机械设计概述(6篇)
来源:整理
机械设计概述篇1
关键词:机械设计;加工技术;机械产品
随着我国工业化技术与生产力水平的不断提高,机械化装备技术也得到了进一步发展。现阶段,我国机械化的制造质量、制造标准、制造工艺日趋完善,新技术、新标准的涌现,为我国机械化制造行业的发展提供了新的契机。机械设计加工是影响机械制造质量的主要因素,我们要深入研究机械设计加工的常见问题,以推动机械制造业的快速发展。本文从机械设计加工的概念出发,着重阐述了机械设计加工中的常见问题,并有针对性地分析了解决机械设计加工问题的有效对策。
一、机械设计加工概念
机械设计加工是通过机械零部件的设计、加工、组合来实现机械的功能性,其设计原理、运行方式、机械结构都需要满足于机械设备的具体要求,并利用整体方案逐步细化的特点来设计和制作机械零件的整个过程。机械设计加工从设计理念出发,可分为新型设计、变型设计、继承设计,其不同的设计特点为现代机械制造行业提供了极大的便利。
二、机械设计加工中的常见问题
1.零件质量问题机械设计加工中,零部件的质量会直接影响机械的寿命和性能。因此,在设计时要注意零部件的材质、特点、抗磨性、传感性等。同时,设计加工过程中也容易出现塑性变形、切割面粗糙、干裂、不耐腐等现象。2.加工精度控制不良。机械设计加工要有效控制好产品的加工精度。然而,现阶段机械设计加工时仍存在很多难以掌握的精度问题,如磨具选择、刀具的老化、温湿度变化等。这些因素都会影响机械加工的精度,进而也影响产品的质量。3.剂问题。有些机械设计加工时会使用到剂,主要是为了起到和冷凝的作用。当机床在高速运转时,设备和零件会因摩擦产生热量,这就需要使用来降低温度,以保证零件的质量。然而,现阶段很多生产单位都没有正确的使用剂,造成零件成品质量下降。
三、解决机械设计加工问题的有效对策
1.原材料的选择。原材料是机械设计加工质量的重要保障,设计和加工过程依靠对原材料的分析、处理、更换来实现零部件的制造。所以,在原材料的选择上要具有针对性,包括材料的大小、结构、质地、特性和价格等,不同的零部件所选择的原材料也不同,要正确分析和评价原材料。2.优化加工技术。机械设计加工由于材质的不同,加工时间的长短也存在不确定性,这在大规模的零部件生产中会影响产品的市场效益。因此,需要优化设计加工的设计时间、生产过程、加工技术,减少和压缩加工时间,以提高机械产品的生产效率。3.规范切削参数。机械零件生产过程中,切割技术是加工难点,切削的深度和速度会影响产品质量,所以要注重零部件的切削质量。在设计和加工时,要科学设置切削参数,不同材质的零部要选用不同的参数,这样才能够保证机械零部件的质量。4.加工工具的选择。机械设计加工时,加工工具也会影响机械产品的质量。因此,在机械零部件设计和制造过程中,要注重加工工具的选择,根据工具的特点和零部件材质的特点来选用适合的工具进行加工。另外,加工中要考虑不同刀具对不同材质零件硬度的影响,同时还要考虑不同零件的材质在大规模生产中对刀具损耗的影响。
作者:孟庆龙单位:哈尔滨电气股份有限公司
参考文献:
[1]张方东.机械设计与加工中存在的问题研究[J].内燃机与配件,2016(11).
机械设计概述篇2
关键词关键词:制造资源;模型;概念;本体;网络本体语言
DOIDOI:10.11907/rjdk.162017
中图分类号:TP301
文献标识码:A:1672-7800(2016)008-0004-02
0引言
当今信息化浪潮中,以计算机技术、自动化技术和互联网技术为代表的信息技术在制造行业应用广泛。制造技术与网络技术、智能技术不断融合,制造模式呈现智能化、网络化和协作化趋势。制造业全球化使得制造企业更迫切希望加强合作,共享制造资源。不同企业采用的制造资源描述方法不完全相同,使得制造资源数据呈现出分布性、异构性、多样性、复杂性等。在企业之间共享资源的需求下,传统的制造资源模型已经不能满足如此复杂多样的数据形式,需要建立一个统一的制造资源模型。本体具有很强的表达能力,能有效描述制造资源的概念以及概念间的关系,使用本体来描述统一制造资源可以帮助达到制造资源共享。本文主要研究制造资源本体建模方法。
1制造资源分类
制造资源可以分为狭义制造资源和广义制造资源,狭义制造资源主要指加工一个零件所需要的物质元素,是面向制造系统底层的制造资源;广义制造资源是指完成产品整个生命周期的所有生产活动的物理信息及技术要素物的总和,包括设计、制造、维护等相关活动过程中涉及的所有软硬件元素[1]。制造资源的分类是构建模型的基础,须按照统一的标准和形式进行描述,将有共同属性的资源划分为同一类别。传统制造业将制造资源简单分为人力资源和生成设备两类,在当今科技日新月异快速发展的时代,人们对制造资源的认识和理解要复杂和深刻得多。本文按照制造资源的属性和应用方式,将制造资源分为8类[2](见图1),具体如下:①设备资源:产品生产环节中各种制造、加工和运输设备;②人力资源:生产活动中各类人员,如管理人员、操作工人和设计人员等;③软件资源:企业管理和产品设计生产过程中各类软件,如办公软件、PRO/E等;④服务资源:产品生命周期里各种相关服务,如物流服务、培训服务等;⑤知识资源:产品生命周期中涉及到的各种研究机构、专利和市场信息等;⑥计算资源:生产活动中使用的计算机等相关硬件资源;⑦物料资源:产品生命周期使用到的原材料、能源等等;⑧除上述类别外的其它资源。
2制造资源建模方法
有研究使用状态图来描述制造资源,方法描述能力有限,没有被推广使用。面向对象的建模方法使用较多,该方法将客观世界中的事物抽象为对象,使用对象的属性来描述对象,属性的取值范围定义作为值域,用类的操作描述对象的功能[3]。基于本体的建模方法和面向对象的方法有一定相似之处,但本体更便于描述某领域中的概念和概念之间的关系,并且能够处理制造资源中具有逻辑关系的概念,所以本文采用基于本体的建模方法。
3本体建模
3.1本体的定义
