超声波焊接(6篇)
来源:
超声波焊接篇1
【关键词】超声波探伤;缺陷识别
1.超声波探伤技术缺陷识别的意义
超声波探伤技术是当前应用最为广泛的无损探伤方式之一,其应用具有灵敏度高、穿透性超强、探测速度快、使用便携方便且对人体无损害等一系列优点。超声波探伤在建筑方面的应用中,对于钢材料的穿透能力具有十分大的优势,主要应用与探测厚度较大的钢板和焊缝。对于钢板平面上的缺陷,尽管有些缺陷深度大,但是只要超声波能直射到缺陷界面就能得到十分清晰的缺陷波。因此,超声波探伤技术在压力容器焊缝探伤和未焊透裂纹等危险性较高的缺陷检测中具有十分重要的应用意义。
2.超声波探伤缺陷的识别
2.1平面状缺陷的探测识别
对于平面状的缺陷类型,在不同方向上的探测,其缺陷回波的高度也具有明显的不同,在缺陷垂直方向进行探测时,其缺陷回波较高;而在平行面上进行缺陷探测时,其缺陷回波较低,有些情况甚至没有缺陷回波。所以针对裂纹类的缺陷类型来说,在超声波探伤识别中通常会出现较大的回波高度,且波幅宽,波峰较多。将探头进行平移,会出现反射波连续的现象,且波幅也随之变动;将探头转动会发现波峰有上下错动的现象出现,这些都可以作为检测平面状缺陷识别的依据。
2.2点状缺陷的探测识别
点状缺陷的探测识别在方向上,缺陷回波不会出现显著的变化,其波形稳定,不同方向探测的反射波高度也大致相同,但是在实际的检测中一旦移动探头,回波就可能消失。根据不同材质内含物阻抗的不同,超声波探伤检测的表现形式也有所不同。气孔内通常含有气体,其声阻抗较小,反射率较高,波形呈陡直尖锐状;而金属夹渣或者非金属夹渣类型的缺陷类型的声阻抗较大,反射波也会更低一些,夹渣面较粗糙的情况,其波形较宽,呈锯齿形状;气孔较为密集的反射波的波高会随着气孔的大小不一而表现出不同的高度,当探头进行定点转动检测时,波高就会呈现出此起彼落的现象。
2.3咬边缺陷的探测识别
咬边缺陷的超声波探测识别主要表现在反射波上,通常情况下这种缺陷类型的反射波会出现在一次与二次波的前面。在探测过程中当探头在焊缝两侧进行探伤时,都能发现这种现象,当探头移动到能够出现最高反射波信号时,固定探头,可以适当降低仪器的检测灵敏度。用手指沾一些油对焊缝边缘咬边出进行轻轻敲打,对反射信号进行观察,当反射信号有明显的跳动情况时,则说明是咬边反射信号,证明该缺陷类型为咬边缺陷。
2.4裂纹缺陷类型的探测识别
通常情况下,裂纹的回波高度都比较大,波幅较宽,其具有多峰现象。将超声波探头进行平移,观察反射波以连续形式出现,波幅会有一定的变动;将探头进行转动检测时,波峰出现上下错动的现象。此外,裂纹缺陷也比较容易出现的焊缝热影响区,且裂纹多数情况下垂直于焊缝,进行探测时,应该在平行于焊缝的方向上进行检测,这样比较容易使超声波直射到裂纹,便于发现裂缝缺陷。
2.5未焊透缺陷的探测识别
未焊透缺陷类型主要是由于焊缝金属没有填到接头根部的原因造成的。这种缺陷类型主要分布在焊根部分,且两端较钝,具有一定的长度,也是平面缺陷类型的一种。将探头进行平移检测时,会发现未焊透缺陷的反射波的波形比较稳定;在焊缝两侧进行探伤检测时,基本上都能得到反射波幅一致性较好的反射波,从而能够判断识别出缺陷的类型。
2.6未熔合熔焊缺陷类型的探测识别
所谓的未熔合熔焊缺陷类型主要是指焊道与母材之间或者焊道与焊道之间在焊接过程中未完全熔化结合而形成的缺陷。当使用超声波进行探伤检测时,超声波可以通过垂直射到其表面的方式,得到波峰较高的回波。但是,在实际的探测过程中如果探伤方式和折射角的选择不合理,也可能造成漏检的问题。对于未熔合熔焊的缺陷的检测识别判断依据的特征有:当探头进行平移检测时,波形呈现比较稳定;进行两侧的探测时,反射波的波幅会产生变化,且存在只能在一侧能探测到的情况。
3.伪缺陷类型的识别
3.1仪器杂波类伪缺陷波类型
这种伪缺陷波通常是在不接探头的情况下,由于设备仪器性能不良以及探头灵敏度调节过高等原因引起的,在荧光屏上表现的单峰或者多峰的波形。当接上探头进行工作时,该波形在荧光屏上的位置维持不变,通过降低探头灵敏度的方法,可以消除这类伪缺陷波。
3.2焊缝表面沟槽引起的伪缺陷波
焊缝表面沟槽的缺陷波类型主要集中表现在反射波方面,使用超声波探测焊缝表面时,会因为其表面的沟槽而产生沟槽反射波。这种波形一般会出现在一次或者二次波偏后的位置,波形表现不强烈,较为平缓、迟钝。
3.3焊缝交错位置引起的伪缺陷波
在钢材料进行加工坡口工作中,由于上下刨的不对称或者焊接过程中的偏移都会形成焊缝错位的问题,由于上下焊缝焊偏,在进行超声波探伤检测时,焊角的反射波同焊缝缺陷波十分相似,但是,通过转移到另一侧进行探伤时,其一次波前不会出现反射波,以此可以最为避免误判的标准。
4.结语
综上所述,造成缺陷的原因较多,且缺陷类型众多,不同的缺陷类型在超声波探伤识别过程中的表现也有所不同,但是也不排除个别有类似的情况,因此,在实际的超声波探伤技术应用过程中,要不断积累经验,且在实际探测中还要熟悉各种缺陷类型的不同探测方式、回波类型以及反射波特征,最终判断识别出正确的缺陷类型,为采取相应的有效处理措施提供指导。
【参考文献】
[1]李政,罗飞路,邹毅.基于PC机的多通道超声波探伤系统[J].无损检测,2009(01).
