪80年代末期,近十年来取得了快速发展,2000年产量达到12万吨,约占树脂基复合材料总产量的17%,,所用的基体材料仍以PP、PA为主,增强材料以玻璃纤维为主,少量为碳纤维,在热塑性复合材料方面未能有重大突破,与发达国家尚有差距。
我国复合材料的发展潜力和热点
我国复合材料发展潜力很大,但须处理好以下热点问题。
1、复合材料创新
复合材料创新包括复合材料的技术发展、复合材料的工艺发展、复合材料的产品发展和复合材料的应用,具体要抓住树脂基体发展创新、增强材料发展创新、生产工艺发展创新和产品应用发展创新。到2007年,亚洲占世界复合材料总销售量的比例将从18%增加到25%,目前亚洲人均消费量仅为0.29kg,而美国为6.8kg,亚洲地区具有极大的增长潜力。
2、聚丙烯腈基纤维发展
我国碳纤维工业发展缓慢,从CF发展回顾、特点、国内碳纤维发展过程、中国PAN基CF市场概况、特点、“十五”科技攻关情况看,发展聚丙烯腈基纤维既有需要也有可能。
3、玻璃纤维结构调整
我国玻璃纤维70%以上用于增强基材,在国际市场上具有成本优势,但在品种规格和质量上与先进国家尚有差距,必须改进和发展纱类、机织物、无纺毡、编织物、缝编织物、复合毡,推进玻纤与玻钢两行业密切合作,促进玻璃纤维增强材料的新发展。
4、开发能源、交通用复合材料市场
一是清洁、可再生能源用复合材料,包括风力发电用复合材料、烟气脱硫装置用复合材料、输变电设备用复合材料和天然气、氢气高压容器;二是汽车、城市轨道交通用复合材料,包括汽车车身、构架和车体外覆盖件,轨道交通车体、车门、座椅、电缆槽、电缆架、格栅、电器箱等;三是民航客机用复合材料,主要为碳纤维复合材料。热塑性复合材料约占10%,主要产品为机翼部件、垂直尾翼、机头罩等。我国未来20年间需新增支线飞机661架,将形成民航客机的大产业,复合材料可建成新产业与之相配套;四是船艇用复合材料,主要为游艇和渔船,游艇作为高级娱乐耐用消费品在欧美有很大市场,由于我国鱼类资源的减少、渔船虽发展缓慢,但复合材料特有的优点仍有发展的空间。
5、纤维复合材料基础设施应用
国内外复合材料在桥梁、房屋、道路中的基础应用广泛,与传统材料相比有很多优点,特别是在桥梁上和在房屋补强、隧道工程以及大型储仓修补和加固中市场广阔。
6、复合材料综合处理与再生
高分子材料的耐热性范文篇3
一、新材料
材料是社会进步的物质基础和先导,对国民经济和国防建设起着关键的支撑作用。新材料是高技术领域的重要组成部分,与信息、生命、能源并称为现代文明和社会发展的四大支柱。加强新材料的开发,对推动高新技术产业发展、促进传统产业升级换代和增强综合国力,具有重要的意义。本年度重点支持新材料领域中下列五个方面的技术和产品:1.金属材料;2.无机非金属材料;3.高分子材料;4.生物医用材料;5.精细化学品。本刊重点介绍后三种技术和产品。
高分子材料
高分子材料是新材料领域的重要组成部分,由于其具有优良的物理、化学性能和优异的加工特性,被广泛应用于信息产业、航空航天、生物医药、交通运输、机械仪表、建筑和能源等国民经济重要领域。随着新型高分子合成、改性与加工等高技术的发展,高性能高分子材料迅速崛起,新产品、新技术不断涌现。新型高分子材料的开发和广泛应用,对于推动传统产业的升级换代、新兴产业的发展壮大会起到积极的作用,必将对推动我国国民经济的发展发挥重要的作用。
本年度重点支持的方向如下。
高性能高分子结构材料
高性能高分子结构材料具有机械性能好、比强度高、耐热性好、耐腐蚀、耐磨损和易加工等特点,在各行业应用广泛,对国民经济的发展和国家安全具有重要意义。本年度重点支持:具有高强、耐高温、耐磨、高韧的高分子结构材料和复合材料;低成本化的特种工程塑料;具有特殊功能、特殊用途的高附加值热塑性树脂。
新型高分子功能材料
高分子功能材料由于其特有的功能性和专用性,在生态环境保护、信息功能化、生物医用器材、物质分离膜、能量转换和储能技术等工业领域有着极为广泛的应用。本年度重点支持:先进功能膜材料及支撑材料;光电信息高分子材料;液晶高分子材料;形状记忆高分子材料;高分子相变材料;具有特殊功能性、高附加值的高分子材料。
高分子材料的低成本化和高性能化
通用塑料的高性能化和工程塑料的低成本化,仍然是当前高分子材料领域研究、开发的重点之一,同时也是扩大通用塑料和工程塑料应用范围的一个重要措施。鼓励开发产业化制备技术和工业化应用技术。本年度重点支持:通过化学改性和/或物理改性(含纳米技术改性),性能显著提高或获得特殊性能的高分子及其复合材料;高刚性、高韧性、高电性能、高耐热或导热性聚合物合金与改性材料;新型高性能热塑性弹性体;具有特殊用途、高附加值的新型改性高分子材料。
本年度不支持:普通塑料的一般改性专用料;普通电线、电缆专用料;流延、吹塑、拉伸法生产的通用薄膜;普通管材、管件及异型材(如普通塑钢窗);以聚乙烯、聚丙烯为基材的部分降解材料;普通的PS和PU泡沫塑料等。
新型橡胶材料
新型橡胶作为三大合成材料之一,在国防工业、航空航天和交通运输等方面具有广泛的应用。为满足现代汽车工业高速、耐热、减震、密封、耐老化、耐介质、耐脉冲性的要求,优化橡胶工业产品结构,采用高性能材料,可以有效缓解资源不足和环境污染的压力。本年度重点支持:特种合成橡胶;新型橡胶功能材料及产品;为高速安全交通配套的橡胶轮胎和制品。
本年度不支持普通橡胶制品项目。
新型纤维材料
纤维是高分子材料的重要组成部分,广泛应用于纺织、信息、航空、汽车、环保、卫生、建筑等领域。我国纤维、纺织品及服装的产量均居世界第一,但产品性能档次低、附加值低,常规产品产能过剩,高档产品需进口,技术进步和产品创新仍以跟踪国外为主。新型纤维品种及其成纤高分子新品种的开发及产业化是纺织新产品创新的源头,因此必须加大技术含量高、市场前景好的新技术和新品种开发力度,加快产业化进程,推进全行业产品的升级换代,重视环境友好和清洁生产,重点支持我国自主知识产权的技术,同时支持有较高技术含量的集成创新。本年度重点支持:新型成纤聚合物开发,及应用新型成纤聚合物制备的具有特殊性能或功能的纤维;高性能纤维及其原料、半成品;环境友好及可生物降解型纤维;在确保环境保护的前提下,申报差别化纤维开发及应用项目(仅限于西部欠发达地区申报)。
本年度不支持服装面料、衬布、纱线、常规或性能仅略有改善的纤维(如:有色、异形、细旦、功能粉体添加、简单的化学改性、常规的共混等)及服装项目;不支持常规的非织造布、涂层布或层压纺织品、一般功能性纤维材料产品项目。
生态和环境友好高分子材料
随着高分子材料的迅速发展,传统高分子材料在使用过程及废弃后对环境的危害逐渐显现,白色污染已经引起了社会的关注。发展生态和环境友好高分子材料是高分子材料新的方向之一。本年度重点支持:以生物质来源的高分子材料及制品;全生物降解塑料及其制品。
本年度不支持:淀粉填充的不完全降解塑料及其制品、单纯填充的材料、废旧高分子直接回用、单纯降解塑料制品常规制备项目。
高分子材料的加工应用技术
现代科技进步迫切需要成型加工具有优异性能和特定形态的高分子材料及制品,成型加工工艺及设备也正在向高效、节能、省料、优质方向发展。通过某些物理化学和机械手段将各种形态的聚合物成型为不同用途的制品;通过对高分子材料制品表面进行改性,可制备出具有导电、磁性、压电、屏蔽、耐蚀、耐磨等单功能或多功能应用产品。本年度重点支持:具有微孔结构的复合注射成型;高比强度、大型复杂热塑性制品成型;模内优质修饰注塑成形;先进的高分子材料制品的表面改性与应用;CAD及气辅CAE辅助等高分子加工新工艺;具有显著节能减排效果的新工艺技术。
高分子材料的耐热性范文篇4
关键词:可瓷化高分子复合防火材料;硅橡胶;硅酸盐矿物
中图分类号:TB33文献标识码:A文章编号:1671-2064(2017)04-0180-01
当前我们所使用的电线电缆多以氧化镁矿物绝缘防火电缆及云母带绕包的耐火电缆为主,但这二种电缆都存在着成本较高的问题,而且遇水导电,无法起到有效的防火作用,在火灾发生过程中也无法有效的保证通电安全。这就使许多人专家学者开始深入的研究更为适宜的绝缘耐火材料。可瓷化高分子复合防火材料是一种较为优异的电线电缆材料,在高温着火后,经过瓷化的表面会转变为坚硬的陶瓷防护层,能够有效的抵御明火的烧蚀,而且具有较好的机械强度,即使水浇在上面也会不发生破裂,而且这种新型防火材料已在电线电缆中进行应用,并取得了较好的应用效果。
1可瓷化高分子复合防火材料的特性及防火机理
可瓷化高分子复合防火材料主要是在含硅高分子基体中将粘土类矿物粉末填料加入其中,同时还会加入结构控制剂和其他助剂。这其中含硅高分子主要以含有元素硅的有机聚合物为主,如硅橡胶。在有机硅高分子结构中,不仅含有有机基团,同时还含有无机结构,其将有机物与无机物集于一身,因此有机硅具有非常好的热稳定性,能够在高温领域中进行广泛应用。同时含硅高分子在常温下具有无毒无味的特点,能够耐高温、耐严寒、耐臭氧、难燃、憎水,即使在燃烧状态下含硅高分子材料也不会产生有毒气体,将其用于电线电缆绝缘材料及绕包材料十分适宜,具有安全、可靠的特性。
当前普通的电线电缆绝缘层材料多以易燃的高分子材料为主,一旦发生火灾,电线电缆绝缘层在火焰烧蚀后会产生熔融滴落,从而使铜导线在外,发生短路。但可瓷化高分子复合防火材料中是以有机硅作为基体,以粘土类矿物为填料,在高温和火焰烧蚀下呈现出较强的抗高温氧化性能,而且粘土矿物与有机硅分子结合后会在烧蚀过程中会形成较硬的陶瓷状块体,具有较强的耐高温性能,而且在火灾现场高温水浇过程中也不会发生破裂,能够对铜导线进行有效的保护。
在高温烧蚀下,可瓷化高分子复合防火材料能够与粘土粉末填料分解产物发生反应,形成部分液相和新的同相。而且在烧蚀温度不断升高及烧蚀时间延长的情况下,液相会向陶瓷网络结构中进行渗入,待冷却同化后,能够进一步强化陶瓷结构。而且在烧蚀后残留的陶瓷保护层还能够对物质对流起到阻碍作用,并防止热量的有效传输,对材料内部物质的挥发损耗具有较好的抑制作用,能够对外界热量向材料内部扩散产生有效的阻隔,从而具备非常好的防火性能。
2可瓷化高分子复合防火材料的研究进展
2.1有机硅基体
可瓷化高分子复合防火材料的基体采用的是含硅的高分子材料,即有机硅。将有机硅转换为陶瓷的技术已较成熟,为可瓷化高分子复合防火材料的制备提供了实验依据。有机硅分为硅油、硅树脂和硅橡胶3大类。硅油在室温下为液体,没有足够的强度,起到联结无机填料的作用,适合作基体材料。硅树脂是具有高度交联网状结构的聚有机硅氧烷,虽然它具有优异的热氧化稳定性,但却是一种热固性的塑料,成型后不具有柔韧性,不可随意弯折,不是制造电缆的理想材料。因此作为可瓷化高分子复合防火电缆材料的基体,应用得最为广泛的是硅橡胶。硅橡胶是唯一一类主链上不含碳原子的大分子弹性体,具有其他橡胶所不具备的独特性能,具有优良的耐高温与耐寒性,良好的耐老化性、电气绝缘性和化学稳定性,突出的表面活性和生理惰性等。同时硅橡胶还具有燃烧时少烟无毒、燃烧热值低、火焰传播速度慢等特点。
以硅橡胶为基体的各种材料具有优良的阻燃防火性能。因此以硅橡胶作为可瓷化高分子复合防火材料的基体是行之有效的。其他类型的高分子材料通过与阻燃剂复合虽然也可制备出阻燃性能相当优良的阻燃材料,但是这类材料在明火的烧蚀下容易分解挥发,不能保持原有形状,难以起到真正的防火作用。
2.2粘上矿物粉末填料
由于粘土矿物中主要以含水硅酸盐矿物为主,其具有较高的耐火度,在耐火材料制备中应用十分广泛。在可瓷论高分子复合防火材料中,以粘土矿物粉末作为填料,充当硅橡胶补强剂的作用,而且在阻燃方面也优于其他无机填料。当前层状硅酸盐矿物种类较多,将其粉末作为可瓷化高分子复合防火材料的填料,使其c低溶点的氧化物有效的进行配合使用,从而保持复合材料的高温性能,并获得较好好的中温性能,即使在低温下也能够形成坚硬的陶瓷保护层,使材料使用过程中温度范围得以扩大。
3结语
可瓷化高分子复合材料是当前一种较为新型的防火材料,不仅制备工艺简单,而且原料丰富,而且在不断研究过程中,可瓷化高分子复合防火材料的性能进一步提升。随着研究的不断深入,可瓷化高分子复合防火材料必将实现低成本工业化生产,从而使其应用更为普及,这对消防防火安全具有非常积极的意义。
参考文献
[1]王锦贵,王希光,郭祥旭.浅谈几种常用的防火材料[J].技术与市场,2010-05-15.