本体(ontology)指事物本身,原来是哲学上的概念。目前被广泛认同的定义是“本体是共享概念模型的明确的形式化说明”[1]。包括以下几层含义:①共享:本体不是面向整体,其是共同认可的概念,是公认的知识的集合;②明确:本体中明确定义了使用的概念和概念的约束;③概念化:本体中的概念模型是客观世界抽象出来的,其与具体环境没有关系;④形式化:本体是计算机方便处理的。
本体可以定义为一个五元组O=(C,R,P,A,I),其中O代表本体,C(Concept或Class)表示概念或类别,R(Relations)表示关系,P(Property)表示属性,A(Axiom)表示公理,I(Instances)表示实例[2]。
3.2本体描述语言OWL
网络本体语言(WebOntologyLanguage,OWL)是由W3C提出的一种本体描述语言,OWL基于XML/RDF等标准,并且与其它多种本体兼容,具有很强的语义表达和推理能力。另外,OWL可以利用流行的本体描述工具protégé来描述制造资源本体,使用非常方便。OWL定义了3种表达能力不同的子语言:OWLFull、OWLDL和OWLLite,其中OWLFull的表达和推理能力最强,OWLDL适中,OWLLite最弱。OWLDL中的DL指的是描述逻辑(DescriptionLogic),其知识库是基于知识表示的一阶谓词逻辑的可判定子集。而DL与OWL之间有着对应关系,如DL中用于描述概念关系的公理集Tbox和描述个体实例的断言公理集Abox分别对应着OWL中的公理和事实,DL中的概念和角色分别对应OWL中的类和属性[3]。OWLDL已经能够完成制造资源本体需要的语义表达和推理服务,因此OWLDL已经成为制造资源表达的首选语言。不作特殊说明情况下,以下提到的OWL语言均是指OWLDL语言。
3.3本体建模步骤
本体建立主要包括以下几个步骤:①明确资源本体要覆盖领域的范围;②收集资源本体领域范围内的知识(定义、术语、属性及关系),并对制造资源概念划分类别与层次,形成资源本体框架,使用本体建模语言对本体形式化描述[1];③初步评价构建本体模型的一致性、完备性和清晰性;④检验和完善本体模型[4]。
4OWL实例描述
4.1机械零件分类
本文以机械零件资源为例构建一个基于OWL的资源本体,如图2所示。第一层次:按照机械零件的功能、用途分为模具行业零件、能源机械零件和机械标准件等;第二层次:按照机械标准件的属性和功能分为传动件、紧固件、轴承和法兰等;第三层次:将轴承功能及工作原理分为滚动轴承和滑动轴承;第四层次:将滚动轴承的结构特性分为推力球轴承、深沟球轴承和向心轴承等。如此划分层次清晰,结构完整,便于下一步概念本体模型的构建。
4.2制造资源概念本体模型构建
制造资源属性是描述其概念本体的重要信息,根据资源的属性特征抽象出描述制造资源的概念信息。图3是双列深沟滚动轴承的属性信息图,可将其属性进行分类,以更清晰描述概念。图4描述了双列深沟滚动轴承的属性和部分概念间的关系。
4.3基于OWL的表示实例
以“双列深沟球轴承”为例,基于OWL描述制造资源的方法。
(1)定义双列深沟球轴承类
上面代码用subClassOf表示继承关系[5],这里描述“双列滚动轴承”是“深沟球轴承”的子类,二者有继承关系,图形上看是一种层次结构。
(2)定义数据属性。
以上代码用DtatypeProperty表示了“生产厂商”是“双列深沟球轴承”的一个属性,其数据类型为string。
5结语
本文按照制造资源的属性和应用方式,将制造资源分为8类,简要分析了制造资源的几种建模方式,指出基于本体的建模方式的优势。介绍了网络本体语言OWL,并以机械零件中的双列深沟球轴承为例,使用OWL构建本体模型。建立的本体模型能有效描述制造资源,为优化企业内部资源结构以及企业间共享制造资源奠定了良好的基础。
参考文献参考文献:
[1]魏军英,钟佩思,郭春芬,等.基于OWL的制造资源本体建模[J].山东科技大学学报:自然科学版,2011,30(1):58-61.
[2]朱李楠.云制造环境下资源建模及其匹配方法研究[D].杭州:浙江工业大学,2014.
[3]党亚洲.基于本体的机械零件资源库语义检索研究与应用[D].乌鲁木齐:新疆大学,2015.
机械设计概述篇3
关键词:可靠性;机械制造工艺;指标体系;评价
中图分类号:TH16文献标识码:A文章编号:1009-8631(2012)(11-12)-0034-01
1引言
机械制造过程是一个复杂的动态过程,包括加工设备、夹具、刀具、检测设备、加工对象及工艺操作控制人员等。论文将机械制造过程作为研究对象,分析其对产品可靠性的保障能力,因此无论是研究对象还是分析内容都具有其特殊性,不同于普通产品,因而相关的可靠性概念不能简单地采用通常的系统可靠性定义,而需要根据对其规定的功能来加以定义。论文参考可靠性的通用定义,结合机械制造过程的特点,将机械制造的工艺可靠性定义为:机械制造过程在规定的条件下和规定的时间内,保证加工出来的产品具有规定的可靠性水平的能力。这里,机械制造过程就是产品的机械加工阶段,包括了产品的工艺设计与实现。
2机械制造的外部条件
机械制造的外部条件是指机械制造过程在规定的时间内所处的预先规定的全部外部条件,包括人员、设备、材料、工艺、测量、生产环境等条件。人员条件是对与制造过程相关的所有人员的要求,主要包括工艺设计人员、操作员、检验员等应具备的条件。设备条件是指对实现制造任务所需的所有设备的要求,主要包括对完成生产任务所需的生产、工具等所必需达到的要求。材料条件是指对构成产品(工件)实体的主要材料和在制造中起辅助作用而不构成产品实体的辅助材料所需要具备的条件。工艺条件是指完成制造任务所采用的技术方法及相关工艺文件的要求,包括对工艺技术、工艺方案、工艺流程、工艺规程、工艺细则、工艺标准、操作方法和工艺参数等具体的要求。测量条件是指对原材料检测、生产过程控制、产品质量检验、环保监测等过程所需具备条件的要求。生产环境条件是指生产(包括设计、加工、处理、装配、检测、计量、调整、试验等)的空间或厂房的大小、高低、通风、照明、温度、湿度、振动、噪声、洁净度、电磁辐射、静电、动力供应以及现场生产管理等环境条件要求。