超声波焊接篇2
关键词小径管;超声波检测
中图分类号TK22文献标识码A文章编号1674-6708(2012)78-0170-02
火电发电机组小径管焊接接头无损检验过程中,由于使用射线检测技术受到现场条件的制约,不能对所有的焊接接头进行100%射线检测,因此必须对受条件制约的管子进行超声波检测。为了提高火力发电厂安装工程的质量,我对小径管超声波检测方法进行了一些探讨。从而提高了小径管焊接接头超声波检测的可靠性和准确率。
1检测范围与难点
小径管超声波技术适用与对管道外径小于或等于159mm,壁厚大于或等于4mm、小于或等于14mm的铁素体类钢制承压管道单面焊接双面成型的中厚壁管焊接接头手工A型脉冲反射法超声波检验。
射线检测对裂纹这些面积性缺陷容易产生漏检现象,裂纹的检出率大大降低。因此,使用小径管超声波检测,对小径管焊接接头面积性缺陷检出率高,能更好的解决此类问题。
超声波技术本身对于面积性缺陷有着较高的灵敏度跟检出率,比如:裂纹,未熔合,未焊透等等。但是对于体积性缺陷的灵敏度不高,甚至容易发生漏检,比如:气孔。这就要求小径管超声波检测人员要有丰富的理论知识和实践经验,并且细心,负责,及时做好记录。
2准备工作
2.1仪器的选择
由于小径管多为薄管,曲率半径小,在检测过程中容易产生杂波干扰,最好使用数字式超声波检测仪进行检测,在平时工作中使用的是泛美EPOCHLT的数字式超声波检测仪进行检验。
2.2探头的选择
小径管焊接接头宜使用前沿短,前沿长度L≤5mm,折射角大的小探头,由于较高的探测频率可以改善探头的指向性,并且降低杂波对检测的干扰,推荐使用频率为5MHz的抬头。DL/T820-2002《管道焊接接头超声波检验技术规程》推荐的折射角如下表:
3小径管超声波探伤的实际应用
对福建华电漳平火电有限公司2×300MW火电机组锅炉受热面过热器系统进行小径管超声波检测,管子规格为φ63.5×7,如下图所示。
3.1检测前的准备
1)工件表面的处理:尽量不采取机械工具对工件表面进行打磨。油漆结合的好的情况下,也不需要进行打磨;
2)在小径管对接接头的超声波探伤过程中,使用的耦合剂是纤维类的,比如浆糊,而不是使用油类作为耦合剂,浆糊可以使探头滑动的更好,降低杂波的干扰;
3)探头与焊接接头接触面之间进行耦合存在缝隙容易对检测造成干扰,形成变形波,所以应该将探头打磨到与焊接接头能较好的耦合。
3.2仪器调整
使用泛美EPOCHLT数字式超声波检测仪进行检测,探头前沿为5P5×6K3,探头前沿为5mm。在小径管专用试块上面进行调整灵敏度,扫查速度为深度1:1,扫查灵敏度为φ2×15-18dB。
3.3焊接接头的信息
φ63.5×7的过热器管子,采用手工氩弧焊打底,手工焊盖面的焊接接头,常见的焊接缺陷有:裂纹,未焊透,未熔合,气孔,焊瘤等等。检测要区分的是根部内凹或者咬边等伪缺陷的影响。
3.4缺陷的波形分析
变形波对小径管焊接接头缺陷的判断形成了干扰,存在一定的鉴别难度。在超声波一次声波范围内的缺陷基本上都是缺陷;二次声波范围如果定位在焊接接头同侧也是缺陷,定位在焊接接头另外一次则不能定为缺陷。因此,实际情况因以缺陷的位置判定为准。有如下的几种缺陷波形:
1)气孔。当气孔的尺寸大到一定程度时,它的反射波幅反而减小。当气孔的直径小于1mm时,它的反射波幅随着气孔尺寸的增大而增大。当气孔直径比1mm大时,反射波幅由尖变宽。因此,大尺寸的气孔应配合射线检测进行最终判定;
2)密集气孔。超声波探头前后左右移动,它的反射波幅不高。在基准线附近会出现起起伏伏的宽波形反射波;
3)未熔合。用一次波检查反射波不会很高,但是用二次波检测反射波很高,并且定位在焊接接头边缘,所以二次波判定未熔合比较准确;
4)未焊透。反射波类似于端角反射,回波较强,在焊接接头两侧都能探测到,靠近焊接接头中心或者一侧,沿着焊接接头方向有一定的长度性;
6)裂纹。接头两端判定均出现反射波,波形尖且较高,焊接接中心定位与一个垂直性缺陷,测量它的水平位置不是同一个点;
7)焊瘤。焊瘤一般出现在焊接接头一个壁厚的厚度范围之外。水平定位在中心线远离探头的一侧,波形不尖且波幅较宽。
3.5检测结果加以验证
通过以上措施,并加以严格控制工艺,认真做好每一步的检测。此次共接受委托的过热器焊接接头数量为183个,经过超声波全部检查,结果发现有密集气孔2个,未焊透或者未熔合6个。在焊接接头的返修过程中,超声波检测人员参与了有缺陷的焊接接头的打磨,发现缺陷与检测结果一致,足以说明了这次的小径管超声波检测结果准确。
4结论
随着数字式超声波检测仪,高性能高灵敏度探头的发展与更新,小径管焊接接头的超声波检测将更加准确,缺陷的定性跟定量将更加的精确。使得小径管超声波检测投入更多的生产实践中,它的检测将比射线检测更方便,更快捷,使用过程更安全环保,更大程度地发挥了它的经济效应。
参考文献
[1]中国机械工程学会无损检测分会,编.超声波检测[M].北京:机械工业出版社,2000.
超声波焊接篇3
关键词:钢结构焊缝超声波检测
中图分类号:TU391文献标识码:A文章编号:
前言
声波探伤是通过超声波仪探头产生和发射高频超声波到待检材料中,利用超声波在同一均匀介质中按恒速直线传播,而从一种介质传播到另一介质时,它会产生反射和折射的原理,再用探头接收这些反射、折射的超声波到超声仪,由超声仪放大显示在超声显示屏上,超声波探伤工作者根据显示的波形和波高来分析和判定缺陷的类型和大小的检测方法。超声波探伤具有高灵敏度、操作简便、探测速度快、成本低且对人体无损伤的优点,故得到广泛应用。其缺点是该探伤方法进行定性定量的评定受探伤人员的经验和技术熟练程度的影响较大,且不直观,至今仍难达到精确评定的要求。
一、超声波检测的特点和适用范围
寸的锻件、轧制件、焊缝和某些铸件,无论是钢铁、有色金属和非金属,都可以用超声波法进行检验。各种机械零件、结构件、电站设备、船体、锅炉、压力容器等,都可以采用超声波进行有效的检测。有的采用手动方式,有的可采用自动化方式。就物理性能检测而言,用超声波可以无损检测材料厚度、材料硬度、淬硬层深度、晶粒度、液位和流量、残余应力和胶结强度等。
1超声波检测的特点
超声波是超声振动在介质中的传播,它的实质是以波动形式在弹性介质中传播的机械振动,其频率在20KHz以上。超声波检测可探测厚度较大的材料,且具有检测速度快,费用低并能对缺陷进行定位和定量,对人体无害以及对危害性较大的面积型缺陷的检测灵敏度较高等优点。因此,超声波检测已经发展成一种很重要的无损检测方法,在生产实践中得到了广泛的应用。超声波被用于无损检测,主要有以下几个特性:
(1)超声波在介质中传播时,遇到界面会发生反射;
(2)超声波指向性好,频率愈高,指向性愈好;
(3)超声波传播能量大,对各种材料的穿透力都较强;
(4)超声波的声速、衰减、阻抗和散射等特性,为超声波的应用提供了丰富的信息,并且成为超声波广泛应用的条件。
2超声波检测的适用范围
超声波检测是工业无损检测中应用最为广泛的一种方法。就无损检测而言,超声波适用于各种尺寸的锻件、轧制件、焊缝和某些铸件,无论是钢铁、有色金属和非金属,都可以用超声波法进行检验。各种机械零件、结构件、电站设备、船体、锅炉、压力容器等,都可以采用超声波进行有效的检测。有的采用手动方式,有的可采用自动化方式。就物理性能检测而言,用超声波可以无损检测材料厚度、材料硬度、淬硬层深度、晶粒度、液位和流量、残余应力和胶结强度等。
二、钢结构焊缝超声波检测
根据《钢结构工程施工及验收规范》GB50205-2001规定,对一级、二级焊缝内部质量应进行超声波探伤检测,检测比例分别是焊缝长度的100%、20%。对于手工电弧焊,同一制造企业的焊工焊接水平可能存在较大差异,抽取部分构件的20%进行焊缝检测往往不能有效的反映整批焊缝质量。标准强调了探伤比例按每条焊缝长度的百分数计,且不小于200mm。而绝对不是部件、构件焊缝总长度的百分数,这是保证每条焊缝质量的硬性规定。
抽检工作分两种情况,对于制造厂质保体系具备探伤条件的厂家,根据其企业内部检验报告,进行抽样核实,其探伤比例适当减小,为焊缝数量的20%。对于制造厂质保体系不具备探伤条件的情况,严格按照GB50205-2001规定,探伤比例按每条焊缝长度的20%,且不小于200mm操作。在严格的管理下,制造厂也对焊缝探伤工作引起了足够重视。一些厂建立了自检体系,并不断通过检验,发现和改进焊接工艺中存在的问题。目前,不少单位对接焊缝已改用埋弧自动整板拼接后切割的方式,有效的控制了焊接质量,同时,在切割组装前进行超声波探伤,既满足了GB50205-2001规定,又相对减小了工作量。焊缝超声波探伤要求探伤人员具有一定的超声理论知识和丰富的实际操作经验,同时还应了解焊接工艺过程、材料特征和可能产生缺陷等,只有这样,才能采取适当的探测方式,并作出正确的判断。
1探头选择
探头晶片尺寸较大时,探头入射至反射体的能量大,且指向角较小,能量相对集中,发现远距离缺陷能力强。但通常晶片尺寸大的探头,前沿较大,一次波能直接扫查的区域减小。探测频率相同时,晶片尺寸小,有利于发现薄板焊缝缺陷。大K值探头,一次波能直接扫查的区域也较大,但实际使用中,K3.0的探头会有不同程度的表面波干扰,增加缺陷判断的难度。当然,表面波与缺陷波还是能区别的,在一定范围内前后移动探头,表面反射波讯号通常始终存在,且波幅变化不显著。而缺陷波只有探头在特定的位置,才具有最佳的反射条件,因而,发现缺陷波时前后移动探头,波幅变化显著。
2缺陷讯号的判别
在探伤过程中,示波屏上常会出现一些非焊缝内部缺陷引起的反射讯号,主要有焊角反射、咬边反射及反沟槽射等。咬边属于焊缝的表面缺陷,咬边一般有一定的长定,可通过表面检查加以判别。焊角反射和沟槽反射可通过反射波在示波屏上的位置计算得到水平距离及垂直距离,与焊角和沟槽的位置相同;用手指沾油在焊角和沟槽处轻轻敲击,反射波会上下跳动。
3缺陷性质评判
在实际探伤中,焊缝中常见的缺陷主要有气孔、夹渣、未焊透和未熔合。根据缺陷波的大小、位置、探头运动时波幅变化的特点,结合工艺情况,可以对缺陷的性质进行大致的估计。气孔一般产生于引弧和熄弧处,在我们的实际工作中,发现一些制造厂不严格按焊接工艺生产,不加引弧板和熄弧板,往往这种情况下,焊缝的两端问题较集中。气孔缺陷探头稍一移动,波形即消失,从各方向探测,可得到大致相同的反射波,缺陷当量一般不大。夹渣一般波幅也不高,但从各方向探测时,缺陷当量各不相同。未焊透的位置根据坡口型式,一般在焊缝中部、焊缝两侧和焊缝根部,通常有一定长度,反射波幅较高,且从焊缝两侧探伤时,能得到大致相当的当量。
由于严格把关及宣传,近年来某市的钢结构焊缝质量有了明显的提高,一次抽查合格率已达95%以上。我们也曾应邀到临近县市协助进行钢结构焊缝超声波检测,其结果不仅焊缝外观不符要求,内部质量更不如人意。这充分说明了严格执行GB50205-2001规范的必要性。但目前不少钢结构制造厂尚未具备焊缝内部质量超声波检测的自检能力。因此,建议进一步加强超声波监督抽检力度,同时加强钢结构生产体系的资质认证,完善企业内部质保体系。
结束语
随着我国钢产量迅速增加,建筑物中钢结构和混合结构的应用越来越普遍,这些钢结构建筑物中,钢构件之间多采用焊接连接,如钢梁与钢梁的连接、钢梁与钢柱的连接、直接相贯的钢管桁架连接等,而焊接作为钢结构中应用最为广泛的一个基本连接方式,然而、由焊接问题造成的事故也越来越频繁,事故的危害性也越来越严重。故而,对于采用焊接连接的钢结构,提高和保证其焊接质量已成为当前焊接生产中的关键问题。为了判定焊接结构或焊件在成型后能否满足使用要求,而又不进行大面积破坏性试验的情况下,能够针对钢结构焊缝进行无损检测的技术在目前国内外钢结构领域应用广泛。
参考文献
[1]任常海.钢结构工程的检测[J].黑龙江科技信息.2007(03)
[2]任森智,张新胜.我国钢结构焊缝无损检测探析[J].山西建筑.2007(15)
超声波焊接篇4
变形,进而推导出焊接接头区域理论温度;然后通过人工热电偶试验测得铝片表面及铝片一铜管间的温度.再结合接头扫描电镜图片进
行验证,认为焊接接头的形成是由材料本身的塑性本质、一定的摩擦升温、工具头竖直方向压力3个因素共同作用的结果.整个过程使
接头区域材料发生充分的塑性变形,破坏并清除氧化物、油污,使焊件材料原子之间发生力的作用而形成金属键合。
关键词:铝片一铜管太阳能集热板;超声波焊接;焊接接头
中图分类号:tg453、9文献标识码:a
当前金属管板式太阳能集热板大多采用铜管一铜片的组
合,这种组合虽然有利于材料的焊接,易于制造,但成本较
高,不利于普及。而铝的密度小,价格比铜低,工业上经常用
铝代铜.因此用铝片代替铜片作为太阳能集热板的吸热板可以
大大降低成本。虽然铝的导热性能不及铜,但在[,!]材料很薄的情