高分子材料的耐热性范文1篇5
在现实生活中,人们不会像电影剧情那样遭遇宇宙射线辐射而发生变异,也不会在严酷的宇宙空间中穿越变形。美国洛克希德・马丁公司认为,普通人要具备超能力,只能借助高科技材料。
科学家为我们描绘了一幅这样的蓝图:自修复式弹性聚合物可以令人像神奇先生一样,任意延伸、扭曲,变幻形状;反光材料可以让人像隐形女一样,拥有隐身的能力;硬度是钢100倍的碳纳米管,可以让人像石头人一般力大无穷;耐高温材料可以保护人在霹雳火的火焰下毫发无损。
神奇先生:伸缩技术
在材料设计上,伸缩性指的是可自修复、或可重构的能力。在没有人类干涉的情况下,自修复材料可通过重组化学键或使用病毒,实现损伤部位的自修复。事实上,这类材料目前已被应用于诸如自愈合混凝土等领域,未来或将被应用于海军舰只上的防腐涂料中。
可重构材料能在不同环境下改变自身属性。从微观尺度上看,通过吸收或放射能量,个体分子键可具备可逆的变形能力。聚合材料可以实现宏观形态变化,如放置于光或电荷下,聚合物可自动卷缩或伸展。
如今,飞机机翼的形态是固定的,但是在不同飞行阶段中,如滑行、起飞、降落等,理想的机翼形状应该有所不同。洛克希德・马丁公司材料专家安娜・保尔森称,在现实世界中,我们可以设想在飞机或汽车设计中研发应用可重构元素,如果在设计中用到可重构材料,飞机就可在飞行中优化机翼形状,提高航空燃油的利用率。
尽管利用高科技材料变身降落伞或蹦床的想法听上去有些荒诞,不过美国宇航局已受该领域研究的启发,探索开发弹性飞机机翼。
隐形女:隐形技术
要令物体消失于无形,需要科学家致力于图案与光线的研究。而隐形材料有着特殊的图案,且具有传导与隔绝元件,能管理物体周围的电磁辐射。但在隐形材料领域,科学家面临着三大挑战:改变这些图案的大小、控制三维光线,以及设计适合多波长的图案。
保尔森表示,从物理学角度来看,克服这些困难是可行的。目前,他们已经模拟出具备这些必要属性的图案。如今,研究人员正在研发新技术,制造三维纳米级图案,用来控制三维的光线。
显然,成为一名隐形超级英雄很具诱惑力,未来在我们的日常生活中,隐形技术将在美学领域大显身手,如将具备隐形特性的建筑材料应用于电力线,或者纽约帝国大厦顶部的护栏。此外,隐形材料的应用领域还有高速计算机中的光学处理器,以及高能天线中的天线材料。
石头人:纳米技术
要令人具有超高硬度,需要着眼于分子级的科学原理研究。而纳米技术就是一种纳米级的物质控制技术,其分子级介于1到100纳米之间,或百万分之一毫米。利用纳米技术,人们可以改变单个原子和分子,从而改变物质的物理、化学、生物以及光学属性。
碳是纳米技术应用的最佳原材料之一,如石墨烯就是一种由碳原子构成的二维碳材料。石墨烯的晶格是由六个碳原子围成的六边形,其厚度为一个原子层。碳原子之间结合紧密,使得石墨烯拥有极其优异的力学性质和结构刚性――由石墨烯制成的材料具有难以置信的硬度,且耐腐蚀、耐高温、耐高压。
目前,科学家正致力于研究石墨烯材料,以期将其应用于电子显示屏和医学设备。同时,对在石墨烯片上钻孔的可能性研究,将使科学家能够解决一些新问题,如纯净饮用水和电源管理。
纳米技术还带来了碳纳米管的开发应用。碳纳米管作为一维纳米材料,重量轻,体积小,六边形结构连接完美,具有许多异常的力学、电学和化学性能――硬度是钢的100倍,且比人的头发纤细10000倍。洛克希德・马丁公司研究专家米歇尔・梅恩霍德称,正是这些碳原子之间完美的连接结构,才使得碳纳米管硬度超强。现在,碳纳米管应用可见于“朱诺”号飞船的建造。
在不久的将来,一旦碳纳米管具备了节能属性,将可被广泛应用于长寿命锂电池、1TB闪存、智能电话的化学传感器、织入衣服的电子布线,以及高硬度轻质复合材料等消费品中。然而,大规模生产植入碳纳米管的材料结构目前存在很多局限性,其中最大的局限性在于大规模增加碳纳米管长度。
此外,碳纳米管研发还处于实验室阶段,研制的所谓“微型碳纳米管森林”也仅长几厘米。保尔森表示,一旦研制成数米长的碳纳米管,他们就能将其应用于超轻汽车的设计中,但由于碳纳米管只在单一方向上具有高硬度,所以在汽车设计中需多个方向将其组合起来,以使汽车拥有良好的抗震性。
目前,科学家正在研究将大量碳纳米管绞缠起来,以生产出一种超硬度的轻质面料。未来,有了石头人那样的套装后,也许人人都能变成超级大力士。
霹雳火:耐热技术
总体上来说,越坚硬有力的材料就具有越高的熔点。应用热力学原理的高科技材料,因其分子键特性可以抵抗超高温度,而要成为一种保护屏障,这种材料还必须具备弱导热性。如,一辆车(一个超人)要以超音速速度移动,就需要使用这种超耐材料,需耐得住3000华氏度(约合1648℃)的高温。
高分子材料的耐热性范文篇6
关键词:2024Al/Gr/SiC复合材料;热暴露;耐热性能;断裂机制
中图分类号:TG146.21文献标识码:A
颗粒强化铝基复合材料具有密度小、比强度和比刚度高、弹性模量高和热膨胀系数低等优点,已在航空航天、交通领域得到非常广泛的应用[1].随着近年来航空航天工业的迅猛发展对材料提出了更高的要求,为了进一步提高飞行器的性能,开发混合颗粒强化铝基复合材料越来越受到人们的关注[2-4].混合颗粒强化铝基复合材料结合了不同增强相颗粒所带来的优势,使其具有多种独特的性能,例如SiC颗粒与石墨混合强化铝基复合材料不仅具有高弹性模量,还具有良好的耐磨性能和阻尼性能[5-8].2024Al合金属于可热处理强化铝合金,耐热性也比较优异[9].通过在合金中复合添加SiC颗粒和片状石墨,可以进一步提高其模量和阻尼性能,这种混杂增强的2024Al/Gr/SiCp复合材料在航天飞行器支撑结构件上有重要的应用价值.然而,目前关于2024Al/Gr/SiCp复合材料耐热性能的报道很少.本文研究2024Al/Gr/SiCp复合材料的高温拉伸性能及长时间热暴露后的室温力学性能,同时对拉伸断口进行分析,探讨SiC颗粒和石墨对材料的耐热性能的影响.
1实验方法
实验所用的惰性气体雾化2024Al合金粉末、鳞片状石墨和SiC颗粒的形貌如图1所示.2024Al合金粉末的化学成分(质量分数)为3.53%Cu,1.28%Mg,0.2%Fe,余量为Al.石墨和SiC颗粒的加入量分别为3%和10%(质量分数)
采用真空热压粉末锭坯挤压成形法制备了2024Al,2024Al/3Gr,2024Al/3Gr/10SiCp3种复合材料板.采用的挤压温度为470℃,挤压比为22∶1,板材的截面尺寸为40mm×10mm.
将挤压板材进行峰值时效处理后,分别在150℃,200℃,250℃和300℃热暴露不同时间,测量其硬度变化规律及室温拉伸性能.采用HBRVU187.5型布洛维光学硬度计进行布氏硬度测试,加载载荷为612.9N,保荷时间为30s,每个试样测试5个点,舍去最大值和最小值后取平均值作为测量值.在Instron3369电子万能试验机上进行室温拉伸性能测试,拉伸速度为0.5mm/min,每种试样测量3个并取平均值作为测量值,拉伸试样断口形貌在HitachiS4800型场发射扫描电子显微镜(SEM)上进行观察.金相组织观察在CarlZeissAxioLabA1型光学显微镜上进行.
2实验结果
2.1微观组织
图2为2024Al/Gr/SiCp复合材料分别在150℃,200℃和300℃热暴露48h后的金相组织.从图中可以看出,2024Al合金及复合材料在不同温度热暴露48h后,在材料的金相组织中没有观察到明显的变化.2024Al合金粉末颗粒沿挤压方向被拉长,SiC颗粒及石墨均匀分布在基体中,且与基体具有良好的界面结合.比较图2(a),(d),(g)和图2(b),(e),(h)可以发现,随着热暴露温度的升高,基体合金的晶粒尺寸逐渐增大,这是因为高温下,基体合金中溶质原子的扩散速度加快,导致晶粒和第二相尺寸的增加.图2(c),(f),(i)为2024Al/3Gr/10SiC复合材料的金相组织,因SiC颗粒的加入且为挤压变形组织,在进行金相组织时无法腐蚀显现出明显的晶粒,但根据上述结果可以推断其晶粒尺寸变化趋势与基体合金大致相同.此外,复合材料增强相,尤其是硬质SiC颗粒的加入,会阻碍热暴露时晶粒的长大.
2.2硬度曲线
图3为2024Al合金及其复合材料分别在150℃,200℃,250℃和300℃热暴露96h过程中的硬度值随时间延长的变化曲线.从图中可以看出,材料热暴露后的硬度均有所下降,且随着热暴露温度升高,材料硬度下降的幅度增大;在200℃时硬度下降的幅度最小,在300℃时硬度下降的幅度最大.这是因为热暴露温度越高,溶质原子扩散速度越快,第二相长大或粗化速度也越快,同时晶粒长大的趋势也越明显.在相同温度下,开始阶段材料的硬度下降比较明显,随着保温时间的延长,最后的硬度变化曲线处于平稳状态,几乎不发生改变.比较2024Al/3Gr/10SiC复合材料与2024Al/3Gr复合材料的硬度曲线可见,加了SiC颗粒的复合材料硬度值下降幅度比未加SiC的材料的小.比较2024Al/3Gr复合材料与基体合金的硬度变化曲线发现,随着热暴露温度升高,2024Al/3Gr复合材料硬度下降幅度比2024Al合金基体在相同温度下硬度的下降幅度小.这是因为片状石墨和SiC颗粒与基体合金之间的热膨胀系数存在差异,淬火时会在基体合金中引入大量位错,对材料具有强化作用.
从整体来看,在200℃及以下热暴露时,2024Al/Gr/SiCp复合材料的硬度性能曲线比较平稳.含SiC颗粒的复合材料耐热性能最好,含石墨的复合材料耐热性能次之,基体合金的耐热性能最差.在300℃热暴露时,2024Al/Gr/SiCp复合材料的硬度性能曲线下降趋势明显加快.高温下,基体合金中位错攀移、晶粒长大及第二相粗化导致材料的硬度下降的作用比复合增强相的强化作用更明显,所以温度越高,硬度越低.通常AlCuMg系合金的正常服役温度一般在150℃以下,超过该温度后,材料的力学性能会下降[9].而本文研究制备的2024Al/Gr/SiCp复合材料具有较好的耐热性能,主要是因为加入的SiC颗粒和石墨颗粒能够阻碍热暴露过程中的晶粒长大及阻碍位错的运动.
2.3拉伸性能
图4为在不同温度下热暴露12h后材料的室温抗拉强度变化规律及拉伸曲线.由图可见,材料的强度随着热暴露温度的升高逐渐降低,但整体仍具有较高的强度.在200℃及以下,材料的整体抗拉强度下降幅度不大,具有良好的耐热性能.对比2024Al合金基体与复合材料的抗拉强度变化,可以发现基体合金的抗拉强度下降幅度更大.2024Al合金在150℃时抗拉强度为480MPa,200℃时抗拉强度为394MPa,下降了约90MPa;而2024Al/3Gr/10SiCp复合材料在150℃时抗拉强度为424MPa,200℃时抗拉强度为404MPa,下降幅度仅为20MPa.在300℃保温12h后,材料的抗拉强度下降幅度较大.这与硬度曲线变化规律分析得到的结论相吻合,在200℃及以下温度,2024Al合金及其复合材料的力学性能下降幅度较小,在300℃时力学性能快速下降.在200℃及以下温度,由于SiC颗粒及石墨的加入,能钉扎位错和晶界,阻碍位错运动和晶粒长大,有效地提高材料的耐热性能.当在300℃时,位错和晶界运动驱动力增大,晶粒及第二相长大趋势明显,材料的强度下降.
比较2024Al/Gr/SiCp复合材料室温及在150℃保温12h后的抗拉强度,可以发现,经150℃热暴露12h后,2024Al合金及复合材料的抗拉强度均有小幅的升高.部分学者[10-12\]在研究AlCuMg系铝合金的耐热性能时也发现过类似现象.魏修宇等[12]在研究2197Al合金的高温拉伸性能及长时间热暴露后的室温力学性能时发现,在低于150℃的温度下热暴露100h后,2197Al合金的强度提高了15MPa左右,将其原因归结为:合金经过160℃/16h时效处理后,仍残留有部分的过剩溶质原子,当合金在150℃及以下长时间暴露时,会二次析出细小弥散的θ'(Al2Cu)强化相.本实验的基体合金中Cu含量较高,基体中除了存在S(Al2CuMg)相,多余的Cu原子会形成θ'(Al2Cu)相.θ'相作为(Al2Cu)相的过渡相,其在150℃热暴露时在基体中析出的可能性很大.因此,θ'相的二次析出可能是2024Al合金基体及其复合材料在150℃热暴露后,强度有所提高的主要原因.
图5为2024Al合金及其复合材料在200℃下分别热暴露12h,24h和48h后的室温抗拉强度变化趋势及相应的拉伸曲线.由图可见,随着保温时间的延长,2024Al合金及其复合材料的抗拉强度均有小幅度的下降;相比于基体合金,复合材料的下降幅度更小.2024Al合金在200℃下保温48h后抗拉强度为340MPa,比未经保温处理的强度下降了140MPa;2024Al/3Gr/10SiCp复合材料在200℃下保温48h后抗拉强度仍有366MPa,比未经过保温处理的强度仅下降了21MPa.可见SiC颗粒和石墨的加入,减小了材料强度下降的幅度,提高了基体合金的耐热性能.热暴露保温时间对材料伸长率的影响不大,随着时间的延长,材料的伸长率一般都有小幅度的提高,基体合金伸长率的变化幅度在5%左右,复合材料的伸长率变化幅度在1%左右.
随着热暴露时间的延长,溶质原子扩散得更加充分,晶粒尺寸和第二相尺寸长大、位错攀移运动程度加剧,导致材料的抗拉强度下降、伸长率上升.
图6为2024Al合金及其复合材料在不同温度下热拉伸变形时的强度及相应的拉伸曲线.由图可见,随着拉伸温度的升高,2024Al合金及其复合材料的抗拉强度均逐渐下降.在200℃及以下温度,抗拉强度下降的幅度较小,在250℃及以上的温度下拉伸时,抗拉强度下降幅度较大.在200℃时,2024Al合金、2024Al/3Gr和2024Al/3Gr/10SiCp复合材料仍具有较高的力学性能,抗拉强度分别为383MPa,377MPa及372MPa.比较2024Al及其复合材料的抗拉强度可知,复合材料的抗拉强度下降幅度比基体合金的小.