3评价机械制造可靠性的基本概念
反应机械制造可靠性的基本概念主要有以下几个:第一,工艺故障发生率。在机械制造过程的工艺故障定义为在规定的条件下,机械制造过程丧失保障产品的可靠性指标这一规定功能的现象。一旦制造过程发生了工艺故障,无论是加工完成后产品的可靠性达不到规定要求的“软故障”还是制造设备自身出现的影响其完成加工任务的“硬故障”,势必影响加工任务的顺利完成,为生产商带来损失。因此,制造过程中应该尽量避免工艺故障的发生。在生产实践中,由于多种因素的影响,工艺故障总是不可避免的,但是对一个工艺可靠性水平令人满意的机械制造过程来讲,工艺故障的发生必然较少,所以这里提出了工艺故障发生率这个指标来评价一个制造过程发生工艺故障的频度。第二,工艺故障平均维修时间。对于复杂系统来讲,高可靠性本身不足以保证系统在需要时是可用的,还需要确保它能够快速地修复,特别是对机械制造过程来讲,只有及时地排除工艺故障,才能尽量减低制造过程工艺故障造成的损失。因此,需要通过工艺故障平均维修时间来衡量制造过程针对工艺故障的修复能力。第三,工艺稳定性。机械制造过程保障产品孔位特征的能力主要表现为产品孔位特征的加工过程是否稳定以及产品是否具有足够的加工精度。工艺稳定性是指在规定的时间内,由机械制造过程加工的产品的孔位特征值保持在一定的范围内,即具备要求的精度和偏差。论文通过机械制造过程的工序能力来衡量工艺稳定性。机械制造过程的工序能力是指工序处于稳定受控状态时,加工出来的产品质量满足技术规范要求的能力,通常通过产品孔位特征值的变异或波动来表示。工序能力取决于机械制造过程的技术能力和管理水平,决定于影响加工过程的因素(人、机、料、法、测、环等),并非决定于孔位特征的公差,但是为了通过机械制造过程的数据来评价其工序能力,需要通过与孔位特征相关的综合工序能力指数来进行评价。第四,工艺自修正性。由于多种因素影响,机械制造中不可避免地会产生加工误差。因此,对产品孔位特征的控制主要是确保加工误差在工艺文件允许的范围内。产品一般都需要按照规定的工艺路线经过多道工序加工完成,在每道工序的加工过程中都可能产生加工误差,而最终决定产品孔位特征的往往是位于工艺路线中靠后的工序,因为在前面工序中产生的加工误差有可能在后续的工序中予以修正。机械制造的工艺可靠性是一个比较抽象的概念,对一个具体的加工过程,需要全面客观地评价其工艺可靠性水平,这就要求在理解机械制造过程功能的基础上,确定评价制造过程保障产品可靠性能力的定量指标。由于产品可靠性的保障涉及多方面因素,因此不可能用单个的指标来评定机械制造的工艺可靠性,只有通过一系列的评定指标才能全面的刻画其完成规定功能的能力,这一系列的评定指标构成了机械制造的工艺可靠性的指标体系。
4工艺可靠性指标体系的选择标准
为了合理准确的评价机械制造的工艺可靠性,将其评定指标体系的选择标准归纳为以下几点:
4.1完备性:指标体系应能够全面地描述机械制造的工艺可靠性要求的各个方面;
4.2适用性:指标体系应能够与机械制造过程的运行机制相适应,即与制造过程功能失效的各种模式相对应;
4.3可计算性:能在实际机械制造过程中进行定量计算,这样才能定量评价制造过程保障产品可靠性的效果;
4.4可达性:指标应对机械制造过程完成其规定的功能起指导作用,只有制定出制造过程能够达到的功能要求,才能够对制造过程的能力提出合理的定量要求;
4.5可组合性:指标体系应能够适用于大多数制造过程,并根据具体的制造过程选取其中部分指标评价其工艺可靠性水平。
5工艺可靠性指标体系
机械制造的工艺可靠性指标体系的确定应依据工艺可靠性的定义,对定义中规定功能所涉及的各要素进行分解描述,然后再进行综合。在指标体系的确定中要考虑到机械制造过程的多加工设备和多工序的特点,同时注意到指标体系的完整性、适用性、可计算性等要求。由于产品的加工数据主要来自产品的孔位特征测量值,因此对机械制造过程的能力评价主要建立在对产品孔位特征测量值进行分析的基础上。根据前面的分析,在人员、材料、测量、生产环境等条件都能够充分保障的条件下,机械制造的工艺可靠性主要受加工设备和工艺的影响。我们用工艺可靠度、工艺故障发生率、工艺故障平均维修时间、工艺稳定性、工艺自修正性几个概念一起作为评价机械制造工艺可靠性的指标体系。
参考文献:
机械设计概述篇4
关键词:机械产品;方案设计方法;发展趋势
引言
科学技术的飞速发展,产品功能要求的日益增多,复杂性增加,寿命期缩短,更新换代速度加快。然而,产品的设计,尤其是机械产品方案的设计手段,则显得力不从心,跟不上时代发展的需要。目前,计算机辅助产品的设计绘图、设计计算、加工制造、生产规划已得到了比较广泛和深入的研究,并初见成效,而产品开发初期方案的计算机辅助设计却远远不能满足设计的需要。为此,作者在阅读了大量文献的基础上,概括总结了国内外设计学者进行方案设计时采用的方法,并讨论了各种方法之间的有机联系和机械产品方案设计计算机实现的发展趋势。
根据目前国内外设计学者进行机械产品方案设计所用方法的主要特征,可以将方案的现代设计方法概括为下述四大类型。
1、系统化设计方法
系统化设计方法的主要特点是:将设计看成由若干个设计要素组成的一个系统,每个设计要素具有独立性,各个要素间存在着有机的联系,并具有层次性,所有的设计要素结合后,即可实现设计系统所需完成的任务。
系统化设计思想于70年代由德国学者pahl和beitz教授提出,他们以系统理论为基础,制订了设计的一般模式,倡导设计工作应具备条理性。德国工程师协会在这一设计思想的基础上,制订出标准vdi2221“技术系统和产品的开发设计方法。