况下并不影响整体效果.这种新的组合也是金属管板式集热板
的发展趋势。然而,铜铝属于不同种金属,它们之间存在电极
电势差,铜的线膨胀系数比铝的大0.5倍。再加上熔点的差异、
铜铝间易形成金属间化合物等原因.容易引起铜铝接头电化学
腐蚀,同时铜铝变形不一致也容易产生裂纹、夹杂层或出现脆
性金属间化合物等.这些缺陷将会降低接头强度。
为克服铜一铝焊接时所出现的缺点,一般采用铜一铝压力
焊。如摩擦焊ⅲ、超声波焊]、真空扩散焊等焊接方法.获
得电气性能、抗老化性能、抗腐蚀性能、使用寿命都比较理想
的焊接接头。jiromarutsujino.tetsugiueoka等日本学者
长期从事金属超声波焊接研究,对超声波焊接过程中的一系列
问题作了比较全面的探讨.如:频率和压力变化对焊接质量的
影响[31,实测得到铜铝焊接温度超过436℃,同时对铜、铝、
金等金属的焊接性能进行了深入而细致的研究,认为超声波
焊接对各种塑性良好的金属材料来说,只要选择合适的设备和
工艺参数,都可能获得良好的焊接接头。jamesekrazanowski
通过透射电镜(tem)研究焊接区域组织。认为金属超声波焊
接机理是一个金属粘合的过程,而扩散和再结晶等物理冶金反
应在接头成形机理中并不起主要作用[9]。本文从铜铝材料性能
分析人手,推导焊接区域温度,同时结合实测温度和焊接区域
收稿日期:20__—04—12:修回日期:20__—07—07
基金项目:广州市科技攻关重点项目(20__z3一do101)
扫描电镜图片探讨铜一铝超声波焊接机理。
1焊接试验及过程分析
超声波焊接设备包括:超声波发生器、换能器、聚能器
(变幅杆)和工具头等,如图l所示。焊接参数见表1。
图1超声波焊接设备
表1焊接参数
汽缸
动块
导轨
频率功率工具头转速焊接压力振幅铝片厚度铜管厚度
f/khzfi,kw(r·min-‘)p/mpaa/1.zm占l/mmnull
15344—490.4、30n21.0
铝片一铜管太阳能集热板的焊后样品如图2所示。
图2铝片一铜管太阳能集热板焊后样品
weldingtechnologyvo1.36no.5oct.20__·试验与研究·15
1.1材料处理
铜和铝极易在空气中被氧化,在光亮清洁的表面就已经有
约200个分子厚度的氧化膜存在,而且氧化膜也是由晶体组成,
本身也存在不饱和的分子,能够吸引对称性较弱的极性分子
(如水分子、有机物分子等),形成一层油污和水气膜,这些物
质的存在导致表面凹凸不平,使材料原子问距离增大,难于进
行焊接。
1.1.1铜管表面套拉与翅化
根据金属超声波焊接机理,对材料表面要求高,针对上述
铜管表面状态,需要击碎、破坏、清除铜管表面油污及氧化膜
使其暴露出纯净的金属表面,主要有两步:
第一步,铜管的表面套拉,套拉过程如图3所示。
套拉方向
图3套拉过程示意图
其作用有:①全面刮削铜管表面.比较彻底地破坏表面氧
化膜暴露出纯净的金属表面;②由于进行的是冷加工.可以适
当提高铜管硬度,有利于随后的焊接及增加变形抗力以保证在后
续的挤压中维持圆管形状;③将铜管的直径缩口至需要的尺寸。
第二步,利用专用工具头,表面具有微翅结构,如图4a所
示,在铜管表面预先滚压一次,进一步破坏和清除待焊部位的
表面氧化膜。且在铜管表面加工出微翅结构,如图4b所示。
(b)铜表面微翅结构
图4袭面有微翅结构的工具头及其预滚压铜管后形成的铜表面翅化结构
其作用主要有:①增大铝片和铜管的接触面积,增加机械
嵌合的可能性;②增大接触区域粗糙度,增大摩擦,增加析热
量,从而形成局部高温,有利于焊接;③破碎、清理旧表面,
振动滚压出新鲜表面,为金属键合形成接头提供条件。
1.1.2铝片处理
铝片薄,只能用钢丝刷清除其表面氧化膜,使铝片与铜管
之间通过新鲜表面充分贴合,为原子力起作用提供条件。
1.2焊接接头形成
铝片一铜管超声波金属焊接过程如图1所示,工具头在汽
缸压力作用下,其表面微翅压入铝片后与铝片发生摩擦.然后
带动铝片以频率,相对铜管振动,在铝片与铜管间剧烈摩擦,
焊接接头区域温度升高,材料发生塑性变形。材料塑性变形、
铝片与铜管间的高频振动摩擦、工具头竖直方向的压力三因素
共同作用,破坏并清除金属表面的油污和氧化物,使彼此的纯
净表面暴露并贴合,在贴合面形成牢固的接头。
2焊接影响因素讨论分析与试验测定
超声波焊接振动幅度只有几m到几十m,而且铜铝的塑
性良好,其振动摩擦作用区域小,很难用直接测温法准确测定
焊接温度;而间接测温,即通过分析焊接接头组织的扫描电镜
图片(sem)或透射电镜(tem)图片,根据接头组织推断焊
接过程所能达到的温度的方法也受到了限制,这是因为sem图
片难于准确判定组织结构,而tem样品难于制作。
由于测温方法上的限制,各研究者所得结果相差较大.使
得超声波金属焊接温度的作用成为一个有争议的问题,同时学
者对超声波焊接机理也有不同看法。本文先从理论推导出焊接
区域材料主要发生塑性变形而非弹性变形,后通过摩擦力做功
理论推导出焊接区域理论温度,同时通过人工热电偶试验测出
焊接区域实测温度,并结合试验测定焊接接头区域显微硬度.
综合分析超声波金属焊接机理。
2.1焊接时材料的变形情况分析
从图4b材料表面翅化后形态可以看到.焊接区域铜管表面
产生很大的塑性变形,振动摩擦和材料塑性变形能够破坏、挤
压、清除金属表面氧化物和油污,这对超声波焊接是非常有利
的。
从图5ae实测应力一应变关系曲线和图5b理论应力一应变
关系曲线可以看出,材料弹性应变小于0.5%,本文以0.5%计
算:
f=f,(1)
式中:fn为材料厚度,1.2mm;8为应变,o.5%。
可见,弹性变形约为6m,而工具头振动幅度a为3o
m,所以振动摩擦影响区域主要发生塑性变形,这可以从图
4b的铜管表面翅化后的sem图片看出,工具头的纵向振动不但
16·试验与研究·焊接技术第36卷第5期20__年10月
在铜管表面压出新鲜表面,而且在纵向摩擦力的作用下,工具
头表面微齿挤出的材料被翻了过来,发生了大的塑性变形,这
对焊接是非常有利的。
量
-
z
b
0.0020.0040.0060.0080.010
6(%)
(a)工业铝实测应力一应变曲线
6(%)
(b)铝等塑性材料理论应力一应变关系曲线
图5工业铝的实测及理论应力一应变关系曲线
2.2摩擦做功方程
由华南理工大学机械工程学院在超声波焊接方面的研究11].