2.4断口形貌
图7为2024Al合金及其复合材料分别在150℃,200℃和300℃下热暴露12h的断口形貌.由图7(a)(b)(c)可以看出,2024Al合金的断口处出现了大量的韧窝,说明在拉伸过程中基体发生了塑性变形.随着热暴露温度的升高,合金中的韧窝尺寸变
大.造成这种现象的原因与韧窝形成机理有密切联系.一般认为,韧窝主要由微孔聚合型断裂形成,微孔聚合型的断裂过程是在外力作用下,在夹杂物、第二相粒子与基体的界面处,或在晶界、相界、大量位错塞积处形成微裂纹,因相邻微裂纹的聚合产生可见微孔洞,以后孔洞长大、增殖,最后连接形成断裂.因此,韧窝的形成与材料中的第二相粒子的特征有关,Shakeri等[13]认为微孔在第二相颗粒附近形核,而且只有当颗粒尺寸在50~500nm之间才对韧窝的形成有影响.所以当热暴露温度升高时,第二相颗粒的长大或粗化造成断裂韧窝尺寸增大.一般情况下,韧窝尺寸越大,材料的塑性变形能力越好,伸长率也越高.这也解释了拉伸结果中,随着热暴露温度升高,合金的伸长率有一定程度升高的原因.
图7(d)(e)(f)和(g)(h)(i)分别为2024Al/3Gr和2024Al/Gr/10SiCp的断口形貌.由图可见,复合材料的断口形貌具有两个明显的共同特征:第一,断口处存在断裂的石墨;第二,基体合金断口中存在大量的韧窝.观察发现,随着热暴露温度的升高,韧窝尺寸没有明显的变化.在2024Al/Gr/10SiCp复合材料的断口形貌中发现了坑洞,这是由于拉伸过程中SiC被拔出基体后留下的.2024Al/3Gr与2024Al/3Gr/10SiCp复合材料的断口中韧窝尺寸变化不大,主要是受到SiC颗粒和石墨的影响.SiC颗粒和石墨的加入能阻碍基体合金在热暴露时晶粒尺寸.根据前面分析可知,颗粒尺寸对韧窝的形貌具有一定程度的影响.在一定范围内,第二相颗粒尺寸越小,韧窝尺寸也越小.
图8为2024Al合金及其复合材料分别在150℃,200℃,250℃及300℃下拉伸的断口形貌.由图可见,2024Al合金在高温下拉伸的断口具有韧性断裂的特征,断口中撕裂棱和韧窝较多.随着温度的上升,韧窝边缘被拉长的程度增大,表明高温下材料的塑性变形能力有所提高.这也解释了图6中拉伸曲线的变化情况,即随着拉伸温度升高,材料伸长率逐渐增大.2024Al/3Gr复合材料的断口中存在大量断裂的石墨,基体合金呈韧性断裂,2024Al/3Gr/10SiCp复合材料的断口处也存在断裂的石墨,但没有观察到SiC颗粒,说明在高温拉伸时SiC颗粒主要被拔出基体,基体合金呈韧性断裂.在高温下复合材料的基体合金中的韧窝呈现两种形式:小而深的韧窝,大而浅的韧窝.靠近增强相附近的韧窝小而深,距离增强相较远处的韧窝大而浅.这是因为颗粒附近的基体合金协调变形受到约束,导致韧窝小而深;而距离颗粒较远的基体合金可以充分协调变形,因而表现为断口上的韧窝大而浅.
3分析讨论
材料在热暴露过程中力学性能下降的主要原因是:基体的晶粒长大、溶质原子的急剧扩散以及强化相的长大或者粗化.因此提高材料的耐热性能的主要途径有:阻碍晶粒长大、选择高温稳定的第二相及添加陶瓷颗粒等.基体合金中析出的第二相的热稳定性与其组成元素的扩散速率有关,同时第二相的形貌与基体的界面有关;其组成元素扩散速率越快,第二相尺寸越容易长大.增强颗粒自身性能稳定,在高温下尺寸不发生变化,能有效阻碍位错的滑移和晶界的迁移,提高材料的热稳定性能[14].
2024Al/Gr/SiCp复合材料中主要的析出相为S(Al2CuMg)相和θ(Al2Cu)相.其中弥散强化相θ相具有正方结构,为类球形,常温下具有较好的强化效果,但高温下容易长大;S(Al2CuMg)相在常温下具有良好的强化效果,且在高温下也具有一定的强化作用.在200℃左右时,S相和θ相发生粗化,导致合金的性能下降,通常采用添加Ag、稀土元素等以形成复杂的耐高温相来提高材料的热稳定性能[15-16].本实验中没有添加此类元素,但材料在200℃及以下温度具有良好的耐热性能,随着保温时间的延长,材料的硬度和强度并没有出现大幅降低.首先增强相SiC颗粒和石墨能改善材料的耐热性能,SiC颗粒和石墨高温下很稳定,尺寸几乎不发生变化,在高温下能有效地阻碍位错的运动和晶粒的长大,提高材料的强度.其次,由于增强相SiC颗粒与基体热膨胀系数差异很大,热暴露实验后,材料中形成大量的位错,大量位错与基体中的第二相相互作用,形成位错缠结或者位错网结构,能有效提高材料的强度,提高材料的耐热性能.
4结论
1)2024Al合金及其复合材料在200℃及以下热暴露时,随着时间的延长,材料组织没有明显改变,其硬度和强度没有出现明显下降,具有较高的热稳定性能.SiC颗粒和石墨均能提高复合材料的热稳定性,但SiC颗粒的影响作用更明显.
2)在300℃热暴露时,2024Al合金及其复合材料的硬度和强度出现了较大幅度的降低.但2024Al/Gr/SiCp复合材料的硬度和强度下降幅度均比2024Al合金的低.
3)2024Al及其复合材料的抗拉强度随着拉伸温度升高而下降,在200℃拉伸时,2024Al/3Gr/10SiCp的抗拉强度达到372MPa.复合材料的强度下降幅度比2024Al合金的小,说明SiC颗粒与石墨加入能提高材料的耐热性能.
4)高温拉伸及热暴露后的2024Al合金的断裂机制为韧性断裂,2024Al/Gr/SiCp复合材料的断裂机制为基体韧性断裂、石墨断裂及SiC颗粒与界面分离的混合断裂机制.
参考文献
[1]张大童,李元元,龙雁.铝基复合材料研究进展[J].轻合金加工技术,2000,28(1):5-10.
ZHANGDatong,LIYuanyuan,LONGYan.Areviewontheprogressofaluminummatrixcomposites[J].LightAlloyFabrication,2000,28(1):5-10.(InChinese)
[2]PANDIG,MUTHUSAMYS.Areviewonmachiningandtribologicalbehaviorsofaluminumhybridcomposites[J].ProcediaEngineering,2012,38:1399-1408.
[3]SHOWBK,MONDALDK,BISWASK,etal.Developmentofanovel6351AlC(Al4SiC4+SiC)hybridcompositewithenhancedmechanicalproperties[J].MaterialsScienceandEngineering:A,2013,579:136-149.
[4]JAMESSJ,VENKATESANK,KUPPANP,etal.HybridaluminummetalmatrixcompositereinforcedwithSiCandTiB2[J].ProcediaEngineering,2014,97:1018-1026.
[5]MAHDAVIS,AKHLAGHIF.EffectoftheSiCparticlesizeonthedryslidingwearbehaviorofSiCandSiCGrreinforcedAl6061composites[J].JournalofMaterialsScience,2011,46(24):7883-7894.
[6]ASLAM,KHANDANIST.Roleofhybridratioinmicrostructural,mechanicalandslidingwearpropertiesoftheAl5083/Graphitep/Al2O3pasurfacehybridnanocompositefabricatedviafrictionstirprocessingmethod[J].MaterialsScienceandEngineering:A,2013,559:549-557.
[7]GUJ,ZHANGX,GUM,etal.Internalfrictionpeakanddampingmechanisminhighdamping6061Al/SiCp/Grhybridmetalmatrixcomposite[J].JournalofAlloysandCompounds,2004,372(1):304-308.
[8]GUIMC,WANGDB,WUJJ,etal.DeformationanddampingbehaviorsoffoamedAlSiSiCpcomposite[J].MaterialsScienceandEngineering:A,2000,286(2):282-288.
[9]刘兵,彭超群,王日初,等.大飞机用铝合金的研究现状及展望[J].中国有色金属学报,2010,20(9):1705-1715.
LIUBing,PENGChaoqun,WANGRichu,etal.Recentdevelopmentandprospectsforgiantplanealuminumalloys[J].TheChineseJournalofNonferrousMetals,2010,20(9):1705-1715.(InChinese)
[10]KERRMJ,SWEETED,BENNETTCG,etal.Effectofalkalimetalimpuritiesonthelowtemperaturethermalstabilityof2090AlCuLialloys[J].MaterialsScienceForum,1996,217:1079-1084.
[11]GAOX,NIEJF,MUDDLEBC.Secondaryhardeningin2090(AlCuLi)alloy[C]//Proceedingofthe6thInternationalConferenceonAluminumAlloys.Toyohashi:TheJapanInstituteofLightMetals,1998:651-656.
[12]魏修宇,郑子樵,李世晨,等.2197铝锂合金的耐热性能[J].中国有色金属学报,2007,17(9):1417-1422.
WEIXiuyu,ZHENGZiqiao,LIShichen,etal.Heatresistantpropertiesof2197AlLialloy[J].TheChineseJournalofNonferrousMetals,2007,17(9):1417-1422.(InChinese)
[13]SHAKERIHR,WANGZ.EffectofalternativeagingprocessonthefractureandinterfacialpropertiesofparticulateAl2O3reinforcedAl(6061)metalmatrixcomposite[J].MetallurgicalandMaterialsTransactionsA,2002,33(6):1699-1713.
[14]贺毅强,陈振华,王娜,等.SiCp/AlFeVSi复合材料组织与性能的热稳定性[J].中国有色金属学报,2008,18(3):433-438.
HEYiqiaing,CHENZhenhua,WANGNa,etal.ThermostabilityofhardnessandmicrostructureofSiCp/AlFeVSicomposite[J].TheChineseJournalofNonferrousMetals,2008,18(3):433-438.(InChinese)
[15]宋G,肖代红,贺跃辉,等.稀土元素对AlCuMgAg合金显微组织影响的研究进展[J].中国有色金属学报,2009,19(8):1355-1365.