制定的机械产品方案设计进程模式,基本上沿用了德国标准vdi2221的设计方式。除此之外,我国许多设计学者在进行产品方案设计时还借鉴和引用了其他发达国家的系统化设计思想,其中具有代表性的是:
(1)将用户需求作为产品功能特征构思、结构设计和零件设计、工艺规划、作业控制等的基础,从产品开发的宏观过程出发,利用质量功能布置方法,系统地将用户需求信息合理而有效地转换为产品开发各阶段的技术目标和作业控制规程的方法。
(2)将产品看作有机体层次上的生命系统,并借助于生命系统理论,把产品的设计过程划分成功能需求层次、实现功能要求的概念层次和产品的具体设计层次。同时采用了生命系统图符抽象地表达产品的功能要求,形成产品功能系统结构。
(3)将机械设计中系统科学的应用归纳为两个基本问题:一是把要设计的产品作为一个系统处理,最佳地确定其组成部分(单元)及其相互关系;二是将产品设计过程看成一个系统,根据设计目标,正确、合理地确定设计中各个方面的工作和各个不同的设计阶段。
由于每个设计者研究问题的角度以及考虑问题的侧重点不同,进行方案设计时采用的具体研究方法亦存在差异。下面介绍一些具有代表性的系统化设计方法。
1.1设计元素法
用五个设计元素(功能、效应、效应载体、形状元素和表面参数)描述“产品解”,认为一个产品的五个设计元素值确定之后,产品的所有特征和特征值即已确定。我国亦有设计学者采用了类似方法描述产品的原理解。
1.2图形建模法
研制的“设计分析和引导系统”kaleit,用层次清楚的图形描述出产品的功能结构及其相关的抽象信息,实现了系统结构、功能关系的图形化建模,以及功能层之间的联接。
将设计划分成辅助方法和信息交换两个方面,利用nijssen信息分析方法可以采用图形符号、具有内容丰富的语义模型结构、可以描述集成条件、可以划分约束类型、可以实现关系间的任意结合等特点,将设计方法解与信息技术进行集成,实现了设计过程中不同抽象层间信息关系的图形化建模。
文献[11]将语义设计网作为设计工具,在其开发的活性语义设计网ask中,采用结点和线条组成的网络描述设计,结点表示元件化的单元(如设计任务、功能、构件或加工设备等),线条用以调整和定义结点间不同的语义关系,由此为设计过程中的所有活动和结果预先建立模型,使早期设计要求的定义到每一个结构的具体描述均可由关系间的定义表达,实现了计算机辅助设计过程由抽象到具体的飞跃。
1.3“构思”—“设计”法
将产品的方案设计分成“构思”和“设计”两个阶段。“构思”阶段的任务是寻求、选择和组合满足设计任务要求的原理解。“设计”阶段的工作则是具体实现构思阶段的原理解。
将方案的“构思”具体描述为:根据合适的功能结构,寻求满足设计任务要求的原理解。即功能结构中的分功能由“结构元素”实现,并将“结构元素”间的物理联接定义为“功能载体”,“功能载体”和“结构元素”间的相互作用又形成了功能示意图(机械运动简图)。方案的“设计”是根据功能示意图,先定性地描述所有的“功能载体”和“结构元素”,再定量地描述所有“结构元素”和联接件(“功能载体”)的形状及位置,得到结构示意图。roper,h.利用图论理论,借助于由他定义的“总设计单元(ge)”、“结构元素(ke)”、“功能结构元素(fke)”、“联接结构元素(vke)”、“结构零件(kt)”、“结构元素零件(ket)”等概念,以及描述结构元素尺寸、位置和传动参数间相互关系的若干种简图,把设计专家凭直觉设计的方法做了形式化的描述,形成了有效地应用现有知识的方法,并将其应用于“构思”和“设计”阶段。
从设计方法学的观点出发,将明确了设计任务后的设计工作分为三步:1)获取功能和功能结构(简称为“功能”);2)寻找效应(简称为“效应”);3)寻找结构(简称为“构形规则”)。并用下述四种策略描述机械产品构思阶段的工作流程:策略1:分别考虑“功能”、“效应”和“构形规则”。因此,可以在各个工作步骤中分别创建变型方案,由此产生广泛的原理解谱。策略2:“效应”与“构形规则”(包括设计者创建的规则)关联,单独考虑功能(通常与设计任务相关)。此时,辨别典型的构形规则及其所属效应需要有丰富的经验,产生的方案谱远远少于策略1的方案谱。策略3:“功能”、“效应”、“构形规则”三者密切相关。适用于功能、效应和构形规则间没有选择余地、具有特殊要求的领域,如超小型机械、特大型机械、价值高的功能零件,以及有特殊功能要求的零部件等等。策略4:针对设计要求进行结构化求解。该策略从已有的零件出发,通过零件间不同的排序和连接,获得预期功能。
1.4矩阵设计法
在方案设计过程中采用“要求—功能”逻辑树(“与或”树)描述要求、功能之间的相互关系,得到满足要求的功能设计解集,形成不同的设计方案。再根据“要求—功能”逻辑树建立“要求—功能”关联矩阵,以描述满足要求所需功能之间的复杂关系,表示出要求与功能间一一对应的关系。
kotaetal将矩阵作为机械系统方案设计的基础,把机械系统的设计空间分解为功能子空间,每个子空间只表示方案设计的一个模块,在抽象阶段的高层,每个设计模块用运动转换矩阵和一个可进行操作的约束矢量表示;在抽象阶段的低层,每个设计模块被表示为参数矩阵和一个运动方程。
1.5键合图法
将组成系统元件的功能分成产生能量、消耗能量、转变能量形式、传递能量等各种类型,并借用键合图表达元件的功能解,希望将基于功能的模型与键合图结合,实现功能结构的自动生成和功能结构与键合图之间的自动转换,寻求由键合图产生多个设计方案的方法。
2、结构模块化设计方法
从规划产品的角度提出:定义设计任务时以功能化的产品结构为基础,引用已有的产品解(如通用零件部件等)描述设计任务,即分解任务时就考虑每个分任务是否存在对应的产品解,这样,能够在产品规划阶段就消除设计任务中可能存在的矛盾,早期预测生产能力、费用,以及开发设计过程中计划的可调整性,由此提高设计效率和设计的可靠性,同时也降低新产品的成本。feldmann将描述设计任务的功能化产品结构分为四层,(1)产品(2)功能组成(3)主要功能组件(4)功能元件。并采用面向应用的结构化特征目录,对功能元件进行更为具体的定性和定量描述。同时研制出适合于产品开发早期和设计初期使用的工具软件strat。