可得到焊接区域的温升公式为:
at-4afw~’at一
,(2)
cpn
式中,a为振幅,mm;f为频率,khz;为能量吸收率,
为摩擦系数;p为压强,mpa;at为焊接时间,s;c为比热
容,j/(kg·℃);p为材料的密度,g/cm;为受影响厚度,mm。
将公式(2)运用到铝片一铜管的超声波焊接,计算焊接
区域温度,由于铜管和铝片厚度小。其对密度、比热容等影响
非常小,所以铜片一铜管焊接和铝片一铜管焊接不会有非常大
的差异。假定焊接时摩擦振动影响区域厚度h是分别从焊缝向
铝片和铜管壁各取1/2(即:=(0。1+0.5)mm=0.6mm,即热
影响区为0.6mm),同时铝密度2.78g/cm,约为铜密度8.96g/cm
的1/3,铝的比热容为0.88j/(kg·℃),而铜的比热容为
0.385j/(kg·℃).将比热容及密度也按比例折算为合成比热
容、合成密度。
由公式(2)得:
at-4afrtu~
.
at
一
.(3)
c1—1-zhl一2
式中:c_2为材料合成比热容,取值410j/(kg·℃);p1-2为材料
合成密度,取值7,8g/cm;h1-2为振动摩擦影响材料厚度之和,
0.6mm;助压强,通过换算可得到p=20mpa;at为等效点焊
时间。s。
p可以通过焊点的面积为4minx4mm.工具头汽缸压强为
0.4mpa.汽缸直径为32mm换算得到,焊接区域的压强为汽
缸压强的50倍,所以助20mpa。
焊接行程为1886mm.而连续滚动焊接可看成是点焊叠
加,焊接时间通过测定为18.76s。可以通过将工具头压下,而
不做直线运动测出点焊接头是面积为4mmx4mm的正方形.
计算其点焊时间£为0.04s。
由式(3),代入各相关参数得:
a/’-730rgt。(4)
超声波焊接过程中能量吸收率和摩擦系数很难准确测量,
但肛的范围可以通过试验手段得到,同时结合相关文献查到
铜一铜表面清洁度较高时为1,4.而在一般情况下为0,2左右。
之所以产生这种差异.主要是因为在清洁铜一铜摩擦副的情况
下,铜的塑性好,导致摩擦系数非常大;但在一般情况下,铜
的表面容易发生氧化而覆盖一层氧化物,氧化物硬度大,且有
一定的性能.使摩擦系数大为降低,铝一铜的摩擦系数无
资料可查.只能以测量和类比计算为准。
本试验中,由于铜管表面预先经过滚压,自然表面全部挤
压翻滚一次而露出新鲜表面.同时铝片也经过了清洗并在焊前
进行了打磨处理,这就和焊接时的条件接近,所以铝片一铜管
之间的摩擦系数应取较大值。通过摩擦系数测定试验,推导出
摩擦系数介于0,5—0.8之间。
能量吸收率值可以和切削时切削区域情况类比确定,切
削时有70%一90%的热量集中在切削区域,金属超声波焊接时
工具头和焊件金属紧密贴合,焊接区域与切削区域情况相似。
工具头与铜铝间的振动摩擦影响范围小,铜铝均为理想塑性
材料,工具头则可以看成是理想的弹性体。超声波从工具头
传出到铝片铜管接触界面处.由于铜铝材料的大塑性变形,
超声波在界面处不能远距离传递,大部分的能量以体积变形、
材料内部温升等形式被接头区域材料所吸收,因此吸收效率
为0.7—0.9。
从上面的分析可知,能量并不能远距离传递,其影响区域
非常小.主要集中在铜铝塑性材料的表层,振动摩擦影响不到
深层区域,式(4)中,为0.5—0.8,为0、7~0.9,所以为
255525℃(室温为24—26℃).即焊接区域理论温度推导为
280550℃
weldinztechnolo~vo1.36no.5oct.20__·试验与研究·17
2.3试验温度测定
直接法测温试验按如下方法设计:在铝片表面布置一个热
电偶,焊接时,工具头直接从热电偶探头上滚压过,此时所测
温度为焊接时工具头和铝片之间振动摩擦在铝片表面所达到的
温度,测量结果如图6a所示,在室温为24~26℃条件下测得最
高温度为392℃,最低温度为284℃。选用相同的工艺参数,
相同的材料进行测试。在焊接接头形成区域的铝片一铜管间布
置一个热电偶,其所测得最高温度为144℃,最低温度仅44℃,
整个温度一压强曲线如图6b所示。
汽缸压强pa汽缸压强pa
(a)铝片表面温度一汽缸压强曲线(b)焊接接头区域温度一汽缸压强曲线
图6温度一汽缸压强曲线
2.4焊接区域显微硬度测定
在显微硬度计上进行焊接接头显微硬度测定。母材铜的硬
度为hv90~92.9,而铝的显微硬度为hv42~47。从铜管内表面
开始测,其所测得硬度值分布如图7所示。
宝
越
罄
揠
叫
到铜管内壁的距离l/mm
m7样品横截面显微硬度分布
从图7中可见,最高硬度hv942在焊接接头界面处,当压
痕菱形刚好落在铜铝两侧时,铜边缘发生塑性变形而拱起,导
致测量上的困难,而铝在交界面边缘处发生塌边,出现碎状,
并且可以看到结合面处出现微小裂纹。结果还显示出,远离结
合面处,铝侧的硬度值也还是比较大,分析认为这是由于焊接
工具头表面微齿高度为0.6mm,而铝片厚度只有0.2mm,焊
接时,微齿从铝片表面压穿铝片,而且接触到铜管表面,在焊
接时发生了大的塑性变形,而且由于温度的影响。在铝侧生成
了一定量的a120,,而a120,的硬度较大,并且同时存在一定的
铝的加工硬化所造成的。
3超声波焊接机理分析探讨
超声波焊接接头区域呈现复杂和多样的显微组织,有关焊
接过程中所能达到的焊接温度是多少,及焊接过程中起主导作
用的是焊接温度、机械嵌合、物理冶金反应还是金属原子之间
的键合都存在争议。下面结合试验数据和相关理论,对铜一铝
超声波焊接机理进行分析讨论。
3.1焊接区域温度分析与讨论
焊接温度对金属超声波焊接过程有重要影响,从试验测
得铝片上表面最高温度为392℃。铝片铜管接头区域最高温
度只有144℃。从理论温度计算来看,其最高温度为550℃,
均没有达到焊件材料的熔点(铝的熔点为660.4℃,铜的熔
点1083℃)。文献[4]认为,焊接区域温度不低于436℃,
该值与本文试验测得的铝片上表面温度及理论推导温度较为
接近。所以,可以认为,试验测得的温度(392℃)为焊接
区域真实温度。
3.2机械嵌合、物理冶金反应
较多的压焊专家认为。材料间的嵌合有助于材料原子间
的相互靠近,说明焊接也是塑性变形的结果,这种嵌合结构
在金属超声波焊接接头形成过程中具有重要作用。但从图8
铜一铝接头过腐蚀sem图片来看,与铝结合处,铜管表面为一
微小片面,看不到明显的材料彼此间机械嵌合,而看到铜管
表面还残留有未腐蚀的绒状铝存在,表现出明显的相互间贴
合。所以本文认为机械嵌合对金属超声波焊接有一定的作
用,但不起主要作用。
图8铜一铝焊接接头过腐蚀扫描电镜图