SONGMin,XIAODaihong,HEYuehui,etal.ResearchprogressofeffectofrareearthelementsonmicrostructuresofAlCuMgAgalloys[J].TheChineseJournalofNonferrousMetals,2009,19(8):1355-1365.(InChinese)
高分子材料的耐热性范文篇7
复合材料是指由两种或两种以上不同物质以不同方式组合而成的材料,它可以发挥各种材料的优点,克服单一材料的缺陷,扩大材料的应用范围。由于复合材料具有重量轻、强度高、加工成型方便、弹性优良、耐化学腐蚀和耐候性好等特点,已逐步取代木材及金属合金,广泛应用于航空航天、汽车、电子电气、建筑、健身器材等领域,在近几年更是得到了飞速发展。
随着科技的发展,树脂与玻璃纤维在技术上不断进步,生产厂家的制造能力普遍提高,使得玻纤增强复合材料的价格成本已被许多行业接受,但玻纤增强复合材料的强度尚不足以和金属匹敌。因此,碳纤维、硼纤维等增强复合材料相继问世,使高分子复合材料家族更加完备,已经成为众多产业的必备材料。目前全世界复合材料的年产量已达550多万吨,年产值达1300亿美元以上,若将欧、美的军事航空航天的高价值产品计入,其产值将更为惊人。从全球范围看,世界复合材料的生产主要集中在欧美和东亚地区。近几年欧美复合材料产需均持续增长,而亚洲的日本则因经济不景气,发展较为缓慢,但中国尤其是中国内地的市场发展迅速。据世界主要复合材料生产商ppg公司统计,2000年欧洲的复合材料全球占有率约为32%,年产量约200万吨。与此同时,美国复合材料在20世纪90年代年均增长率约为美国gdp增长率的2倍,达到4%~6%。2000年,美国复合材料的年产量达170万吨左右。特别是汽车用复合材料的迅速增加使得美国汽车在全球市场上重新崛起。亚洲近几年复合材料的发展情况与政治经济的整体变化密切相关,各国的占有率变化很大。总体而言,亚洲的复合材料仍将继续增长,2000年的总产量约为145万吨,预计2005年总产量将达180万吨。
从应用上看,复合材料在美国和欧洲主要用于航空航天、汽车等行业。2000年美国汽车零件的复合材料用量达14.8万吨,欧洲汽车复合材料用量到2003年估计可达10.5万吨。而在日本,复合材料主要用于住宅建设,如卫浴设备等,此类产品在2000年的用量达7.5万吨,汽车等领域的用量仅为2.4万吨。不过从全球范围看,汽车工业是复合材料最大的用户,今后发展潜力仍十分巨大,目前还有许多新技术正在开发中。例如,为降低发动机噪声,增加轿车的舒适性,正着力开发两层冷轧板间粘附热塑性树脂的减振钢板;为满足发动机向高速、增压、高负荷方向发展的要求,发动机活塞、连杆、轴瓦已开始应用金属基复合材料。为满足汽车轻量化要求,必将会有越来越多的新型复合材料将被应用到汽车制造业中。与此同时,随着近年来人们对环保问题的日益重视,高分子复合材料取代木材方面的应用也得到了进一步推广。例如,用植物纤维与废塑料加工而成的复合材料,在北美已被大量用作托盘和包装箱,用以替代木制产品;而可降解复合材料也成为国内外开发研究的重点。
另外,纳米技术逐渐引起人们的关注,纳米复合材料的研究开发也成为新的热点。以纳米改性塑料,可使塑料的聚集态及结晶形态发生改变,从而使之具有新的性能,在克服传统材料刚性与韧性难以相容的矛盾的同时,大大提高了材料的综合性能。
树脂基复合材料的增强材料
树脂基复合材料采用的增强材料主要有玻璃纤维、碳纤维、芳纶纤维、超高分子量聚乙烯纤维等。
1、玻璃纤维
目前用于高性能复合材料的玻璃纤维主要有高强度玻璃纤维、石英玻璃纤维和高硅氧玻璃纤维等。由于高强度玻璃纤维性价比较高,因此增长率也比较快,年增长率达到10%以上。高强度玻璃纤维复合材料不仅应用在军用方面,近年来民用产品也有广泛应用,如防弹头盔、防弹服、直升飞机机翼、预警机雷达罩、各种高压压力容器、民用飞机直板、体育用品、各类耐高温制品以及近期报道的性能优异的轮胎帘子线等。石英玻璃纤维及高硅氧玻璃纤维属于耐高温的玻璃纤维,是比较理想的耐热防火材料,用其增强酚醛树脂可制成各种结构的耐高温、耐烧蚀的复合材料部件,大量应用于火箭、导弹的防热材料。迄今为止,我国已经实用化的高性能树脂基复合材料用的碳纤维、芳纶纤维、高强度玻璃纤维三大增强纤维中,只有高强度玻璃纤维已达到国际先进水平,且拥有自主知识产权,形成了小规模的产业,现阶段年产可达500吨。
2、碳纤维
碳纤维具有强度高、模量高、耐高温、导电等一系列性能,首先在航空航天领域得到广泛应用,近年来在运动器具和体育用品方面也广泛采用。据预测,土木建筑、交通运输、汽车、能源等领域将会大规模采用工业级碳纤维。1997~2000年间,宇航用碳纤维的年增长率估计为31%,而工业用碳纤维的年增长率估计会达到130%。我国的碳纤维总体水平还比较低,相当于国外七十年代中、末期水平,与国外差距达20年左右。国产碳纤维的主要问题是性能不太稳定且离散系数大、无高性能碳纤维、品种单一、规格不全、连续长度不够、未经表面处理、价格偏高等。
3、芳纶纤维
20世纪80年代以来,荷兰、日本、前苏联也先后开展了芳纶纤维的研制开发工作。日本及俄罗斯的芳纶纤维已投入市场,年增长速度也达到20%左右。芳纶纤维比强度、比模量较高,因此被广泛应用于航空航天领域的高性能复合材料零部件(如火箭发动机壳体、飞机发动机舱、整流罩、方向舵等)、舰船(如航空母舰、核潜艇、游艇、救生艇等)、汽车(如轮胎帘子线、高压软管、摩擦材料、高压气瓶等)以及耐热运输带、体育运动器材等。
4、超高分子量聚乙烯纤维
超高分子量聚乙烯纤维的比强度在各种纤维中位居第一,尤其是它的抗化学试剂侵蚀性能和抗老化性能优良。它还具有优良的高频声纳透过性和耐海水腐蚀性,许多国家已用它来制造舰艇的高频声纳导流罩,大大提高了舰艇的探雷、扫雷能力。除在军事领域,在汽车制造、船舶制造、医疗器械、体育运动器材等领域超高分子量聚乙烯纤维也有广阔的应用前景。该纤维一经问世就引起了世界发达国家的极大兴趣和重视。
5、热固性树脂基复合材料
热固性树脂基复合材料是指以热固性树脂如不饱和聚酯树脂、环氧树脂、酚醛树脂、乙烯基酯树脂等为基体,以玻璃纤维、碳纤维、芳纶纤维、超高分子量聚乙烯纤维等为增强材料制成的复合材料。环氧树脂的特点是具有优良的化学稳定性、电绝缘性、耐腐蚀性、良好的粘接性能和较高的机械强度,广泛应用于化工、轻工、机械、电子、水利、交通、汽车、家电和宇航等各个领域。1993年世界环氧树脂生产能力为130万吨,1996年递增到143万吨,1997年为148万吨,1999年150万吨,2003年达到180万吨左右。我国从1975年开始研究环氧树脂,据不完全统计,目前我国环氧树脂生产企业约有170多家,总生产能力为50多万吨,设备利用率为80%左右。酚醛树脂具有耐热性、耐磨擦性、机械强度高、电绝缘性优异、低发烟性和耐酸性优异等特点,因而在复合材料产业的各个领域得到广泛的应用。1997年全球酚醛树脂的产量为300万吨,其中美国为164万吨。我国的产量为18万吨,进口4万吨。乙烯基酯树脂是20世纪60年展起来的一类新型热固性树脂,其特点是耐腐蚀性好,耐溶剂性好,机械强度高,延伸率大,与金属、塑料、混凝土等材料的粘结性能好,耐疲劳性能好,电性能佳,耐热老化,固化收缩率低,可常温固化也可加热固化。南京金陵帝斯曼树脂有限公司引进荷兰atlac系列强耐腐蚀性乙烯基酯树脂,已广泛用于贮罐、容器、管道等,有的品种还能用于防水和热压成型。南京聚隆复合材料有限公司、上海新华树脂厂、南通明佳聚合物有限公司等厂家也生产乙烯基酯树脂。
1971年以前我国的热固性树脂基复合材料工业主要是军工产品,70年代后开始转向民用。从1987年起,各地大量引进国外先进技术如池窑拉丝、短切毡、表面毡生产线及各种牌号的聚酯树脂(美、德、荷、英、意、日)和环氧树脂(日、德)生产技术;在成型工艺方面,引进了缠绕管、罐生产线、拉挤工艺生产线、smc生产线、连续制板机组、树脂传递模塑(rtm)成型机、喷射成型技术、树脂注射成型技术及渔竿生产线等,形成了从研究、设计、生产及原材料配套的完整的工业体系,截止2000年底,我国热固性树脂基复合材料生产企业达3000多家,已有51家通过iso9000质量体系认证,产品品种3000多种,总产量达73万吨/年,居世界第二位。产品主要用于建筑、防腐、轻工、交通运输、造船等工业领域。在建筑方面,有内外墙板、透明瓦、冷却塔、空调罩、风机、玻璃钢水箱、卫生洁具、净化槽等;在石油化工方面,主要用于管道及贮罐;在交通运输方面,汽车上主要有车身、引擎盖、保险杠等配件,火车上有车厢板、门窗、座椅等,船艇方面主要有气垫船、救生艇、侦察艇、渔船等;在机械及电器领域如屋顶风机、轴流风机、电缆桥架、绝缘棒、集成电路板等产品都具有相当的规模;在航空航天及军事领域,轻型飞机、尾翼、卫星天线、火箭喷管、防弹板、防弹衣、鱼雷等都取得了重大突破。
热塑性树脂基复合材料
热塑性树脂基复合材料是20世纪80年展起来的,主要有长纤维增强粒料(lfp)、连续纤维增强预浸带(mitt)和玻璃纤维毡增强型热塑性复合材料(gmt)。根据使用要求不同,树脂基体主要有pp、pe、pa、pbt、pei、pc、pes、peek、pi、pai等热塑性工程塑料,纤维种类包括玻璃纤维、碳纤维、芳纶纤维和硼纤维等一切可能的纤维品种。随着热塑性树脂基复合材料技术的不断成熟以及可回收利用的优势,该品种的复合材料发展较快,欧美发达国家热塑性树脂基复合材料已经占到树脂基复合材料总量的30%以上。
高性能热塑性树脂基复合材料以注射件居多,基体以pp、pa为主。产品有管件(弯头、三通、法兰)、阀门、叶轮、轴承、电器及汽车零件、挤出成型管道、gmt模压制品(如吉普车座椅支架)、汽车踏板、座椅等。玻璃纤维增强聚丙烯在汽车中的应用包括通风和供暖系统、空气过滤器外壳、变速箱盖、座椅架、挡泥板垫片、传动皮带保护罩等。
滑石粉填充的pp具有高刚性、高强度、极好的耐热老化性能及耐寒性。滑石粉增强pp在车内装饰方面有着重要的应用,如用作通风系统零部件,仪表盘和自动刹车控制杠等,例如美国hpm公司用20%滑石粉填充pp制成的蜂窝状结构的吸音天花板和轿车的摇窗升降器卷绳筒外壳。
云母复合材料具有高刚性、高热变形温度、低收缩率、低挠曲性、尺寸稳定以及低密度、低价格等特点,利用云母/聚丙烯复合材料可制作汽车仪表盘、前灯保护圈、挡板罩、车门护栏、电机风扇、百叶窗等部件,利用该材料的阻尼性可制作音响零件,利用其屏蔽性可制作蓄电池箱等。
我国的热塑性树脂基复合材料的研究开始于20世纪80年代末期,近十年来取得了快速发展,2000年产量达到12万吨,约占树脂基复合材料总产量的17%,,所用的基体材料仍以pp、pa为主,增强材料以玻璃纤维为主,少量为碳纤维,在热塑性复合材料方面未能有重大突破,与发达国家尚有差距。
我国复合材料的发展潜力和热点
我国复合材料发展潜力很大,但须处理好以下热点问题。
1、复合材料创新
复合材料创新包括复合材料的技术发展、复合材料的工艺发展、复合材料的产品发展和复合材料的应用,具体要抓住树脂基体发展创新、增强材料发展创新、生产工艺发展创新和产品应用发展创新。到2007年,亚洲占世界复合材料总销售量的比例将从18%增加到25%,目前亚洲人均消费量仅为0.29kg,而美国为6.8kg,亚洲地区具有极大的增长潜力。
2、聚丙烯腈基纤维发展
我国碳纤维工业发展缓慢,从cf发展回顾、特点、国内碳纤维发展过程、中国pan基cf市场概况、特点、“十五”科技攻关情况看,发展聚丙烯腈基纤维既有需要也有可能。
3、玻璃纤维结构调整
我国玻璃纤维70%以上用于增强基材,在国际市场上具有成本优势,但在品种规格和质量上与先进国家尚有差距,必须改进和发展纱类、机织物、无纺毡、编织物、缝编织物、复合毡,推进玻纤与玻钢两行业密切合作,促进玻璃纤维增强材料的新发展。
4、开发能源、交通用复合材料市场
一是清洁、可再生能源用复合材料,包括风力发电用复合材料、烟气脱硫装置用复合材料、输变电设备用复合材料和天然气、氢气高压容器;二是汽车、城市轨道交通用复合材料,包括汽车车身、构架和车体外覆盖件,轨道交通车体、车门、座椅、电缆槽、电缆架、格栅、电器箱等;三是民航客机用复合材料,主要为碳纤维复合材料。热塑性复合材料约占10%,主要产品为机翼部件、垂直尾翼、机头罩等。我国未来20年间需新增支线飞机661架,将形成民航客机的大产业,复合材料可建成新产业与之相配套;四是船艇用复合材料,主要为游艇和渔船,游艇作为高级娱乐耐用消费品在欧美有很大市场,由于我国鱼类资源的减少、渔船虽发展缓慢,但复合材料特有的优点仍有发展的空间。
5、纤维复合材料基础设施应用
国内外复合材料在桥梁、房屋、道路中的基础应用广泛,与传统材料相比有很多优点,特别是在桥梁上和在房屋补强、隧道工程以及大型储仓修补和加固中市场广阔。
6、复合材料综合处理与再生
高分子材料的耐热性范文篇8
关键词聚酰亚胺;研究进展;性能;合成;改性
中图分类号TQ323.7文献标识码A文章编号1674-6708(2010)30-0087-03
0引言
聚酰亚胺(PI)是指主链含有酰亚胺环的一类聚合物,刚性酰亚胺结构赋予聚酰亚胺独特的性能,使它具有很好的耐热性及优异的力学、电、耐辐照、耐溶剂等性能。在高温下具备的卓越性能能够与某些金属相媲美,此外,它还具有优良的化学稳定性、坚韧性、耐磨性、阻燃性、电绝缘性以及其它机械性能,已被广泛应用于航空航天、核电和微电子领域[1]。
材料与我们日常生活紧密相关,对材料的研究主要是开发新材料和对材料的改性,前者已经快要走到尽头了,要开发一种新材料已经是很困能的事了,所以对材料的改性显得尤为重要。聚酰亚胺以其独特的优点而得到广泛的应用,为了不断适应当今科技日新月异的发展,对其进行改性研究已势在必行,本文主要介绍了聚酰亚胺在改性方面的研究现状。
1聚酰亚胺的性能
聚酰亚胺由于其分子中含有的芳杂环结构单元,因此,聚酰亚胺具有其他高分子材料无法比拟优越性能:1)优良的耐温性能;2)优异的机械性能;3)优异的介电性能和电性能;4)化学性质稳定;5)无毒性及环境友好性等等。
2聚酰亚胺的合成
聚酰亚胺在合成上具有多种途径,根据分子中酰亚胺环的形成方式,主要分为两大类:第一类合成方法是在聚合反应或大分子反应中形成酰亚胺环;第二类合成方法是以含有酰亚胺环的单体合成聚酰亚胺。根据酰亚胺环的形成方式,第一类合成方法又可以分为以下4种合成路线[2]。
1)一步法合成法:二酐和二胺在高沸点溶剂中直接聚合生成聚酰亚胺,如下式:
2)两步合成法:先由二酐和二胺获得聚酰胺酸,再通过加热或化学方法使分子内脱水,闭环生成聚酰亚胺,如下式:
3)三步合成法:该方法是经聚异酰亚胺得到聚酰亚胺的方法,是聚酰胺酸在脱水剂的作用下脱水成环先生成聚异酰亚胺,然后再在催化剂的作用下异构化成聚酰亚胺。聚异酰亚胺作为聚酰亚胺的前躯体,结构稳定且热处理时不会产生水等低分子物质,能够得到性能优良的聚酰亚胺。
4)气相沉积法:主要用于制备聚酰亚胺薄膜,在高温下将二酸酐与二胺直接以气流的形式输送到混炼机内进行混炼后制成薄膜,这是由单体直接合成聚酰亚胺涂层的方法。
3聚酰亚胺的改性