认为专用机械中多数功能可以采用已有的产品解,而具有新型解的专用功能只是少数,因此,在专用机械设计中采用功能化的产品结构,对于评价专用机械的设计、制造风险十分有利。
提倡在产品功能分析的基础上,将产品分解成具有某种功能的一个或几个模块化的基本结构,通过选择和组合这些模块化基本结构组建成不同的产品。这些基本结构可以是零件、部件,甚至是一个系统。理想的模块化基本结构应该具有标准化的接口(联接和配合部),并且是系列化、通用化、集成化、层次化、灵便化、经济化,具有互换性、相容性和相关性。我国结合软件构件技术和cad技术,将变形设计与组合设计相结合,根据分级模块化原理,将加工中心机床由大到小分为产品级、部件级、组件级和元件级,并利用专家知识和cad技术将它们组合成不同品种、不同规格的功能模块,再由这些功能模块组合成不同的加工中心总体方案。
以设计为目录作为选择变异机械结构的工具,提出将设计的解元素进行完整的、结构化的编排,形成解集设计目录。并在解集设计目录中列出评论每一个解的附加信息,非常有利于设计工程师选择解元素。
根据机械零部件的联接特征,将其归纳成四种类型:1)元件间直接定位,并具有自调整性的部件;2)结构上具有共性的组合件;3)具有嵌套式结构及嵌套式元件的联接;4)具有模块化结构和模块化元件的联接。并采用准符号表示典型元件和元件间的连接规则,由此实现元件间联接的算法化和概念的可视化。
在进行机械系统的方案设计中,用“功能建立”模块对功能进行分解,并规定功能分解的最佳“粒化”程度是功能与机构型式的一一对应。“结构建立”模块则作为功能解的选择对象以便于实现映射算法。
3、基于产品特征知识的设计方法
基于产品特征知识设计方法的主要特点是:用计算机能够识别的语言描述产品的特征及其设计领域专家的知识和经验,建立相应的知识库及推理机,再利用已存储的领域知识和建立的推理机制实现计算机辅助产品的方案设计。
机械系统的方案设计主要是依据产品所具有的特征,以及设计领域专家的知识和经验进行推量和决策,完成机构的型、数综合。欲实现这一阶段的计算机辅助设计,必须研究知识的自动获取、表达、集成、协调、管理和使用。为此,国内外设计学者针对机械系统方案设计知识的自动化处理做了大量的研究工作,采用的方法可归纳为下述几种。
3.1编码法
根据“运动转换”功能(简称功能元)将机构进行分类,并利用代码描述功能元和机构类别,由此建立起“机构系统方案设计专家系统”知识库。在此基础上,将二元逻辑推理与模糊综合评判原理相结合,建立了该“专家系统”的推理机制,并用于四工位专用机床的方案设计中。
利用生物进化理论,通过自然选择和有性繁殖使生物体得以演化的原理,在机构方案设计中,运用网络图论方法将机构的结构表达为拓扑图,再通过编码技术,把机构的结构和性能转化为个体染色体的二进制数串,并根据设计要求编制适应值,运用生物进化理论控制繁殖机制,通过选择、交叉、突然变异等手段,淘汰适应值低的不适应个体,以极快的进化过程得到适应性最优的个体,即最符合设计要求的机构方案。
3.2知识的混合型表达法
针对复杂机械系统的方案设计,采用混合型的知识表达方式描述设计中的各类知识尤为适合,这一点已得到我国许多设计学者的共识。
在研制复杂产品方案设计智能决策支持系统dmdss中,将规则、框架、过程和神经网络等知识表示方法有机地结合在一起,以适应设计中不同类型知识的描述。将多种单一的知识表达方法(规则、框架和过程),按面向对象的编程原则,用框架的槽表示对象的属性,用规则表示对象的动态特征,用过程表示知识的处理,组成一种混合型的知识表达型式,并成功地研制出“面向对象的数控龙门铣床变速箱方案设计智能系统gbcdis”和“变速箱结构设计专家系统gbsdes”。
3.3利用基于知识的开发工具
在联轴器的cad系统中,利用基于知识的开发工具nexpert-object,借助于面向对象的方法,创建了面向对象的设计方法数据库,为设计者进行联轴器的方案设计和结构设计提供了广泛且可靠的设计方法谱。则利用nexpert描述直线导轨设计中需要基于知识进行设计的内容,由此寻求出基于知识的解,并开发出直线导轨设计专家系统。
3.4设计目录法
构造了“功能模块”、“功能元解”和“机构组”三级递进式设计目录,并将这三级递进式设计目录作为机械传动原理方案智能设计系统的知识库和开发设计的辅助工具。
3.5基于实例的方法
在研制设计型专家系统的知识库中,采用基本谓词描述设计要求、设计条件和选取的方案,用框架结构描述“工程实例”和各种“概念实体”,通过基于实例的推理技术产生候选解来配匹产品的设计要求。
4、智能化设计方法
智能化设计方法的主要特点是:根据设计方法学理论,借助于三维图形软件、智能化设计软件和虚拟现实技术,以及多媒体、超媒体工具进行产品的开发设计、表达产品的构思、描述产品的结构。
在利用数学系统理论的同时,考虑了系统工程理论、产品设计技术和系统开发方法学vdi2221,研制出适合于产品设计初期使用的多媒体开发系统软件muse。