jamesekrazanowski通过经典扩散理论分析认为,焊接过
程中原子的扩散距离不到一个原子直径。从上述显微硬度测
定来看,铜在远离焊接接头区域的硬度和母材是一样的,但是
在接近接头区域时其显微硬度显著增大,接头区域达到
l8·试验与研究·焊接技术第36卷第5期20__年lo月
hv942,同时有细小裂纹存在,在铝侧还看到破碎的铝存在,
这表明生成了金属间化合物。李亚江等人在研究铜一铝扩散焊
时,界面出现硬度峰值hv780,分析认为明显存在金属间化合
物[8]。扩散焊接时间越长.铜铝焊接过程越容易出现金属间化
合物,但超声波焊接持续时间短,金属间化合物可能只是在焊
接后才在接头区域形成,而非焊接过程中出现。因此分析认为
物理冶金反应在焊接后出现,对接头的形成作用不明显。
3-3金属键合过程
从材料表面的状态分析可见.正是由于表面的凹凸不平和
表面氧化物的存在,使得焊接难以进行。从压焊的机理可知,
当材料表面原子贴近到0.3—0.5nm范围.即3—5个原子的距离
时,原子之间的作用就能够发生,并在压焊的接头形成过程中
起主导作用。超声波的作用机理和压焊有较大的相似性,在弹
塑性理论推导过程中可以看到,铜铝的塑性变形只有6m,
而超声波的振动幅度为3om,铜铝塑性好,铜的显微硬度为
hv90—92.9。铝的显微硬度为hv42~47,焊接工具头的硬度为
hrc5862,相差较大。焊接时,工具头在焊接过程中压穿铝
片.达到铜管表面,带动铝片和铜管摩擦,同时工具头在竖直
方向压力作用下。使得铜管表面和铝片同时发生充分的塑性流
动,将氧化物、油污等挤出焊接接头形成区域,或将氧化物碎
片通过铜和铝的充分塑性流动而压人铜铝材料里层,使之不能
停留在接头形成界面层。让纯净的金属材料原子之间能够相互
接近到原子作用力范围内。从jamesekrazanowskit]的透射电
镜图片中看到碎片和孔洞的存在,原因就是焊接时由于材料接
触界面金属的塑性流动,使得表面氧化层有的被挤出,而有的
卷入基体材料,如果金属氧化物和母体材料的接触性不好,就
可能使得在存有氧化物碎片的地方留下孔洞。
超声波能够将能量传递给材料,能够降低材料原子的活
化能。在焊接过程中,焊接温度或压力并不单独决定焊接接
头的形成,而是焊接温度、焊接压力、材料本身的塑性共同
决定了接头的形成。压力、温度、材料本身的塑性综合决定
了材料原子的能量状态,从而决定了材料的塑性流动等性
能,只要3个因素综合作用,能够使得焊接材料原子间相互
接近no.3—0.5nm的距离,原子问作用力能够起到主导作用,
焊接接头的形成就是可能的。在图8中有许多绒状铝还粘连
在铜管的表面,可以看到焊接区域铜和铝接触界面处的粘连
状态。但要达到这种状态,材料的塑性流动是充分的,各个
接头的形成条件可能并不相同,但是,材料本身的塑性、压
力和焊接温度相互协调。能够使得材料发生塑性流动,界面
充分贴合,从而形成接头。
4结论.
(1)从理论推导和试验实测得到焊接温度均达不到焊件材
料的熔点。
(2)焊接接头形成过程中。物理冶金反应对焊接接头的形
成并不起主要作用。
(3)铜一铝超声波焊接是由材料本身的塑性、一定的摩擦
升温和工具头竖直方向压力共同作用下.在材料发生充分的塑
性流动及氧化物、油污等阻碍材料焊接的物质被破坏、清除或
压人母体材料的基础上发生的焊接材料原子之间由于原子间作
用力而形成金属粘合的过程。
参考文献:
[1]ednicholas.frictionweldingofcoppertoaluminum[j].metal
construction,march,1975:12—17.
[2]geo~egharman,johnalbers.ultrasonicweldingmechanismas
appliedtoaluminum—andgold—wireboldinginmieroeleetmnies[j].
ieeetransactionsonparts,hybridsandpackaging,1977,13
(4):406—412.
[3]jiromarutsujino,koichihasegawa,yukiosone,eta1.frequency
characteristicsofultrasonicwirebondingusinghighfrequency
vibrationsystemsof40khzto780khz[a].ultrasonics
symposium[c].1996:1021—1026.
[4]jiromarutsujino,himyukiyoshihara,kazuyoshi,eta1.welding
characteristicsandtemperatureriseofhjshfrequencyandcomplex
vibrationultrasonicwirebonding[a].ctrasonies[c].1998.59—65.
[5]jiromarutsujino,tetsugiueoka.weldingcharacteristicsof
variousmetalplatesultrasonicseamandspotweldingsystemsusinga
complexvibrationweldingtip[a].ultrasonicssymposium[c].20__:
669—674.
[6]jiromarutsujino,tetsugiueoka,ichirowatanabe,eta1.
newmethodsofultrasonicmetalwelding[a].uetrasoniessymposium
[c].1995:405—410.
[7]jiromarutsujino.recentdevelopmentsofultrasonicwelding[a].
ultrasonicssymposium[c].1995:1051—1060.
[8]李亚江,吴会强,陈茂爱,等.cu—al真空扩散焊接头显微组织分
析[j].中国有色金属学报,20__,11(3):424—427.
[9]jamese,krazanowski.atransmissionelectronmicroscopystudyof
ultrasonicwirebonding[j].transactionsoncomponents,hybrids
manufacturingteohnology.1990,13(1):450—455.
[1o]黄文,周元鑫,马钢,等.工业纯铝l2应变率相关的拉伸力
学性能研究[j].机械科学与工艺,20__,10(3):263—267.