由于聚酰亚胺大分子的刚性,使材料加工存在一定困难。未经改性的聚酰亚胺材料也存在一些缺点,如粘结性能不理想、固化温度高,合成工艺要求高。为了克服这些缺点,不断提高聚酰亚胺材料的性能及应用领域,人们在聚酰亚胺改性研究上主要进行了以下工作:
3.1共混改性
共混改性是聚合物改性常用的方法,它在聚酰亚胺的改性中也得到了应用。聚酰亚胺可与其他有机物或无机物共混复合,把不同材料的优异性能进行组合,使其具有一些新的功能[3]。常采用的共混改性物有环氧树脂(EP)、热塑性聚氨酯(TPUR)、聚四氟乙烯(PTFE)、聚醚醚酮(PEEK)等。
PI与PTFE共混改性:黄丽等[4]用聚四氟乙烯作为热固性聚酰亚胺的减摩增韧材料,采用简单的机械、溶液、胶体磨及气流粉碎共混4种方法制备了共混物,并对聚四氟乙烯在共混过程中粒径的变化、对共混材料摩擦磨损性能和微观结构的影响进行了研究与探讨。研究结果表明,气流共混法制备的共混物中聚四氟乙烯粒径变小,共混材料的冲击强度有所提高;同时聚四氟乙烯粒径的减小、数量的增多均有利于向摩擦面转移,缩短材料达到摩擦动态平衡的时间,从而提高了共混材料的摩擦磨损性能。
PI与EP共混改性:环氧树脂具有优异的粘结性、良好的热性能和力学性能,将其与聚酰亚胺共混,能使改性产物在耐热、粘结强度和剪切强度方面得到提高,如缩合型聚酰亚胺的中间体聚酰胺酸(PAA)与环氧树脂共混获得一种性能优异的胶粘剂,该共混物不仅保持了聚酰亚胺的高耐热性,同时提高了聚酰亚胺的粘附性[5]。
PI与PEEK共混改性:来育梅等[6]采用机械共混方式,以聚醚醚酮为改性剂对聚酰亚胺进行改性,制备了热塑性聚酰亚胺/聚醚醚酮(TPI/PEEK)共混物。研究结果表明,制备的共混物的结晶温度和熔点与TPI的含量有关,随着TPI含量的减少,共混物的结晶温度和熔点均有所升高,与未经改性的TPI相比,在高温时的力学性能得到了改善,材料的加工性能也得到了改善。
3.2共聚改性
在两步法合成中,当加入第三种单体组合成两种二酐和一种二胺或是两种二胺一种二酐时,制得的聚合物性能会发生改变。如:全部用全芳香族的二酐或二胺,合成材料的耐热性和强度有所提高;若使用脂肪族的二酐或二胺,溶解性会适当增加,再加入某些特殊性能的嵌段后,便能合成所需特殊性能的聚酰亚胺共聚物。
刘蓉[7]等中采用双酚A二酐作为第三单体,与含氟二胺单体6FHP、二酐单体6FDA缩聚,合成了新型三单体共聚型含氟聚酰亚胺材料,三单体缩聚后得到的FAPI重均分子量高达1973.2,分散度最低达到1.2735;共聚物具有高热稳定性,柔韧性好,断裂伸长率高达152.5%,机械强度高达1280MPa。与二单体含氟聚酰亚胺(FPI)相比,FAPI的热稳定性更高、力学性能显著提高,而传输损耗仍较低,但综合性能优异。
3.3结构改性
此类改性是在聚酰亚胺大分子链上引进柔性基团,如醚键、酮键、烷基等,在侧链上引入大的基团,如苯基、正丁基、三氟甲基等,设计合成不对称或扭曲非共平面结构等,将这些方法结合起来可得到具有独特性能的聚酰亚胺,具体如下:
1)主链上引入柔性基团
在主链中引入柔性结构单元,如醚键、酮键、烷基等,例如含硅氧烷的柔性链段的硅氧烷嵌段共聚物,由于Si―O键键能高、热稳定性好,且键的旋转自由性较大,可以便于材料的加工成型,提高柔韧性及粘附性能。
刘金刚[8]等对砜基取代高折射、高透明聚酰亚胺材料的合成及性能进行了研究。在研究中,首先合成了含有砜基和硫醚键的二胺单体BADPS(如图1),再采用BADPS分别与4种二酐单体(BPDA、ODPA、3SDEA、CBDA)采用两步聚合工艺制备了一系列聚酰亚胺(如图2)。改性的聚酰亚胺薄膜具有良好的热稳定性、可见光波长范围内有优良的透明性(10mm厚的聚酰亚胺薄膜在450nm处的透光率超过80%)、高折射率与低双折射等综合性能。
2)功能性侧基的引入
引入的功能性侧基一般为有机硅氧烷侧基、生色侧基、含炔侧基等。引入降低分子间作用力的功能性侧基后,不会破坏分子链的刚性,不仅提高了聚酰亚胺的溶解性和加工性,而且保持了其耐高温性能,获得的是功能化高分子材料。
王大明等[9]以双酚A二醚二酐(BPADA)和3-乙炔苯胺(APA)为原料,先合成一种热固性可交联的聚酰亚胺预聚体,再分别与不同结构的热塑性聚酰亚胺共混,对其进行增韧改性,通过调节热塑性聚酰亚胺添加量,引入结构相似且含有更多柔性基团的热塑性聚酰亚胺,得到了热固/热塑性聚酰亚胺复合膜,研究结果表明,其相分离结构使体系的机械性能得到改善,同时也保持了原有的优异热性能。
近年来,报道较多的是将含氟取代基引入到聚酰亚胺的结构中。氟原子的引入可以在保持聚酰亚胺优良综合性能的同时,又赋予制品其他独特性能,如降低制品颜色、吸湿率等等。由于含氟聚酰亚胺材料性能优于未经改性的材料,含氟聚酰亚胺已经成为研究热点课题[10]。鲁云华等[11]利用利用含氟二胺单体分别与四种二酐单体制备出五种聚酰亚胺薄膜,该类含氟聚酰亚胺薄膜在可见光波长范围内具有优异的光学透明性,450nm处的透光率为84.6%,且5种含氟聚酰亚胺薄膜在光通讯波段1.30μm和1.55μm均无明显吸收,且这五种含氟聚酰亚胺薄膜的玻璃化转变温度(Tg)均在200℃以上。张丽娟等[12]制备了一种无色透明的含氟聚酰亚胺薄膜,对该薄膜性能进行研究的结果表明,含氟取代基及间位取代结构是制备无色透明聚酰亚胺的一条颇具前途的路线,且不会牺牲材料的耐热稳定性及力学性能。
3)引入扭曲和非共平面结构
全芳香型的聚酰亚胺分子链刚性大,分子间存在强烈的相互作用,导致成型加工困难。要克服这个缺点的方法之一就是制备可溶解的聚酰亚胺,在其分子链中引入可扭曲和非平面结构,从而降低了分子间作用力,提高了溶解性能。FumingLi等人[13]采用了4,4’-二氨基-2,2’-双取代联苯类化合物与6FDA通过一步法生成一系列的含氟聚酰亚胺,既可溶于常用有机溶剂,又具有极佳的成膜能力,同时使聚酰亚胺的耐热性、热氧化稳定性和光学性能得以保持;由于在联苯二胺的2,2’位引入双取代基,形成扭曲的非共平面,使聚酰亚胺的结晶度可降低至无定形状态。
3.4超支化结构改性
将超支化结构引入聚酰亚胺分子链中,可以合成可溶性的超支化聚酰亚胺(HBPIs)[14]。HBPIs同时具有高支化和酰亚胺结构,使其不仅具有超支化聚合物的良好溶解性能和低熔融粘度等特征,而且还具有聚酰亚胺的耐热性和介电性质优良等优点,加工性能也得到了很大的改善。
2000年,Kakimoto[15]研究小组年完成了真正意义上的超支化聚酰亚胺的合成,并成功地制备出一种变形AB2型单体―3,5-(4-氨基苯氧基)-二苯醚3’,4’-二羧酸甲酯。在催化剂2,3-二氢-2-硫-3-苯丙唑基磷酸酯(DBOP)的作用下,该单体先通过聚合得到预聚体,再对预聚体进行封端、改性和亚胺化得到HBPIs。
虽然HBPIs正逐渐地应用到各个领域中,但是由于HBPIs是一个全新的研究领域,仍然普遍存在合成方法相对单一、表征和功能化手段欠缺、应用还不成熟等不足等缺点。
4聚酰亚胺材料的应用
由于聚酰亚胺在合成上工艺上的不断提高,在聚合物中像聚酰亚胺这样应用如此广泛、且在许多方面都显示优异性能的材料并不多见,所以受到了极大的重视。从其产生发展至今,已经广泛用于薄膜、涂料、先进复合材料、纤维、泡沫材料、工程塑料、胶粘剂、分离膜、光刻胶等多个领域。如聚酰亚胺泡沫材料以其优异的隔热、隔声及阻燃性能,被广泛用于石油钻井、航空航天领域。
5结论
随着航空、航天科技及微电子行业的发展,聚酰亚胺材料将会越来越受到重视,根据应用的需要合成出各种性能优异的聚酰亚胺材料将得到大力发展;同时,不同结构和性能的聚酰亚胺材料的出现,也会不断地扩大其应用领域。
参考文献
[1]丁孟贤.聚酰亚胺化学、结构与性能的关系及材料[M].北京科学出版社,2006.
[2]曹红癸.聚酰亚胺性能及合成方法[J].化学推进剂与高分子材料,2008,6(3):24-25.
[3]吴小军,刘西强.聚酰亚胺共混和复合改性的研究进展[J],2009,37(2):76-79.
[4]黄丽,徐定宇.聚酰亚胺/聚四氟乙烯合金共混工艺的研究[J].高分子材料科学与工程,1999,15(3):81-84.
[5]赵石林,秦传香.聚酰亚胺/环氧树脂共混胶粘剂的热性能分析[J].粘结,2000,21(4):7-9.
[6]来育梅,王伟.热塑性聚酰亚胺/聚醚醚酮机械共混物的研究[J].机械工程材料,2006,30(7):25-28.
[7]刘蓉,周钰明.三单体共聚型含氟聚酰亚胺的研究[J].功能材料,2008,39(8):1249-1252.
[8]刘金刚,张秀敏.砜基取代高折射率高透明性聚酰亚胺的合成与性能[J].功能材料,2008,39(3):460-464.
[9]王大明,党国栋.乙炔基封端聚酰亚胺增韧改性的相结构[N].高等学校化学学报,2010,31(5):1051-1055.
[10]张丽娟,虞鑫海.含氟聚酰亚胺的研究进展[J].绝缘材料.2009,42(3):14-19.
[11]鲁云华,李伟.6FAPE基含氟聚酰亚胺的结构与性能研究[N].材料导报,2010,24(5):37-43.
[12]张丽娟,虞鑫海.1,3-双(4-氨基-2-三氟甲基苯氧基)苯及其无色透明聚酰亚胺薄膜的制备与性能研究[J].绝缘材料,2010,43(1):4-13.
[13]FLi,SFang,DiamineArchitecturalEffectsonGlassTransitions,RelaxationProcessesandOtherMaterialPropertiesinOrgano-SolubleAromaticPolyimideFilms[J].Polymer,1999,40(16):4571-4583.
高分子材料的耐热性范文篇9
【关键词】Zr-3;R60702;工业纯锆;性能研究;核工业应用
锆(Zirconium)位于元素周期表第IV-B族,室温下晶界结构呈密排六方晶格结构,在865℃时发生相变,由α-Zr转变为体心立方结构的β-Zr。由于金属锆具有高熔点(1852℃),耐氧化,优异的耐腐蚀性,良好的导热性能(热导率22Wm-1K-1),热中子吸收截面小(对2200m/s的中子,俘获截面0.185×10-28m2)以及良好的加工性能和力学性能,纯锆及其合金常被制成管材、板材、棒材、锻件等用于海洋、化工和核工业领域。关于锆及其合金如Zr-1(R60700)、Zr-2(R60802)、Zr-3(R60702)、Zr-4(R60804)、Zr-5(R60705)、M5(Zr-1.0Nb-0.16O)等,在微观组织、退火行为、耐氧化、耐腐蚀性以及应用等方面国内外已进行了大量报道,对于Zr-3在化工领域压力容器或换热器的应用,业已进行了深入讨论。本文主要综述工业纯锆Zr-3(ASTM中R60702)的成分及制备,力学性能及影响因素,焊接工艺及耐腐蚀性,及其在工业领域的应用。
1工业纯锆Zr-3的制备及成分
目前,常用的锆合金熔炼方法有三种:真空非自耗电弧炉熔炼、水冷铜坩埚感应熔炼和真空自耗感应熔炼。真空自耗电弧炉熔炼法是工业上生产金属锆的主要方法,通过加入不同含量的不同元素(Fe、Cr、Sn、Nb等),可以得到适应不同实际需求的锆合金。中国国标和美国标准中Zr-3(R60702)的化学成分含量列于表1。
表1Zr-3的化学成分[1-4]
从表1可以看出,Zr-3(R60702)的化学成分中含有铪元素,其含量不大于(4.5±0.10)%。金属铪是有效的长寿命中子吸收材料,具有热中子吸收截面较大(1.15×10-26m2),良好的力学性能和耐腐蚀性能,熔点高等特点。除了对于热中子吸收性能的差别,铪的耐腐蚀性甚至还要优于锆,因此,Zr-3中铪元素的存在对于其在腐蚀介质环境下的应用并无影响。
2Zr-3的力学性能研究
中国国标和美国标准中退火态Zr-3的管材、板材、棒材、锻件的力学性能列于表2。
表2Zr-3的力学性能
通过控制加工变形量和退火温度,Zr-3可以获得不同的组织性能。随着变形量的增加,位错密度和孪晶数量增加,组织更加精细,抗拉强度增强,但延伸率降低。试验证明,当变形量达到90%时,Zr-3材料的抗拉强度和屈服强度可分别提高到723MPa和637MPa,但延伸率降低到了10.8%;在变形量40%时,Zr-3的应变软化和硬化临界应变速率为1×10-2s-1。在500~700℃退火,Zr-3可以获得较好的强度和延伸率[5-7]。
3Zr-3的耐蚀性及焊接性研究
锆是钝化金属,其标准电极电位为-1.539V。锆与氧有很强的亲和力,在室温就可以和空气中氧气发生反应生成致密的氧化膜,从而保护基体金属。研究表明,Zr-3在500~700℃氧化后表面的氧化物主要为ZrO2,表面硬度增加[8]。纯锆对于干氯气、过氧化氢、苛性碱、发烟硫酸、盐酸、醋酸等具有优异的耐腐蚀性,但在氢氟酸、浓磷酸、浓硫酸、溴水、王水、氢溴酸中容易发生腐蚀,并在含Fe3+、Cu2+的盐酸中可能会发生点蚀与应力腐蚀[9]。
锆的焊接性和铬镍不锈钢近似,热膨胀系数(5.5×10-6/℃)是工程用金属材料中最低的,焊接变形小。弹性模量(海绵锆8.96×104MPa)较小,焊接残余应力小。但在焊接过程中应严防氮、氧、碳、氢等间隙元素的污染,避免产生气孔和间隙腐蚀。锆材的焊接方法很多,包括熔焊、钎焊、固态焊等,最常用的焊接方法之一是TIG焊。研究表明,Zr-3(R60702)的TIG焊接接头中热影响区的耐腐蚀性最差,在5mol/L的醋酸溶液中,热影响区的点蚀情况较为严重,焊缝区的耐蚀性较差,母材的耐蚀性不受影响[10-11]。
4Zr-3材料的应用
在石油、化工、冶金、医药等工业领域中苛刻的腐蚀条件下,不锈钢和镍基合金都无法满足使用要求时,锆材是优异的材料选择。
醋酸工业中,国内外厂家广泛采用锆反应器、换热器、管道等,合肥某家机械研究院研制的采用Zr-3板制作的醋酸生产中的冷却器,为锆设备国产化提供了宝贵的经验。硫酸工业中,锆制壳式和管式换热器代替传统的石墨换热器。锆材设备对于工业中高浓度硝酸也比不锈钢和钛材具有优势,国外一家化工厂处理99%浓度的硝酸时,采用了锆制U型管冷却器。在氯化洗涤器,锆材代替传统的塑料部件,使其使用寿命可提高到25年。在最早使用锆制设备的尿素工业中,锆材主要用于热交换器、冷凝器、反应器、管道系统、泵阀及密封件。由于锆的无毒且耐盐酸腐蚀,锆材还广泛应用与食品和医药生产中[12-13]。
相比不锈钢,锆材的价格要昂贵许多。对于在苛刻的腐蚀环境下使用,虽然设备投资较大,但从设备寿命、工人劳动强度、安全环保等方面综合考虑,成本是降低的。
5结语
目前,锆材在核工业中的应用较为广泛,核燃料及附属材料中采用锆的氟化物作为液体燃料的熔盐;采用Zr-2(R60802)和Zr-4(R60804)合金制作燃料元件的包套管;采用M5(Zr-1.0Nb-0.16O)合金制造的包壳材料用于AFA3G燃料组件中等。工业纯锆Zr-3在一般工业领域已有成熟的应用,且对其性能、焊接和耐蚀性的研究已经相当深入,结合核电厂设备的寿命相对较长及较难更换的特点,对于Zr-3材料应用于核工业设备的研究有待完善。
【参考文献】
[1]GB/T26314-2010,锆及锆合金牌号和化学成分[Z].