在进行自动取款机设计时,把产品的整个开发过程概括为“产品规划”、“开发”和“生产规划”三个阶段,并且充分利用了现有的cad尖端技术——虚拟现实技术。1)产品规划—构思产品。其任务是确定产品的外部特性,如色彩、形状、表面质量、人机工程等等,并将最初的设想用cad立体模型表示出,建立能够体现整个产品外形的简单模型,该模型可以在虚拟环境中建立,借助于数据帽和三维鼠标,用户还可在一定程度上参与到这一环境中,并且能够迅速地生成不同的造型和色彩。立体模型是检测外部形状效果的依据,也是几何图形显示设计变量的依据,同时还是开发过程中各类分析的基础。2)开发—设计产品。该阶段主要根据“系统合成”原理,在立体模型上配置和集成解元素,解元素根据设计目标的不同有不同的含义:可以是基本元素,如螺栓、轴或轮毂联接等;也可以是复合元素,如机、电、电子部件、控制技术或软件组成的传动系统;还可以是要求、特性、形状等等。将实现功能的关键性解元素配置到立体模型上之后,即可对产品的配置(设计模型中解元素间的关系)进行分析,产品配置分析是综合“产品规划”和“开发”结果的重要手段。3)生产规划—加工和装配产品。在这一阶段中,主要论述了装配过程中cad技术的应用,提出用计算机图像显示解元素在相应位置的装配过程,即通过虚拟装配模型揭示造形和装配间的关系,由此发现难点和问题,并找出解决问题的方法,并认为将cad技术综合应用于产品开发的三个阶段,可以使设计过程的综合与分析在“产品规划”、“开发”和“生产规划”中连续地交替进行。因此,可以较早地发现各个阶段中存在的问题,使产品在开发进程中不断地细化和完善。
我国利用虚拟现实技术进行设计还处于刚刚起步阶段。利用面向对象的技术,重点研究了按时序合成的机构组合方案设计专家系统,并借助于具有高性能图形和交换处理能力的opengl技术,在三维环境中从各个角度对专家系统设计出的方案进行观察,如运动中机构间的衔接状况是否产生冲突等等。
将构造标准模块、产品整体构造及其制造工艺和使用说明的拟订(见图1)称之为快速成型技术。建议在产品开发过程中将快速成型技术、多媒体技术以及虚拟表达与神经网络(应用于各个阶段求解过程需要的场合)结合应用。指出随着计算机软、硬件的不断完善,应尽可能地将多媒体图形处理技术应用于产品开发中,例如三维图形(立体模型)代替装配、拆卸和设计联接件时所需的立体结构想象力等等。
利用智能型cad系统sigraph-design作为开发平台,将产品的开发过程分为概念设计、装配设计和零件设计,并以变量设计技术为基础,建立了胶印机凸轮连杆机构的概念模型。从文献介绍的研究工作看,其概念模型是在确定了机构型、数综合的基础上,借助于软件sigraph-design提供的变量设计功能,使原理图随着机构的结构参数变化而变化,并将概念模型的参数传递给下一级的装配模型、零件设计。
5、各类设计方法评述及发展趋势
综上所述,系统化设计方法将设计任务由抽象到具体(由设计的任务要求到实现该任务的方案或结构)进行层次划分,拟定出每一层欲实现的目标和方法,由浅入深、由抽象至具体地将各层有机地联系在一起,使整个设计过程系统化,使设计有规律可循,有方法可依,易于设计过程的计算机辅助实现。
结构模块化设计方法视具有某种功能的实现为一个结构模块,通过结构模块的组合,实现产品的方案设计。对于特定种类的机械产品,由于其组成部分的功能较为明确且相对稳定,结构模块的划分比较容易,因此,采用结构模块化方法进行方案设计较为合适。由于实体与功能之间并非是一一对应的关系,一个实体通常可以实现若干种功能,一个功能往往又可通过若干种实体予以实现。因此,若将结构模块化设计方法用于一般意义的产品方案设计,结构模块的划分和选用都比较困难,而且要求设计人员具有相当丰富的设计经验和广博的多学科领域知识。
机械产品的方案设计通常无法采用纯数学演算的方法进行,也难以用数学模型进行完整的描述,而需根据产品特征进行形式化的描述,借助于设计专家的知识和经验进行推理和决策。因此,欲实现计算机辅助产品的方案设计,必须解决计算机存储和运用产品设计知识和专家设计决策等有关方面的问题,由此形成基于产品特征知识的设计方法。
目前,智能化设计方法主要是利用三维图形软件和虚拟现实技术进行设计,直观性较好,开发初期用户可以在一定程度上直接参与到设计中,但系统性较差,且零部件的结构、形状、尺寸、位置的合理确定,要求软件具有较高的智能化程度,或者有丰富经验的设计者参与。
值得一提的是:上述各种方法并不是完全孤立的,各类方法之间都存在一定程度上的联系,如结构模块化设计方法中,划分结构模块时就蕴含有系统化思想,建立产品特征及设计方法知识库和推理机时,通常也需运用系统化和结构模块化方法,此外,基于产品特征知识的设计同时又是方案智能化设计的基础之一。在机械产品方案设计中,视能够实现特定功能的通用零件、部件或常用机构为结构模块,并将其应用到系统化设计有关层次的具体设计中,即将结构模块化方法融于系统化设计方法中,不仅可以保证设计的规范化,而且可以简化设计过程,提高设计效率和质量,降低设计成本。
机械设计概述篇5
引言
科学技术的飞速发展,使产品功能的要求日益增多、复杂性增加、寿命期缩短、更新换代速度加快。然而产品的设计,尤其是机械产品方案的设计手段则显得力不从心,跟不上时展的需求。在经济全球化的环境下,机械制造业的竞争实质上是产品设计的竞争。如何快速地进行机械产品的开发是提高制造业市场竞争能力的一个关键问题,进行机械产品现代设计理论、方法和应用技术的研究是十分重要的一项基础性工作。
目前计算机辅助产品的设计绘图、计算、加工制造、生产规划已得到广泛深入地研究,并初见成效,而产品开发初期方案的计算机辅助设计却远远不能满足设计需要。为此本文概括总结了国内外设计学者进行方案设计时采取的方法,并讨论了各种方法间的有机联系和机械产品方案设计计算机实现的发展趋势。
机械产品方案设计方法概括为以下四大类型:
1.系统化设计方法
系统化设计方法的主要特点是:将设计看成有若干设计要素组成的一个系统,每个设计要素具有独立性,各个要素间存在着有机联系,并具有层次性,所有要素结合后,即可实现设计系统所需完成的任务。下面介绍一些具有代表性的系统化设计方法。
1.1.设计元素法
用五个设计元素(功能、效应、效应载体、形状元素和表面参数)描述“产品解”,认为一个产品的五个设计元素值确定之后,产品的所有特征和特征值即已确定。
1.2.图形建模法
研制出设计分析和引导系统,用层次清楚的图形描述出产品的功能结构及其相关的抽象信息,实现了系统结构、功能关系的图形化建模,以及功能层之间的链接。