超声波焊接篇5
为使超声检测结果易于评定,用相控阵探头在焊缝两侧进行扇形扫查,观测其图像显示。利用数据分析软件的屏幕设置,能使缺陷信息的三维数据易于识别、定位和定量。体积状缺陷先观测代表体积状缺陷的横孔反射信号的显示。图3即为相控阵探头探测壁厚T=25mm焊接试样时获得的超声S扫描(扇形扫描)的成像结果;由左右两图像显示,即可从焊缝两侧观察到被检焊缝体积的声束覆盖范围和缺陷S扫描显示特征(左上和右上为S扫描图像,显示缺陷在壁厚方向的深度位置和范围;左下和右下为C扫描(平面投影)图像,显示缺陷在焊缝轴线方向的位置和长度范围)。平面状缺陷试样底面开口线槽再观测位于试样底面、代表平面状缺陷的电火花切割线槽,用相控阵扇形扫查检测到的超声回波信号的显示特征。实验证明,用给定的探测布置,要使超声波束通过含镍量相对于母材较高的焊缝金属,检测到位于焊缝远侧(即离探头较远的焊缝一侧)的热影响区的线槽是不可靠的。但从焊缝近侧(即靠近探头的焊缝一侧)还是可以检测到的。图4即为T=25mm焊接试样用相控阵探头探得位于焊缝近侧热影响区线槽的超声图像。中间小图表示h=2mm线槽经变焦放大后获得的图像。由图可见,线槽端部衍射回波信号与线槽和底面构成的端角反射回波信号很容易区别,因而可对代表底面开口裂纹的电火花线槽准确测高。
试样表面开口线槽第三步,观测位于试样表面(探测面)、代表平面状缺陷的电火花切割线槽的超声回波信号图像显示特征。对此类缺陷,若用一次波(即直射波或0.5S波)检测,显然要用更大的声束角度才能探到(即用表面下纵波甚至表面波探到)。图5即为板厚25mm焊接试样中外表面h=2mm线槽的PAUT信号的图像显示(注意:这张图像显示的是一次波成像,不是二次波成像)。这里正好彰显了PAUT不同于常规UT的优势:前者可通过电子方法,利用聚焦法则的改变,阵元激活延迟时间的改变,来改变声束探测角度,改变波型,方法简捷;而后者必须更换探头,重新调整仪器,费时费劲。同理,由于焊缝金属的高镍含量,超声波束一般很难通过焊缝金属、检测到焊缝远侧热影响区的电火花线槽或坡口面缺陷。为此,通常就用同一相控阵探头,用二次波(即1.0S波或一次反射波)扫查,使入射声波覆盖焊缝近侧上层区域。对试件表面缺陷的检测,屏幕上的S扫描声成像,一般用"镜像"显示。给出了单面焊表面焊趾裂纹PAUT二次波S扫描的镜像显示示例。T型接头结构对液化天然气储罐上的T型接头结构,可将相控阵探头置于腹板侧,用扇形(S)扫查+电子(E)扫查,探测腹板侧坡口面熔合性缺陷。在条件许可的情况下,为保证整个焊缝体积及相邻母材区全部检测到,最好在储罐内外两面都进行扫查。施探前,要制作拟合实际结构的、带特定参考反射体的专用焊接试样,通过操作演示,验证检测T型接头结构中平面状缺陷和体积状型的PAUT工艺的可靠性。最后,对多种封闭试样(缺陷不告知)和实际试件进行了半自动PAUT试验。结果表明:封闭试样和实际试件中的所有缺陷均能被检出,而且缺陷定量精确度也达到要求。使用多种声束角度和多种波型,能获得优于射线照相的缺陷检出率。作封闭检测试验时,半自动PAUT与RT双管齐下,试验结果两两对照,令人满意。
优势国际权威法规ASME锅炉压力容器法规2011版明确规定:承压设备要用超声检测取代射线照相对焊缝进行100%检测,施探前,必须制定基于车间或现场制造验收标准的超声检测工艺,而此UT工艺必须采用基于计算机声成像技术(即CITs)的半自动或全自动超声检测—目前,就是指TOFD和PAUT技术。试验研究表明,用半自动PAUT取代RT有以下种种优势:(1)检测速度快,检测结果可靠;(2)有数字化记录,便于随后数据分析和资料存档;(3)结果快捷,可随即反馈给焊工;(4)检测中无辐射影响,不影响生产流程;(5)无需消耗化学药品(显影液等);(6)不用胶片、增感屏等,费用省。结论和讨论(1)针对液化天然气储罐9%镍钢焊缝的金属组织高镍含量特点,采用半自动超声相控阵检测(PAUT)方法,通过制备带缺陷的焊接试样,依据规范要求制定PAUT工艺,而后进行"开放"演示试验和"封闭"演示试验,试验结果表明半自动PAUT能取代RT,获得优于RT的检测结果。(2)带缺陷焊接试样要求模拟被检壁厚、材料、曲率和焊接坡口等焊接工艺条件,在焊缝金属中和焊缝附近母材热影响区,特意设置典型焊接缺陷或人工缺陷,至少设置三个平面状缺陷或电火花切割(EDM)线槽,缺陷或线槽的方向应模拟平行于被检产品焊缝轴线和主要坡口面,缺陷或线槽的位置则应如下设置:a.一个表面缺陷设在试样外表面;b.另一个表面缺陷设在试样内表面;c.第三个缺陷设在试样内部。(3)对热影响区和坡口熔合面的面状缺陷,尽量用一次声程波(0.5S波)在焊缝近侧扫查下半部,而用二次声程波(1.0S波)在焊缝近侧扫查上半部。(4)操作者应充分熟悉焊接缺陷位置和性质、形态与PAUTS扫描图像的对应特征,熟悉面状缺陷的信号图像表征与测长测高方法。
超声波焊接篇6
[关键词]锂电池;超声波焊接;工艺研究
中图分类号:TP13文献标识码:A文章编号:1009-914X(2016)30-0117-01
引言:随着我国科研水平的逐步提高,现代焊接技术形式也发生了极大的创新,锂电池极耳超声波焊接形式可以突破传统螺栓连接或焊接模式,同r又打破了传统焊接中多方面焊接因素的相互影响,成为超声波焊接技术的一种新的工艺应用方向。锂电池中极耳连接的超生波焊接的分析是本次研究的主要内容。
一、锂电池极耳超声波焊接的设计原理
锂电池极耳超声波焊接技术是应用电磁感应传输原理进行焊接信息的传输,锂电池极耳超声波焊接将整体焊接的能量储存和传输都是依靠设计中的金属导电完成的,如图1[1]为锂电池极耳超声波焊接设计图。从图中设计的整体进行分析,新型锂电池极耳超声波焊接设计内部形成了简单的电流传输线路图,是焊接技术在实际应用中的动力供应脱离了外部供应的电力资源控制,从而是超声波焊接技术的应用灵活性更强,例如:从图1中结构来看,电路中具有电能,小型发电机等电路传输系统,焊接作用主要通过传感系统接受系统的焊接信号,小型供电系统进行电流供应,保障超声焊接技术的应用。