[2]ASTMB493,StandardSpecificationforZirconiumandZirconiumAlloyForgings[Z].
[3]ASTMB550/B550M,StandardSpecificationforZirconiumandZirconiumAlloyBarandWire[Z].
[4]ASTMB551/B551M,StandardSpecificationforZirconiumandZirconiumAlloyStrip,Sheet,andPlate[Z].
[5]肖洋洋.不同变形方式对Zr702组织及力学性能的影响研究[D].燕山大学,2012:11-47.
[6]MaMin,LiMing-he,TanYuan-biao,etc.Microstructureandtextureevolutionincommercial-purityZr702duringcoldrollingandannealing[J].InternationalJournalofMinerals,MetallurgyandMaterials,2014,21(8):785-795.
[7]HuRou-mei,LingXiang。Three-dimensionalNumericalSimulationonPlasticDamageinSmallPunchSpecimenofZirconium[J].InternationalJournalofPressureVesselsandPiping,2009,86:813-817.
[8]田晓东,王利捷,郝建民,唐美静.Zr-3在500~700℃的氧化及磨损行为[J].热加工工艺,2013,42(12):79-83.
[9]余存烨,余毅骏.“外星”金属钛、锆、钽[J].稀有金属快报,2004,23(10):31-34.
[10]凌遥王正东.TIG焊对工业纯锆R60702接头腐蚀性能的影响[J].核动力工程,2013,34(3):37-41.
[11]左小涛,王国平,雍文佳,张建.锆R60702焊接接头在有机酸中的腐蚀性研究[J].金属功能材料,2011,18(4):47-50.
高分子材料的耐热性范文
【关键词】淀粉;聚丙烯;发泡材料;制备;性能
一、淀粉
1.淀粉的性质及特点
淀粉是由多个葡萄糖分子聚合而成的物质。燃点约为380℃。淀粉不溶于水,在和水加热至60℃左右时(淀粉种类不同,糊化温度不一样),则糊化成胶体溶液。淀粉可以分为直链淀粉和支链淀粉两类。直链淀粉可溶,而支链淀粉部分溶解。支链淀粉溶解产生糊精。糊精在食品行业中可以作为添加剂,在造纸行业也用到糊精,糊精还可以做胶水、浆糊等等。
2.淀粉的改性
天然的淀粉性质不稳定,从而人们对淀粉进行改性,制备出改性淀粉使其能够更好的被人类生活所利用。淀粉的改性方法有很多,主要可以概括为:物理变性,化学变性,生物改性和复合变性四类。
(1)物理变性:就是通过对淀粉预糊化、微波,辐射处理淀粉、机械研磨处理淀粉、湿热处理淀粉等物理的方法对其改性。
(2)化学变性:就是在淀粉中加入不同的化学试剂使其酸解、氧化、交联、酯化、醚化和接枝等得到变性淀粉。
(3)生物改性:用各种酶来处理淀粉。
(4)复合变性:用上面任选两种或两种以上的方法对淀粉进行处理而得到的变性淀粉。例如将淀粉预糊化后再接枝,或先将淀粉氧化后再交联而得到的氧化交联淀粉等。
3.淀粉在塑料中的应用
(1)填充型淀粉塑料:是在塑料中加入不超过30%的淀粉,再加入相应的添加剂,通过加工而得到的淀粉基塑料。
(2)共混型淀粉塑料:是将淀粉与一些高分子材料共混,在混合中淀粉含量不低于30%。淀粉可以与纤维,秸秆等天然高分子混合,或者与PP、PE、聚乙烯醇等合成高分子混合。
二、聚丙烯
聚丙烯(PP)是一种白色粒状、无毒、无味的热塑性树脂。其用途相当广泛,五大通用塑料之一的聚丙烯具有加工性能好、来源丰富、价格便宜、电绝缘性好等优点。在汽车、家电、包装、电子、家具和一些高档工具上,需求量非常大。
1.聚丙烯的结构
聚丙烯的结构是由配位聚合得到的头一尾相接的线型结构:
如图1所示。全同立构与间同立构的聚合物称为立体规整聚合物,配位聚合体系主要得到全同立构的聚丙烯。TiCl4催化体系获得等规聚合体约占总的聚合的90-95%,实际的聚丙烯大分子链中虽然主要是全同立构的分子链段,但也包含一定量的间同立构和无规立构分子链段。所以部分大分子链呈现不规整性。这种聚丙烯具有“全同立构的立体嵌段”结构。
(1)物理性能。聚丙烯有较好的耐热性,长期使用温度可超100℃。聚丙烯的强度和刚度也好过聚乙烯,坚韧耐磨、耐震,机械性能好。聚丙烯是非极性高聚物,有优良的电性能和良好的耐热性,所以在电器工业上广泛使用。聚丙烯的另一优点是质轻(密度0.9g/cm3),制品能浮在水面上,这就使它的应用范围更广。
(2)耐化学介质性能。聚丙烯的耐酸碱性能良好,无论常温或较高温度(70℃,100℃)条件下,其耐碱及各种盐类的性能尤为突出。在室温下它几乎耐所有的无机酸和有机酸。70℃时耐10%盐酸、40%硝酸及30%硫酸的性能良好,但其易遭受氧化性的无机酸如浓硝酸、发烟硫酸等的侵蚀。
(3)大气老化性能。聚丙烯在光、热和空气中的氧(或臭氧)作用下易老化,尤其是大分子链中叔碳原子处易被氧化降解,光和热的作用在于引发氧化降解反应。聚丙烯可制成薄片,吹塑成型,也可以用压铸或挤压等方法成型。聚丙烯的机械加工性能很好,可以锯、切削,在床车上加工,也可用普通木材与金属的加工工具进行加工、还可焊接(220℃)。
2.聚丙烯的改性
(1)聚丙烯的化学改性。通过对聚丙烯进行接枝共聚、氯化、嵌段、交联、氯磺化等化学手段对其改性从而获得性能良好共聚物的方法。
(2)聚丙烯的物理改性。通过物理的方法将聚丙烯、有机(无机)材料或一些添加剂进行混合、混炼来改变聚丙烯的高层次结构。物理改性大致分:共混改性、填充改性、增强改性、功能改性等。共混改性:指将两种或两种聚合物材料、无机材料和添加助剂,在一定温度下进行机械混合。填充改性和增强改性:指在高分子材料中加入一定量的填充剂来改善聚合物材料的性能和弥补材料的不足。常用的填充剂有:滑石粉、碳酸钙、云母、高岭土、导电材料等。功能改性:PP属于易燃材料,在工业生产中,加入阻燃剂,可以对其进行阻燃改性。还有对PP进行防静电处理,将抗静电剂喷洒、浸渍、涂覆抗静电材料或将抗静电剂掺和到材料中,成为抗静电性能的材料。
3.聚丙烯发泡材料及其应用
聚丙烯发泡材料具有良好的耐热性(最高达130℃的使用温度)可在微波中使用。同时还具有较好的力学性能、可降解性、无毒环保等优点,被广泛应用在包装、汽车和隔热材料等方面。聚丙烯发泡材料的这些优点使其成为PS泡沫材料的良好替代品。
(1)包装材料。发泡塑料质量轻应用在塑料包装上较好。由于它耐热性好,高达130℃,因而可以将其制成容器,放在微波炉中使用。例如:耐高温的碗、盘子、保鲜膜等等。由于发泡PP片材无毒,在加入一些物质后可部分分解,用它制作的一次性餐具是比较理想的环保餐具。例如:果盘、托盘、熟食品还有在电器的包装上等。
(2)隔热材料。聚丙烯发泡材料的绝热性好,热导率低,可耐120℃高温,可作为热水管、贮槽的热绝缘材料和一些管道的保温材料等。
(3)建筑材料。发泡PP可作为屋顶、墙壁的填料。可用它制作成建筑模板。通过加入一些纤维合成木材,制作成木地板。
【参考文献】
高分子材料的耐热性范文篇11
关键词:复合材料;机械制造;应用;行业
对于复合材料而言,它主要是由两种或者两种以上性质不尽相同的材料经过各种施工工艺组合而成的新型材料,复合材料的每一组成材料在性能方面都发挥了很强的协同作用。复合材料具有强度好、刚度大、质量小等优势,能够根据不用的使用条件进行设计和制造,以满足各种不同的用途,从而大幅度提升工程结构材料及其功能材料的整体性能。通常情况下,复合材料拥有良好的比模量和比强度,并且化学稳定性好,耐磨、减磨、自滑性好,耐热性好,高抗热冲击性和高韧度,导热性和导电性能良好。所以,当前复合材料已经广泛应用于航空航天、机械制造、电子、纺织、医学、汽车工业等诸多领域当中,产业化形势初具形成。笔者通过本文,针对复合材料在机械制造上的应用进行阐述。
1.关于复合材料的基本概述
由于复合材料各组成材料在性能方面实现了协调,能够实现单组材料所不具有的优势,例如,复合材料具有强度高、刚度大、质量小等优点。
可将复合材料分为功能型材料与结构型材料,前者具有良好的耐磨、耐高温性,适用于机械零部件制造,在保证工件质量的同时,也可适当的增加其使用寿命;而后者则可以很好应用于机械设备制造中,它具有质量小、强度大等优势,有效降低了机械设备的重量。
2.在机械制造上应用复合材料
在制造机械的过程中,应该按照零部件工作环境的不同来确定原材料的选择、工作环境、受力分析和一些特殊的条件等等。一方面要保证零部件在工作过程中不能出现失效的情况,另一方面还要尽量的增加其实际使用寿命。下面将对部分复合材料的主要性能、特点及用途进行集中阐述。
2.1不锈钢复合钢板
不锈钢板是由合金元素组成,这些元素也决定了不锈钢板性能的差异;由于这些元素的存在,因此造就了不锈钢板具有极佳的耐化学腐蚀和电化学腐蚀性能,是在钢材里面是最好的。不锈钢复合板采用先进的真空轧制工艺,可以确保让不同材质材料之间形成原子结合,结合率可达100%。不锈钢复合板具有良好的导热能力,又具有防腐蚀功能,可大量用于焦化设备。如使用于蒸氨塔,可以提高蒸氨塔的使用寿命,降低运行成本;另外一方面因其防腐性能,又能应用于蒸氨设备。
2.2玻璃纤维复合材料
这种复合材料是热固性树脂和纤维的复合,其密度小、强度大、抗冲击性强。收缩性小、耐腐蚀。同时。热塑性树脂和纤维的复合,还具有良好的注射成形和低温韧性。
玻璃纤维复合材料通常运用到耐腐蚀、耐磨、绝缘、无磁、减磨和普通机械零部件、泵阀、管道和容器当中。
2.3碳纤维石墨纤维复合材料
这种复合材料主要是由碳-陶瓷复合、碳-树脂复合等,它具有良好的比模量、比强度、比刚度,而且线膨胀系数小、耐摩擦、自性和耐磨损性良好。此外,它还具有很好的耐热性和耐腐蚀性。
碳纤维石墨纤维复合材料在航空、宇航、原子能等工业中主要使用在压气机叶片、发动机壳体、轴瓦、齿轮、机翼上。
2.4硼纤维复合材料
这种复合材料主要是硼和环氧树脂或者铝复合而成,具有良好的比刚度和比强度。
硼纤维复合材料主要应用于火箭、飞机等构件当中,能够有效降低的机械设备的质量。
2.5晶须复合材料
晶须复合材料中的晶须为单晶,没有普通材料的空穴和错位等毛病,而且具有很强的机械强度。
通产情况下,晶须复合材料应用于涡轮叶片当中。
2.6石棉纤维复合材料
石棉纤维复合材料主要是纤维和树脂的复合,具有良好的绝缘性、耐磨性、耐热性和耐酸性。
石棉纤维复合材料主要应用在绝缘材料、制动机械部件和密封件当中。
2.7金属粒塑料复合材料
金属粒塑料复合材料主要是将金属掺入到塑料当中,能够有效改善自身原本具有的导电性和导热性,并降低线膨胀系数。
石棉纤维复合材料主要应用于铅粉加入氟塑料所做的轴承材料当中。
2.8陶瓷粒金属复合材料
陶瓷粒金属复合材料能够有效提升机械设备的高温耐磨性、抗腐蚀性以及等性能。
陶瓷粒金属复合材料中氧化物金属陶瓷主要用于高速切削材料和高温材料当中;而碳化铬则主要应用于耐磨喷、耐腐蚀、高温无、重载轴承的零部件当中。
2.9弥散强化复合材料
弥散强化复合材料主要是将尺寸比较小的硬质粒子均匀的分布于金属基体当中,从而极大地提升了机械设备的耐热性和强度值。
弥散强化复合材料一般应用于比强度较高、耐热性良好的工件当中。
2.10多层复合材料
多层复合材料主要是指钢-多孔性青铜-塑料三层的复合,具有良好的耐磨性和抗冲击性。
多层复合材料通常应用于热片、轴承以及球头座等耐磨件当中。
2.11多孔浸渍复合材料
多孔浸渍复合材料主要是指多孔材料浸渍到低摩擦系数的油脂或者氟塑料当中,能够有效降低摩擦力。
多孔浸渍复合材料一般应用于轴承、油枕当中,而浸树脂石墨则往往用于抗磨材料当中。
3.在冲压模具的制造上应用复合材料
因为各种各样的冲压模具所处的工作环境有所差异,因而,针对模具材料的要求也不尽相同。我们可以将这些模具材料大体上划分成三种:首先是冲裁模材料的要求;其次是拉伸模材料的要求;第三是冷挤压模材料的要求。对于这些模具制造来说,它们要求原材料能够承受振动、冲击、拉伸、高压、摩擦、扭曲等负荷,甚至还要在超高温条件下完成工作。从当前形势来看,制造冲压模具的材料大部分是以钢材为主,由于碳素工具钢在价格方面相对便宜,并且容易加工塑性,因而它被广泛应用于模具制造当中,然而其红硬性和淬透性较差,在进行热处理时将会发生较大的形变,并且承载能力低,不适用于塑性低、硬度大的零部件制造。例如,硬质合金钢的抗弯强度、韧性差,对于一些需要较强硬度和韧性的机械设备制造就无法满足要求,而复合材料在性能方面则具有较强的比强度和比模量,它能够有效抵抗刃口在工作过程中所受到的各种强烈冲击和摩擦。
4.结语
总而言之,复合材料科学是一种包含了诸多行业、领域的新兴学科,由于其具有质量小、强度大、加工便捷、弹性良好、抗化学腐蚀、耐候性好等优势,现已经广泛应用于航空航天、电子、汽车、医学、化工等诸多领域当中。近年来,针对新型复合材料的设计及其性能的研究与评价获得巨大进步,复合材料在材料工业当中所占比例也逐渐增加,因而产业化趋势得到显著加强。伴随科学技术的深入发展,复合材料也势必会在更多的领域和行业中发挥越来越大的作用。
参考文献:
[1]关锦清,文潮,刘晓新,唐仕英,林英睿,李迅,周刚.不锈钢复合板与16MnR钢冲击拉伸力学特性研究[J].兵器材料科学与工程,2010(01).