1.3.“构思”一“设计”法
将产品的方案设计分为“构思”和“设计”两个阶段。“构思”阶段的任务是寻求、选择和组合满足设计任务要求的原理解。“设计”阶段的工作则是具体实现构思阶段的原理解。
1.4.矩阵设计法
在方案设计过程中采用“要求一功能”逻辑树描述要求与功能之间的相互关系,得到满足要求的功能设计解集,形成不同的设计方案。再根据“要求一功能”逻辑树建立“要求一功能”关联矩阵,以描述满足要求所需功能之间的复杂关系,表示出要求与功能间一一对应的关系。
1.5.键合图法
将组成系统元件的功能分成产生能量、消耗能量、转变能量形式、传递能量等各种类型,并借用键合图表达元件的功能解,希望将基于功能的模型与键合图结合,实现功能结构的自动生成和功能结构与键合图之间的自动转换,寻求由键合图产生多个设计方案的方法。
2.结构模块化设计方法
从规划产品的角度提出:定义设计任务时以功能化的产品结构为基础,引用已有的产品解(如通用零部件等)描述设计任务,即分解任务时就考虑每个分任务是否存在对应的产品解。这样能够在产品规划阶段就消除设计任务中可能存在的矛盾,早期预测生产能力、费用,以及开发设计过程中计划的可调整。由此提高设计效率和设计的可靠性,同时降低新产品的成本。
3.基于产品特征知识的设计方法
基于产品特征知识设计方法的主要特点是:用计算机能够识别的语言描述产品的特征及其设计领域专家的知识和经验,建立相应的知识库及推理机,再利用已储存的领域知识和建立的推理机制,实现计算机辅助产品的方案设计。
机械系统的方案设计主要是依据产品所具有的特征,以及设计领域专家的知识和经验进行推量和决策,完成机构的型、数综合。想要实现这一阶段的计算机辅助设计,必须研究知识的自动获取、表达、集成、协调、管理和使用。
4.智能化设计方法
智能化设计方法的主要特点是:根据设计方法学理论,借助于三维图形软件、智能化设计软件和虚拟现实技术,以及多媒体、超媒体工具进行产品的开发设计、表达产品的构思、描述产品的结构。
在进行机电产品设计时,把产品的整个开发过程概括为“产品规划”、“开发”和“生产规划”三个阶段。
4.1.产品规划一构思产品。任务是确定产品的外部特征,如色彩、形状、表面质量、人机工程等,并将最初的设想用CAD立体模型表示出来,建立能够体现整个产品外形的简单模型。立体模型是检验外部形状效果的依据,也是几何图形显示设计变量的依据,同时还是开发过程中各类分析的基础。
4.2.开发一设计产品。该阶段主要依据“系统合成”原理,在立体模型上配置和集成解元素。将实现功能的关键性解元素配置到立体模型之后,即可对产品的配置进行分析。
4.3.产品规划一加工和装配产品。该阶段主要是装配过程中CAD技术的应用,提出用计算机图形显示解元素在相应位置的装配过程,即通过虚拟装配模型揭示造型和装配间的关系,由此发现难点和问题,并找出解决问题的方法
5.总结
值得一提的是,上述各种设计方法并不是完全孤立的,各种方法之间都存在一定程度上的联系。如结构模块化设计方法中,划分结构模块时就蕴含有系统化思想;建立产品特征及设计方法知识库和推理机时,通常也需运用系统化和结构模块化方法;此外,基于产品特征知识的设计同时又是方案智能化设计的基础之
网络技术的蓬勃发展,使得异地协同设计与制造,以及从用户对产品的功能需求一设计一加工一装配一成品这一并行工程的实现成为可能。但是,达到这些目标的重要前提条件之一,就是实现产品方案设计效果的三维可视化。为此,不仅三维图形软件、智能化设计软件愈来愈多地应用于产品的方案设计中,虚拟现实技术以及多媒体、超媒体工具也在产品的方案设计中初露锋芒。
机械产品的方案设计正朝着计算机辅助实现、智能化设计和满足异地协同设计制造的需求方向迈进。综合运用文中的四种类型设计方法是达到这一目标的有效途径。国外在这方面的研究已初见成效,我国的设计学者应该意识到与国际交流合作的重要性,并采取积极的措施。
参考文献:
[1]刘永翔产品设计实用基础[M]北京化学工业出版社,2003,134
[2]康晓东CAD技术(上)[J]机械工程师,1997,(6):54.
机械设计概述篇6
【关键词】Logistic模型财务预警回归模型
机械制造业作为工业的核心,随着我国经济及工业发展,其上市公司的数量日益增多。截止2014年12月,机械行业上市公司共计556家(含机械、设备、仪表),占整个沪深两市的21.05%。在机械行业取得快速发展的同时,同样存在因财务状况异常而被特别处理或退市风险警示处理的制造业上市公司,而这特别是在2014年。呈现出这一高比例的ST或*ST股的原因较多,由财务原因而被特别处理的主要原因是机械制造业财务风险管理意识淡薄,缺乏适合行业有效的财务预警体系。为此,对机械制造业及整个机械行业上市公司进行财务预警分析势在必得。通过构建有效的财务预警模型,防范、化解风险隐患,对机械制造业上市公司管理层、债权人、投资者、供货商以及其他利益相关主体而言都具有十分重要的现实意义[1]。
一、Logistic模型综述及相关表达
Logistic函数是在果蝇繁殖的研究工作中发现,并最早应用于人口估计与预测,通常把该函数又称为增长函数(Growthfunction)。由该函数构建的多元逻辑模型Logistic是依据被研究对象(或分析对象)的条件概率从而判断其财务状况和经营风险。模型的建立基础是累计概率函数,其优点是不需要严格的假设条件,突破了自变量服从两组间协方差相等和多元正态分布的局限性等。相对于多元判别分析,该模型更为稳健且具有更广泛的使用范围。为此,本文选择该方法对机械制造业公司进行分析[2]。
在财务预警分析中,通常将概率最佳分割因子设为0.5,当分析对象的值小于0.5时表明其财务状况健康,相反则表明存在财务危机。在上市公司的财务分析中,Logistic模型表述为[3]:
■1.1
式中,Yi表示第i家企业的财务状况,当i=0时为财务危机企业,当i=1时为财务正常企业;Xki为第i家企业的k个财务比率。