其二,锂电池极耳超声波焊接设计结构的电流是将电压转变为超声电磁声波进行工作,从图1中设计结构进行分析,锂电池极耳超声波焊接设计中换能器是实电流与超声波之间电流交换的主要平台[2],变幅器能够在机械控制领域进行机械振动能随着需求将超声波的振幅扩大,从而保障了焊接中焊头、焊座、焊件等压力整体结构在压力的作用下顺利开展工作,实现了锂电池极耳超声波焊接中的连接效果。
二、锂电池极耳超声波焊接的工艺分析研究
(一)焊接过程描述
对锂电池极耳进行超声波焊接本质是一种摩擦焊接的工艺。经过设计的超声波焊接的压头在变幅器的驱动下开始震动,从而带动被焊接材料之间进行摩擦,摩擦使其产生一定热量产生局部轻微融化,然后焊头立即对材料进行顶压焊接,实现材料之间的连接。该焊接工艺的优势在于能量输入较少,同时对极耳表面的清理要求较低。同时超声波焊接工艺的施工温度较低,在焊接过程中热影响区非常小,对锂电池内部结构影响也较小。
(二)焊接质量分析
从超声焊接技术的设计原理分析来看,新型超声波焊接技术能够保障焊接整体质量都处于相对完善的焊接结构中,超声波焊接能保障焊接中控制箱的资源供应结构完善。与传统的焊接相比,超声波焊接技术打破了焊接材质的限制,无论焊接的材质的熔点性有何不同,都能够保障锂电池中极耳焊接的可靠性;同时,超声波焊接中,焊接整体处于采用外部声控震动频率的焊接,实现了焊接技术和焊接结构的优化应用,在焊接中对锂电池的损伤性达到最小,保障了锂电池的焊接后应用寿命,是一种具有高强度稳定性和安全性的焊接形式,推进我国焊接技术水平和焊接质量的发展。
此外,还可以从技术应用对锂电池的应用寿命角度进行分析,采用超声波焊接技术进行极耳焊接,可以将后期焊接对锂电池的损伤降至最低,从而避免锂电池受到损伤,使锂电池的应用寿命性得到保障。由此可见,超声波焊接技术在动力电池极耳焊接的工艺过程中具有较高的应用优势。
(三)焊接效果分析
锂电池中极耳的连接质量,关乎锂电池的应用的安全和效率,采用超声波焊接的应用来看,新型超声波焊接技术能够保障焊接极耳之间的接触面积和连接可靠性,如果采用传统的焊接方式进行焊接,容易发生焊接高温融化,焊点飞溅、或者热传导破坏锂电池内部结构的问题。采用超声波焊接技术通过焊头振动摩擦生热过程,加压过程冷却过程,在焊点处无飞溅,同时产热量少,减少对锂电池内部结构的影响,保证焊接整体效果。
(四)焊接材质分析
从异种金属焊接的困难看,超声波的焊接振幅传播可以突破多种材质的限制,超声波焊接技术实现了焊接材质的突破,突破了极耳焊接两侧材质不一致带来的焊接困难,实现了铜铝不同金属间的直接焊接。同时,超声波焊接技术可以根据焊接极耳的介质强度进行自动化调节,能够带来焊接介质应用的多样化发展,保障了锂电池中极耳连接的焊接质量。
从后期质量来看,极耳焊接中主要采用铜、铝等金属元素作为焊接的介质,但随着后期应用时间的逐步延长,传统焊接介质在氧化的作用下出现开裂等问题,如果依旧采用传统的方式进行焊接的补修,会使极耳的焊接效果受到影响,同时较强的后期焊接温度也会造成锂电池内部的损伤,对锂电池的安全性带来隐患。采用超声波焊接技术作为焊接方式,应为在焊接过程中对材料氧化层进行了破坏和清理,降低了极耳后期应用发生焊点腐蚀、开裂的情况,保障极耳焊接的质量。
(五)超声波焊接工艺的不足之处
超声波焊接技术在锂电池极耳焊接上应用有着诸多优势,但同时也有一些不足之处,主要是超声波焊接的实现需要焊头是一套压紧装置,因此在应用过程中需要充分考虑作业空间的问题,也就要求进行极耳连接的结构设计设计时需要充分考虑结构能否实现超声波焊接,往往会造成设计结构不够紧凑,牺牲产品的一些空间。
结论:超声波焊接技术锂电池极耳焊接上的应用,虽然会造成一些产品内部空间的损失,但是其突破了诸多传统极耳连接的不足之处,实现了异种金属的直接焊接,并且保证了使用过程的中载流面积,使锂电池应用的安全性和可靠性得到了较大的提高,延长了焊点的寿命,也延长的锂电池的使用寿命,一定会成为超声波焊接技术应用新趋向。
参考文献
[1]李林贺,刘志盛.锂电池极耳超声波焊接质量分析[J].焊接技术,2012,06:46-49.
[2]王宋.超声波金属焊接机理及实验装置研究[D].河南郑州:河南理工大学,2009.
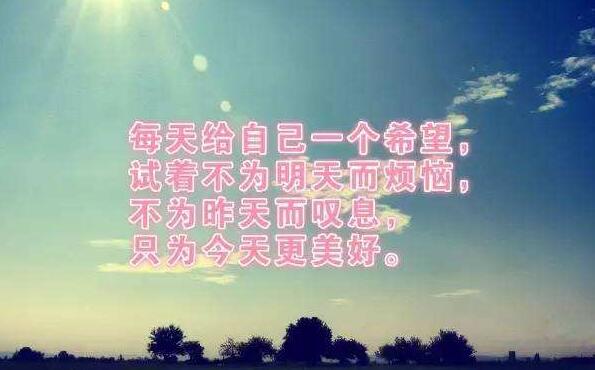
美丽校园的演讲稿范文(整理8篇)
- 阅0美丽校园的演讲稿篇1尊敬的各位老师,亲爱的同学们:大家上午好!今天我国旗下讲话的主题是”把美丽带进校园“。走在校园里,看见地上的一片纸屑,你是视而不见,还是弯腰捡起?在食堂.....
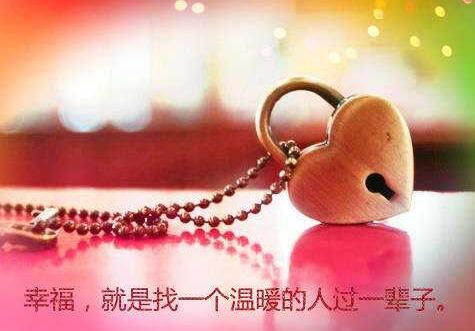
植树节的作文范文(整理16篇)
- 阅0植树节的作文范文篇1今天是植树节,阳光灿烂,老师安排我们一起去植树,我们开开心心地拿起水桶,抗起铁铲,带上树苗地去植树了。我们兴高采烈地来到路边,我和小明一组,我挖坑,小明提水.....
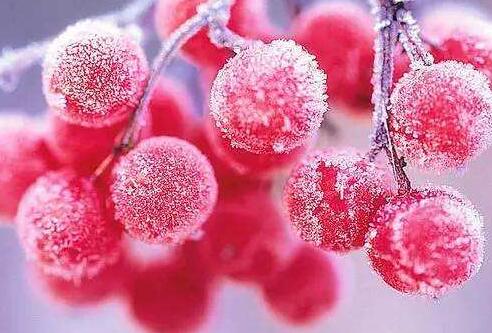
最新学校邀请语,学校邀请函怎么写
- 阅0学校邀请语学校邀请学校的邀请函篇1为继续深化课程改革,切实提高课堂教学的有效性,构建高效、优质课堂,促进青年教师专业成长,我校定于12月11日(第15周星期四)下午1:15承办樊川.....
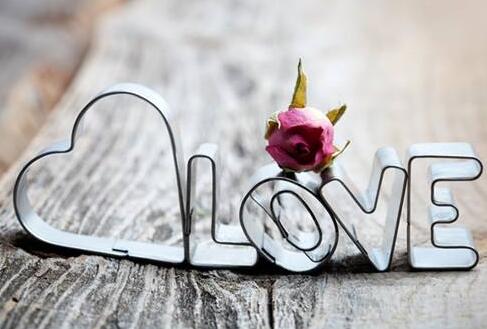
大学生实训报告范文(精选5篇)
- 阅0大学生实训报告范文在生活中,报告不再是罕见的东西,不同的报告内容同样也是不同的。那么一般报告是怎么写的呢?以下是小编收集整理的大学生实训报告范文,仅供参考,欢迎大家阅读。.....