[2]王正中,蒋玉滨,孙小伟.东风微型轿车复合材料车身的开发与应用[J].玻璃钢学会第十五届全国玻璃钢/复合材料学术年会论文集,2008(22):275一278.
[3]李文军,殷江宁,邢高磊,岳强,崔广梅.321/15CrMoR金属复合板压力容器封头的制造[J],材料开发与应用,2011(05).
[4]王宏雁,陈君毅.汽车车身轻量化结构与轻质材料[M].北京:北京大学出版社,2009:50-153.
高分子材料的耐热性范文1篇12
关键词:梯度功能材料,复合材料,研究进展
TheAdvanceofFunctionallyGradientMaterials
JinliangCui
(Qinghaiuniversity,XiningQinghai810016,china)
Abstract:Thispaperintroducestheconcept,types,capability,preparationmethodsoffunctionallygradedmaterials.Baseduponanalysisofthepresentapplicationsituationsandprospectofthiskindofmaterialssomeproblemsexistedarepresented.ThecurrentstatusoftheresearchofFGMarediscussedandananticipationofitsfuturedevelopmentisalsopresent.
Keywords:FGM;composite;theAdvance
0引言
信息、能源、材料是现代科学技术和社会发展的三大支柱。现代高科技的竞争在很大程度上依赖于材料科学的发展。对材料,特别是对高性能材料的认识水平、掌握和应用能力,直接体现国家的科学技术水平和经济实力,也是一个国家综合国力和社会文明进步速度的标志。因此,新材料的开发与研究是材料科学发展的先导,是21世纪高科技领域的基石。
近年来,材料科学获得了突飞猛进的发展[1]。究其原因,一方面是各个学科的交叉渗透引入了新理论、新方法及新的实验技术;另一方面是实际应用的迫切需要对材料提出了新的要求。而FGM即是为解决实际生产应用问题而产生的一种新型复合材料,这种材料对新一代航天飞行器突破“小型化”,“轻质化”,“高性能化”和“多功能化”具有举足轻重的作用[2],并且它也可广泛用于其它领域,所以它是近年来在材料科学中涌现出的研究热点之一。
1FGM概念的提出
当代航天飞机等高新技术的发展,对材料性能的要求越来越苛刻。例如:当航天飞机往返大气层,飞行速度超过25个马赫数,其表面温度高达2000℃。而其燃烧室内燃烧气体温度可超过2000℃,燃烧室的热流量大于5MW/m2,其空气入口的前端热通量达5MW/m2.对于如此大的热量必须采取冷却措施,一般将用作燃料的液氢作为强制冷却的冷却剂,此时燃烧室内外要承受高达1000K以上的温差,传统的单相均匀材料已无能为力[1]。若采用多相复合材料,如金属基陶瓷涂层材料,由于各相的热胀系数和热应力的差别较大,很容易在相界处出现涂层剥落[3]或龟裂[1]现象,其关键在于基底和涂层间存在有一个物理性能突变的界面。为解决此类极端条件下常规耐热材料的不足,日本学者新野正之、平井敏雄和渡边龙三人于1987年首次提出了梯度功能材料的概念[1],即以连续变化的组分梯度来代替突变界面,消除物理性能的突变,使热应力降至最小[3],如图1所示。
随着研究的不断深入,梯度功能材料的概念也得到了发展。目前梯度功能材料(FGM)是指以计算机辅助材料设计为基础,采用先进复合技术,使构成材料的要素(组成、结构)沿厚度方向有一侧向另一侧成连续变化,从而使材料的性质和功能呈梯度变化的新型材料[4]。
2FGM的特性和分类
2.1FGM的特殊性能
由于FGM的材料组分是在一定的空间方向上连续变化的特点如图2,因此它能有效地克服传统复合材料的不足[5]。正如Erdogan在其论文[6]中指出的与传统复合材料相比FGM有如下优势:
1)将FGM用作界面层来连接不相容的两种材料,可以大大地提高粘结强度;
2)将FGM用作涂层和界面层可以减小残余应力和热应力;
3)将FGM用作涂层和界面层可以消除连接材料中界面交叉点以及应力自由端点的应力奇异性;
4)用FGM代替传统的均匀材料涂层,既可以增强连接强度也可以减小裂纹驱动力。
图2
2.2FGM的分类
根据不同的分类标准FGM有多种分类方式。根据材料的组合方式,FGM分为金属/陶瓷,陶瓷/陶瓷,陶瓷/塑料等多种组合方式的材料[1];根据其组成变化FGM分为梯度功能整体型(组成从一侧到另一侧呈梯度渐变的结构材料),梯度功能涂敷型(在基体材料上形成组成渐变的涂层),梯度功能连接型(连接两个基体间的界面层呈梯度变化)[1];根据不同的梯度性质变化分为密度FGM,成分FGM,光学FGM,精细FGM等[4];根据不同的应用领域有可分为耐热FGM,生物、化学工程FGM,电子工程FGM等[7]。
3FGM的应用
FGM最初是从航天领域发展起来的。随着FGM研究的不断深入,人们发现利用组分、结构、性能梯度的变化,可制备出具有声、光、电、磁等特性的FGM,并可望应用于许多领域。FGM的应用[8]见图3。
图3FGM的应用
功能
应用领域材料组合
缓和热应
力功能及
结合功能
航天飞机的超耐热材料
陶瓷引擎
耐磨耗损性机械部件
耐热性机械部件
耐蚀性机械部件
加工工具
运动用具:建材陶瓷金属
陶瓷金属
塑料金属
异种金属
异种陶瓷
金刚石金属
碳纤维金属塑料
核功能
原子炉构造材料
核融合炉内壁材料
放射性遮避材料轻元素高强度材料
耐热材料遮避材料
耐热材料遮避材料
生物相溶性
及医学功能
人工牙齿牙根
人工骨
人工关节
人工内脏器官:人工血管
补助感觉器官
生命科学磷灰石氧化铝
磷灰石金属
磷灰石塑料
异种塑料
硅芯片塑料
电磁功能
电磁功能陶瓷过滤器
超声波振动子
IC
磁盘
磁头
电磁铁
长寿命加热器
超导材料
电磁屏避材料
高密度封装基板压电陶瓷塑料
压电陶瓷塑料
硅化合物半导体
多层磁性薄膜
金属铁磁体
金属铁磁体
金属陶瓷
金属超导陶瓷
塑料导电性材料
陶瓷陶瓷
光学功能防反射膜
光纤;透镜;波选择器
多色发光元件
玻璃激光透明材料玻璃
折射率不同的材料
不同的化合物半导体
稀土类元素玻璃
能源转化功能
MHD发电
电极;池内壁
热电变换发电
燃料电池
地热发电
太阳电池陶瓷高熔点金属
金属陶瓷
金属硅化物
陶瓷固体电解质
金属陶瓷
电池硅、锗及其化合物
4FGM的研究
FGM研究内容包括材料设计、材料制备和材料性能评价。FGM的研究开发体系如图4所示[8]。
设计设计
图4FGM研究开发体系
4.1FGM设计
FGM设计是一个逆向设计过程[7]。
首先确定材料的最终结构和应用条件,然后从FGM设计数据库中选择满足使用条件的材料组合、过渡组份的性能及微观结构,以及制备和评价方法,最后基于上述结构和材料组合选择,根据假定的组成成份分布函数,计算出体系的温度分布和热应力分布。如果调整假定的组成成份分布函数,就有可能计算出FGM体系中最佳的温度分布和热应力分布,此时的组成分布函数即最佳设计参数。
FGM设计主要构成要素有三:
1)确定结构形状,热—力学边界条件和成分分布函数;
2)确定各种物性数据和复合材料热物性参数模型;
3)采用适当的数学—力学计算方法,包括有限元方法计算FGM的应力分布,采用通用的和自行开发的软件进行计算机辅助设计。
FGM设计的特点是与材料的制备工艺紧密结合,借助于计算机辅助设计系统,得出最优的设计方案。
4.2FGM的制备
FGM制备研究的主要目标是通过合适的手段,实现FGM组成成份、微观结构能够按设计分布,从而实现FGM的设计性能。可分为粉末致密法:如粉末冶金法(PM),自蔓延高温合成法(SHS);涂层法:如等离子喷涂法,激光熔覆法,电沉积法,气相沉积包含物理气相沉积(PVD)和化学相沉积(CVD);形变与马氏体相变[10、14]。
4.2.1粉末冶金法(PM)
PM法是先将原料粉末按设计的梯度成分成形,然后烧结。通过控制和调节原料粉末的粒度分布和烧结收缩的均匀性,可获得热应力缓和的FGM。粉末冶金法可靠性高,适用于制造形状比较简单的FGM部件,但工艺比较复杂,制备的FGM有一定的孔隙率,尺寸受模具限制[7]。常用的烧结法有常压烧结、热压烧结、热等静压烧结及反应烧结等。这种工艺比较适合制备大体积的材料。PM法具有设备简单、易于操作和成本低等优点,但要对保温温度、保温时间和冷却速度进行严格控制。国内外利用粉末冶金方法已制备出的FGM有:MgC/Ni、ZrO2/W、Al2O3/ZrO2[8]、Al2O3-W-Ni-Cr、WC-Co、WC-Ni等[7]。
4.2.2自蔓延燃烧高温合成法(Self-propagatingHigh-temperatureSynthesis简称SHS或CombustionSynthesis)
SHS法是前苏联科学家Merzhanov等在1967年研究Ti和B的燃烧反应时,发现的一种合成材料的新技术。其原理是利用外部能量加热局部粉体引燃化学反应,此后化学反应在自身放热的支持下,自动持续地蔓延下去,利用反应热将粉末烧结成材,最后合成新的化合物。其反应示意图如图6所示[16]:
图6SHS反应过程示意图
SHS法具有产物纯度高、效率高、成本低、工艺相对简单的特点。并且适合制造大尺寸和形状复杂的FGM。但SHS法仅适合存在高放热反应的材料体系,金属与陶瓷的发热量差异大,烧结程度不同,较难控制,因而影响材料的致密度,孔隙率较大,机械强度较低。目前利用SHS法己制备出Al/TiB2,Cu/TiB2、Ni/TiC[8]、Nb-N、Ti-Al等系功能梯度材料[7、11]。
4.2.3喷涂法
喷涂法主要是指等离子体喷涂工艺,适用于形状复杂的材料和部件的制备。通常,将金属和陶瓷的原料粉末分别通过不同的管道输送到等离子喷枪内,并在熔化的状态下将它喷镀在基体的表面上形成梯度功能材料涂层。可以通过计算机程序控制粉料的输送速度和流量来得到设计所要求的梯度分布函数。这种工艺已经被广泛地用来制备耐热合金发动机叶片的热障涂层上,其成分是部分稳定氧化锆(PSZ)陶瓷和NiCrAlY合金[9]。
4.2.3.1等离子喷涂法(PS)
PS法的原理是等离子气体被电子加热离解成电子和离子的平衡混合物,形成等离子体,其温度高达1500K,同时处于高度压缩状态,所具有的能量极大。等离子体通过喷嘴时急剧膨胀形成亚音速或超音速的等离子流,速度可高达1.5km/s。原料粉末送至等离子射流中,粉末颗粒被加热熔化,有时还会与等离子体发生复杂的冶金化学反应,随后被雾化成细小的熔滴,喷射在基底上,快速冷却固结,形成沉积层。喷涂过程中改变陶瓷与金属的送粉比例,调节等离子射流的温度及流速,即可调整成分与组织,获得梯度涂层[8、11]。该法的优点是可以方便的控制粉末成分的组成,沉积效率高,无需烧结,不受基体面积大小的限制,比较容易得到大面积的块材[10],但梯度涂层与基体间的结合强度不高,并存在涂层组织不均匀,空洞疏松,表面粗糙等缺陷。采用此法己制备出TiB2-Ni、TiC-Ni、TiB2-Cu、Ti-Al[7]、NiCrAl/MgO-ZrO2、NiCrAl/Al2O3/ZrO2、NiCrAlY/ZrO2[10]系功能梯度材料