将计算得到的Yi值代入下式1.2进行再计算:
■1.2
其Pi值便是由该模型得到的对第家企业的财务危机情况预估值。当该值大于0.5时表明存在财务问题。
综合上述两市,并采用对数表达,得到Logistic模型的常用表达:
■1.3
从Logistic回归模型的原理可以看出,其模型不仅能对企业是否会发生财务风险做出很好的判断,同时还对其风险的大小可以进行量化。根据模型的理论背景,在实际应用中需有这样两个假设作为前提:(1)样本数必须为非回归参数;(2)自变量之间不存在共线性。
二、研究对象样本及相关数据选取
本文以证券会行业板块中的机械、设备、仪表类上市公司作为研究对象,其分析数据来自其中新浪网财经股票数据库,该数据库分析数据准确、及时,数据全面、可靠。
该数据库显示,截止2014年12月,机械、设备、仪表类上市公司共计556家,该类中的ST和*ST共计26家,占该类上市公司中的4.68%。
每个分析对象中,选取资产负债率(分析时用X1表示)、应收账款率(分析时用X2表示)、总资产周转率(分析时用X3表示)、主营业务利润率(分析时用X4表示)、每股经营现金流(分析时用X5表示)作为分析模型在计算过程中的参与分析量。资产负债率是资产负债表所有资产的总和同所有负债的总和相除得到的一个比值,对于其他指标的具体意义,在此不再详述。
三、机械制造业上市公司Logistic回归财务预警模型
(一)预警模型建立
采用统计软件――统计产品与服务解决方案软件SPSS16.0的Logistic回归功能,并选取回归方法为(Wald)法,对机械、设备、仪表类上市公司的资产负债比、应收账款周转率、总资产周转率、主营业务利润率、每股经营流数据进行3次回归计算,得到结果如下表1所示:
表1SPSS软件回归求得系数值
表中,B为变量系数;S.E为标准差;Wald为Wald得分;df为自由度;sig为伴随概率。
由此得到Logistic回归方程为:
■3.1
得到分析对象企业的财务危机情况预估值为:
■3.2
(二)回归模型统计检验
为验证所构建的回归模型,在初值-2LogLikelihood为91.702时,再利用SPSS软件对其进行分析,其输出值为表2所示(限于篇幅,该处只列出第三步回归输出值):
表2SPSS软件对模型计算的输出值
从计算结果可以看出,-2LogLikelihood值较大,表明本文构建的机械制造业上市公司财务预警模型拟合度较高。
(三)以川润股份为例,进行回归模型实例检验
根据所建立的Logistic回归模型,下面以川润股份(股票代码为002272)为例,进一步实例验证回归模型的统计检验。计算公式中单位为元。
资产负债比为:■=32.4%;应收账款率:■=136.97%;总资产周转率:■=28.5%;主营业务利润率:■=0.705%;每股经营现金流:X5=-0.0956。
将上述计算得到的值代入式3.2中,得到:
■=0.534。
四、结果分析
通过对川润股份(股票代码为002272)为实例进行计算,其结果为稍大于财务危机情况预估的临界值,其财务状况正常。该企业主要以生产制造销售液压设备为主,通过结合当前的机械制造业情况来看,当前制造业确实处在“艰难时刻”,这是由于受到全球经济复苏乏力、国内实体经济低位运行的影响,投资增速逐步放缓这一些因素所致。这一系列因素导致传统机械行业景气度低迷已成为不争的事实。
同时,从该股2014年9月30日公布的财务摘要中也可以看出:每股收益为0.0096元;每股现金含量为-0.0956元。
注:本文计算及结果依赖于企业公布数据的真实性,同时限于本文仅对财务预警模型的理论研究,因此其计算结果对投资人、债权人等所有利益相关方不具有实际参考意义。
五、结论
利用SPSS软件对机械设备仪表类上市公司财务数据进行统计学分析,得出Logistic回归模型参量。从而构建出当前机械设备仪表类上市公司财务预警模型,进一步将该模型中利用软件进行统计验证,其结果表明本文构建的机械制造业上市公司财务预警模型拟合度较高。
以某公司为实例,利用该模型进行分析,其分析结果为该公司超过财务危机情况预估的临界值,该公司财务状况正常,对利用Logistic回归模型的构建方法、实际应用提供了有意义的参考。
参考文献
[1]常立华.对企业财务危机临界点的认识[J].财会月刊,2008(4).
[2]刘彦文.上市公司财务危机预警模型研究[D].大连理工大学2009.
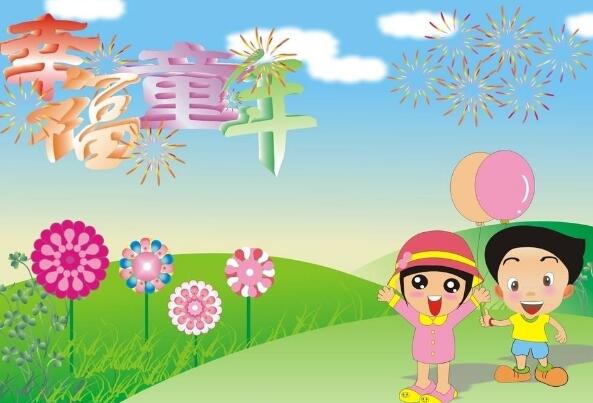
二年级期末总结范文(整理10篇)
- 阅0二年级期末总结范文篇1本学期我担任二年级的语文教学工作。经过半年的努力,学生取得一些提高,同时,我也收获颇多。在这一学期的工作中,有成绩,也有失误;有经验,也有教训。现就本学.....
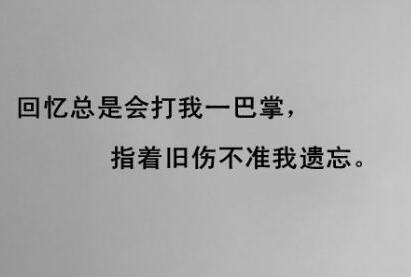
心中的彩虹作文范文(整理18篇)
- 阅0心中的彩虹作文篇1天色昏昏沉沉的,往日热闹非凡的街道此时空无一人,就连道路两旁的树都耷拉着脑袋。如此萧索又有点凄凉的景象,亦如我心中的光景。拿在手里的是张语文答题卡。.....
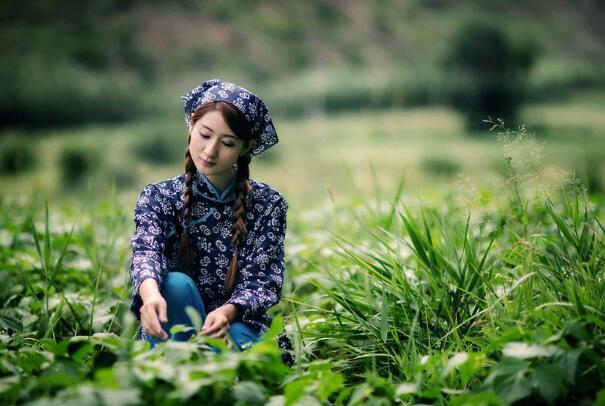
关于以感动为话题的作文范文(10篇)
- 阅0以感动为话题作文篇1法国著名的雕塑家说过:“这个世界并不缺少美,而是缺少一双发现美的眼睛”。同样,这个世界也不缺少感动,而是缺少一颗感受感动的心。那是在我五年级下学期的.....
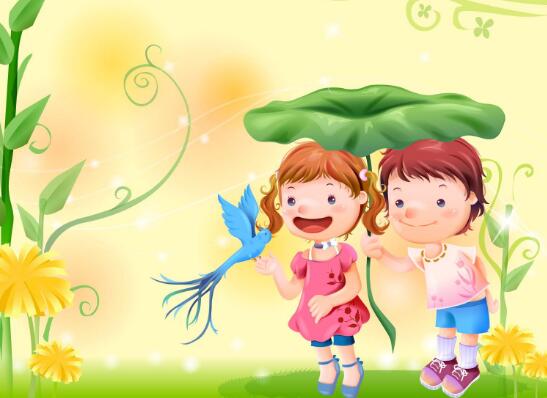
幼儿心理健康教育工作总结范文(整
- 阅0幼儿心理健康教育工作总结篇1有关于幼儿的心理健康教育,之前并不是了解得太多,也没有太深入的研究。不过我认为幼儿心理健康教育是教育必不可少的一个部分,在孩子成长过程中起.....