图7PS方法制备FGM涂层示意图[17](a)单枪喷涂(b)双枪喷涂
4.2.3.2激光熔覆法
激光熔覆法是将预先设计好组分配比的混合粉末A放置在基底B上,然后以高功率的激光入射至A并使之熔化,便会产生用B合金化的A薄涂层,并焊接到B基底表面上,形成第一包覆层。改变注入粉末的组成配比,在上述覆层熔覆的同时注入,在垂直覆层方向上形成组分的变化。重复以上过程,就可以获得任意多层的FGM。用Ti-A1合金熔覆Ti用颗粒陶瓷增强剂熔覆金属获得了梯度多层结构。梯度的变化可以通过控制初始涂层A的数量和厚度,以及熔区的深度来获得,熔区的深度本身由激光的功率和移动速度来控制。该工艺可以显著改善基体材料表面的耐磨、耐蚀、耐热及电气特性和生物活性等性能,但由于激光温度过高,涂层表面有时会出现裂纹或孔洞,并且陶瓷颗粒与金属往往发生化学反应[10]。采用此法可制备Ti-Al、WC-Ni、Al-SiC系梯度功能材料[7]。
图8同步注粉式激光表面熔覆处理示意图[18]
4.2.3.3热喷射沉积[10]
与等离子喷涂有些相关的一种工艺是热喷涂。用这种工艺把先前熔化的金属射流雾化,并喷涂到基底上凝固,因此,建立起一层快速凝固的材料。通过将增强粒子注射到金属流束中,这种工艺已被推广到制造复合材料中。陶瓷增强颗粒,典型的如SiC或Al2O3,一般保持固态,混入金属液滴而被涂覆在基底,形成近致密的复合材料。在喷涂沉积过程中,通过连续地改变增强颗粒的馈送速率,热喷涂沉积已被推广产生梯度6061铝合金/SiC复合材料。可以使用热等静压工序以消除梯度复合材料中的孔隙。
4.2.3.4电沉积法
电沉积法是一种低温下制备FGM的化学方法。该法利用电镀的原理,将所选材料的悬浮液置于两电极间的外场中,通过注入另一相的悬浮液使之混合,并通过控制镀液流速、电流密度或粒子浓度,在电场作用下电荷的悬浮颗粒在电极上沉积下来,最后得到FGM膜或材料[8]。所用的基体材料可以是金属、塑料、陶瓷或玻璃,涂层的主要材料为TiO2-Ni,Cu-Ni,SiC-Cu,Cu-Al2O3等。此法可以在固体基体材料的表面获得金属、合金或陶瓷的沉积层,以改变固体材料的表面特性,提高材料表面的耐磨损性、耐腐蚀性或使材料表面具有特殊的电磁功能、光学功能、热物理性能,该工艺由于对镀层材料的物理力学性能破坏小、设备简单、操作方便、成型压力和温度低,精度易控制,生产成本低廉等显著优点而备受材料研究者的关注。但该法只适合于制造薄箔型功能梯度材料。[8、10]
4.2.3.5气相沉积法
气相沉积是利用具有活性的气态物质在基体表面成膜的技术。通过控制弥散相浓度,在厚度方向上实现组分的梯度化,适合于制备薄膜型及平板型FGM[8]。该法可以制备大尺寸的功能梯度材料,但合成速度低,一般不能制备出大厚度的梯度膜,与基体结合强度低、设备比较复杂。采用此法己制备出Si-C、Ti-C、Cr-CrN、Si-C-TiC、Ti-TiN、Ti-TiC、Cr-CrN系功能梯度材料。气相沉积按机理的不同分为物理气相沉积(PVD)和化学气相沉积(CVD)两类。
化学气相沉积法(CVD)是将两相气相均质源输送到反应器中进行均匀混合,在热基板上发生化学反应并使反映产物沉积在基板上。通过控制反应气体的压力、组成及反应温度,精确地控制材料的组成、结构和形态,并能使其组成、结构和形态从一种组分到另一种组分连续变化,可得到按设计要求的FGM。另外,该法无须烧结即可制备出致密而性能优异的FGM,因而受到人们的重视。主要使用的材料是C-C、C-SiC、Ti-C等系[8、10]。CVD的制备过程包括:气相反应物的形成;气相反应物传输到沉积区域;固体产物从气相中沉积与衬底[12]。
物理气相沉积法(PVD)是通过加热固相源物质,使其蒸发为气相,然后沉积于基材上,形成约100μm厚度的致密薄膜。加热金属的方法有电阻加热、电子束轰击、离子溅射等。PVD法的特点是沉积温度低,对基体热影响小,但沉积速度慢。日本科技厅金属材料研究所用该法制备出Ti/TiN、Ti/TiC、Cr/CrN系的FGM[7~8、10~11]
4.2.4形变与马氏体相变[8]
通过伴随的应变变化,马氏体相变能在所选择的材料中提供一个附加的被称作“相变塑性”的变形机制。借助这种机制在恒温下形成的马氏体量随材料中的应力和变形量的增加而增加。因此,在合适的温度范围内,可以通过施加应变(或等价应力)梯度,在这种材料中产生应力诱发马氏体体积分数梯度。这一方法在顺磁奥氏体18-8不锈钢(Fe-18%,Cr-8%Ni)试样内部获得了铁磁马氏体α体积分数的连续变化。这种工艺虽然明显局限于一定的材料范围,但能提供一个简单的方法,可以一步生产含有饱和磁化强度连续变化的材料,这种材料对于位置测量装置的制造有潜在的应用前景。
4.3FGM的特性评价
功能梯度材料的特征评价是为了进一步优化成分设计,为成分设计数据库提供实验数据,目前已开发出局部热应力试验评价、热屏蔽性能评价和热性能测定、机械强度测定等四个方面。这些评价技术还停留在功能梯度材料物性值试验测定等基础性的工作上[7]。目前,对热压力缓和型的FGM主要就其隔热性能、热疲劳功能、耐热冲击特性、热压力缓和性能以及机械性能进行评价[8]。目前,日本、美国正致力于建立统一的标准特征评价体系[7~8]。
5FGM的研究发展方向
5.1存在的问题
作为一种新型功能材料,梯度功能材料范围广泛,性能特殊,用途各异。尚存在一些问题需要进一步的研究和解决,主要表现在以下一些方面[5、13]:
1)梯度材料设计的数据库(包括材料体系、物性参数、材料制备和性能评价等)还需要补充、收集、归纳、整理和完善;
2)尚需要进一步研究和探索统一的、准确的材料物理性质模型,揭示出梯度材料物理性能与成分分布,微观结构以及制备条件的定量关系,为准确、可靠地预测梯度材料物理性能奠定基础;
3)随着梯度材料除热应力缓和以外用途的日益增加,必须研究更多的物性模型和设计体系,为梯度材料在多方面研究和应用开辟道路;
4)尚需完善连续介质理论、量子(离散)理论、渗流理论及微观结构模型,并借助计算机模拟对材料性能进行理论预测,尤其需要研究材料的晶面(或界面)。
5)已制备的梯度功能材料样品的体积小、结构简单,还不具有较多的实用价值;
6)成本高。
5.2FGM制备技术总的研究趋势[13、15、19-20]
1)开发的低成本、自动化程度高、操作简便的制备技术;
2)开发大尺寸和复杂形状的FGM制备技术;
3)开发更精确控制梯度组成的制备技术(高性能材料复合技术);
4)深入研究各种先进的制备工艺机理,特别是其中的光、电、磁特性。
5.3对FGM的性能评价进行研究[2、13]
有必要从以下5个方面进行研究:
1)热稳定性,即在温度梯度下成分分布随时间变化关系问题;
2)热绝缘性能;
3)热疲劳、热冲击和抗震性;
4)抗极端环境变化能力;
5)其他性能评价,如热电性能、压电性能、光学性能和磁学性能等
6结束语
FGM的出现标志着现代材料的设计思想进入了高性能新型材料的开发阶段[8]。FGM的研究和开发应用已成为当前材料科学的前沿课题。目前正在向多学科交叉,多产业结合,国际化合作的方向发展。
参考文献:
[1]杨瑞成,丁旭,陈奎等.材料科学与材料世界[M].北京:化学工业出版社,2006.
[2]李永,宋健,张志民等.梯度功能力学[M].北京:清华大学出版社.2003.
[3]王豫,姚凯伦.功能梯度材料研究的现状与将来发展[J].物理,2000,29(4):206-211.
[4]曾黎明.功能复合材料及其应用[M].北京:化学工业出版社,2007.
[5]高晓霞,姜晓红,田东艳等。功能梯度材料研究的进展综述[J].山西建筑,2006,32(5):143-144.
[6]Erdogan,F.Fracturemechanicsoffunctionallygradedmaterials[J].Compos.Engng,1995(5):753-770.
[7]李智慧,何小凤,李运刚等.功能梯度材料的研究现状[J].河北理工学院学报,2007,29(1):45-50.
[8]李杨,雷发茂,姚敏,李庆文等.梯度功能材料的研究进展[J].菏泽学院学报,2007,29(5):51-55.
[9]林峰.梯度功能材料的研究与应用[J].广东技术师范学院学报,2006,6:1-4.
[10]庞建超,高福宝,曹晓明.功能梯度材料的发展与制备方法的研究[J].金属制品,2005,31(4):4-9.
[11]戈晓岚,赵茂程.工程材料[M].南京:东南大学出版社,2004.
[12]唐小真.材料化学导论[M].北京:高等教育出版社,2007.
[13]李进,田兴华.功能梯度材料的研究现状及应用[J].宁夏工程技术,2007,6(1):80-83.
[14]戴起勋,赵玉涛.材料科学研究方法[M].北京:国防工业出版社,2005.
[15]邵立勤.新材料领域未来发展方向[J].新材料产业,2004,1:25-30.
[16]自蔓延高温合成法.材料工艺及应用/jxzy/jlkj/data/clkxygcgl/clgy/clgy16.htm
[17]远立贤.金属/陶瓷功能梯度涂层工艺的应用现状./articleview/2006-6-6/article_view_405.htm.
[18]工程材料./zskj/3021/gccl/CH2/2.6.4.htm.
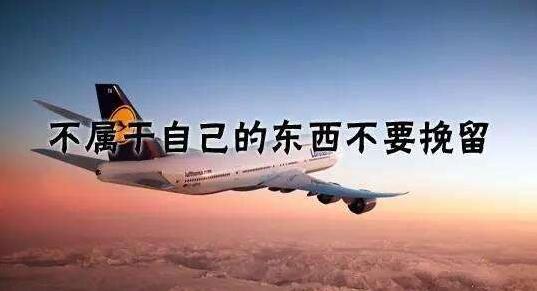
年级写人的作文范例(整理5篇)
- 阅0年级写人的作文篇1我最熟悉的人当然是我的弟弟啦,我的弟弟是个瓜子脸,乌黑的眉毛下有一双水汪汪的大眼睛。他还有一张会说的嘴,如果你和他斗嘴,他肯定斗得你无话可说。我弟弟特.....
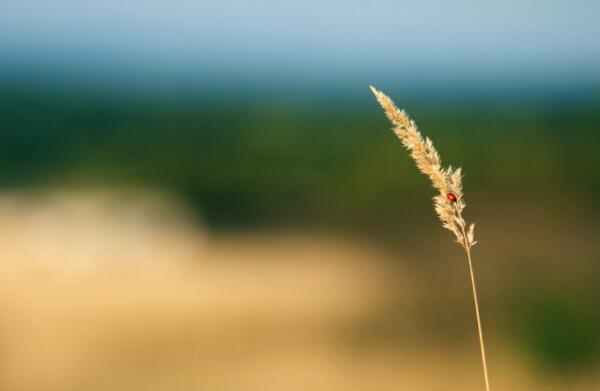
党员酒驾检讨书范例(精选3篇)
- 阅02020年党员酒驾检讨书范例篇1尊敬的交警同志:关于我酒后驾驶的行为,几天来,我认真反思,深刻自剖,为自己的行为感到了深深地愧疚和不安,在此,我谨向各位做出深刻检讨,并将我几天来的.....
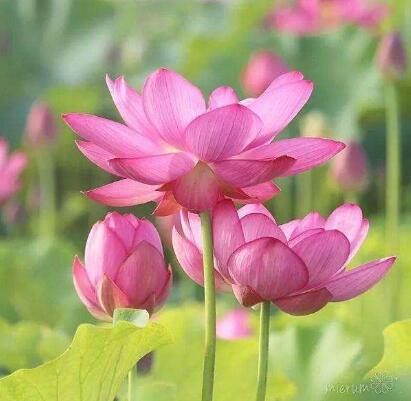
宝宝支气管炎如何护理范例(12篇)
- 阅0宝宝支气管炎如何护理范文篇1四种情况易造成气管异物哭闹时进食宝宝的臼齿未萌出,咀嚼能力差,而且喉的防御功能不健全,若在进食时哭闹很容易将食物呛进气管内。好动误吸宝宝天.....
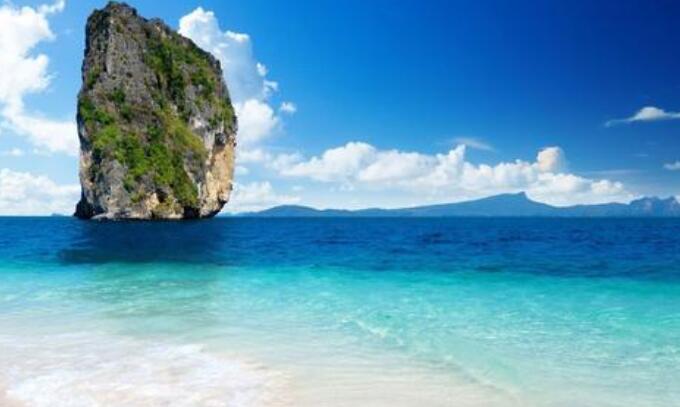
对劳动教育课的认识范例(3篇)
- 阅0对劳动教育课的认识范文关键词:劳动技术课重要性综合素质1.引言我国传统的教育模式只注重升学率,学生只追求学习成绩的提高,大多缺少吃苦耐劳的品质,为了适应社会主义现代化的.....
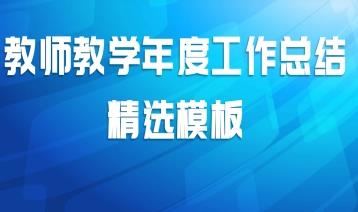
教师个人工作总结标准模板范文3篇
- 阅12023年教师个人工作总结 篇1 本学年,本人接手担任学校教学工作。一学期来,我自始至终以认真严谨的治学态度....
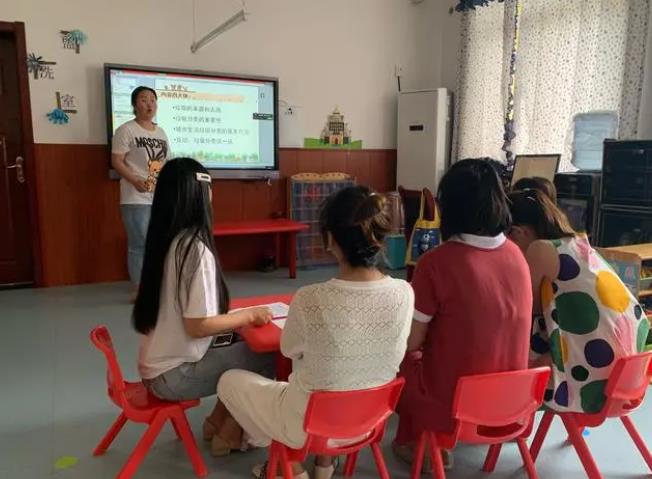
幼儿园教职工培训计划范文(精选5篇)
- 阅1幼儿园教职工培训计划篇1一、培训目标和培训重点坚持以师德建设为中心,以促进教师专业发展为目标,以《指南》....