粉末冶金行业现状(6篇)
来源:收集
粉末冶金行业现状篇1
关键词TiAl基合金;粉末冶金;力学性能
中图分类号TF12文献标识码A文章编号1674-6708(2013)91-0045-02
0引言
作为高温结构材料,TiAl基合金正受到业内界人士的越来越高度关注,良好的抗氧化性能,低密度,耐高温性能等,让其比之镍基合金和钛基合金更具优越性[1],因此成为航空,国防,军工等高科技领域极具吸引力的材料。然而,室温塑性低,高温屈服应力高和加工成形性差等,使得TiAl合金广泛应用受到严重的制约。因此,研究和开发针对TiAl合金合理高效的制备与成形技术,是科技工作者的一个重要课题。常规制备TiAl基合金的方法主要有粉末冶金,铸造,铸锭冶金等。其中粉末冶金方法有其显著独特优点:克服了铸造缺陷,如疏松缩孔等;加入合金元素来制备复合材料变得容易;材料成分均匀,显微组织细小,力学性能优异;复杂零件易于实现近净成形。
1预合金粉末制备工艺
采用预合金粉末成型工艺制备TiAl基合金首先要制备γ-TiAl预合金粉末,之后经过模压成型与烧结反应而制得所需制件的工艺。此工艺的成本有些昂贵,因为,Ti熔点高且活性比较大,需要在制备过程中严格控制工艺,故难度也较大。现阶段,发展出来很多方法制备γ-TiAl预合金粉,其中主要被采用的有:雾化法、机械合金化法(MA)、自蔓延高温合成法(SHS)等。此工艺所获材料其晶粒大小,相分布以及合金元素分布的均匀性与相应的锻件相比,都得到显著提高。用预合金法,德国姆波公司制造出大型客机连接臂,和直升机叶片连杆接头,产品相比于锻件,材料和成本分别节省40%和34%[2]。随后美国坩埚公司又开发出,可以制备全致密,形状复杂的钛合金近形产品的陶瓷模热等静压技术,使得合金材料的力学性能得到进一步提升。
2元素粉末法
元素粉末法是对Ti、Al和Nb、Cr、Mo等外加元素预压成形,在高温下反应合成之后进行致密化来制备TiAl基合金材料的,制品组织细小、成分均匀。此法优点是成本比较低,工艺设备简单而且容易添加各种高熔点合金元素,通过均匀化混合和高温反应能避免成分偏析。元素粉末法制备TiAl基合金,已经得到了广泛研究,所制备出来的材料性能可与铸造TiAl基合金媲美。元素粉末法制备TiAl合金时Ti,Al元素会发生扩散反应,基本反应过程为[3]:6Ti+6Al4Ti+2TiAl3,4Ti+2TiAl3Ti3Al+TiAl+2TiAl2,Ti3Al+2TiAl2+TiAl6TiAl。
3成型工艺
预合金粉末属硬脆粉末,不便直接模压成形,所以采用挤压方式进行成形。有冷挤压和热挤压两种方式。此工艺让粉末晶粒得到了细化,组织均匀性和粉末间的高温扩散能力得到提高。对于元素粉末挤压可以消除压坯膨胀开裂,而对于预合金粉末,挤压也提高了粉末变形能力。随着科技的进步,出现了很多新技术如:温压技术,流动温压技术,模壁技术,爆炸压制技术,高速压制技术等。这使得粉末冶金成形技术正向高性能化,高致密化方向发展。
4烧结反应工艺
以下是对目前出现的几种TiAl合金粉末冶金烧结工艺简单介绍。
4.1热压和热等静压
热压和热等静压是目前两种很可行的制备钛铝基合金的工艺。在压制的过程粉末的受力比较均匀,所得制件的致密度很高,力学性能很优异。经文献和实践所知,在1100℃~1300℃,压力大于100MPa时,将雾化TiAl预合金粉末,直接进行热等静压效果为最好。刘咏等人用此热等静压的工艺方法所制得的钛铝基合金制件,致密度高,显微组织细小,结果很是成功[4]。
4.2自蔓延高温合成工艺
自蔓延高温合成(也被称为燃烧合成方法),是利用化学反应过程所生成的热量和产生的高温,而使自身反应持续下去,进而获得所需材料或制品的方法。该工艺简单,高效节能,成本低且制品质量高,自问世后在世界范围内得到了广泛的研发与应用。其中开发出来的SHS制备粉体,烧结,致密化技术,能够制备出常规方法难以制备出的TiAl化合物,且产物形状复杂,致密度高,目前SHS粉末技术已成功应用与工业生产且技术越发成熟。
4.3放电等离子烧结
放电等离子体烧结亦叫作等离子体活化烧结,最早源于20世纪30年代年美国人的脉冲电流烧结原理,但此快速烧结工艺真正发展成熟是90年代从日本开始的,此后才得到广泛的关注与研发。在装有粉末的模具上联通瞬间,断续,高能脉冲电流,粉末颗粒间就能产生等离子放电现象,产生的高活性离子化的电导气体,迅速消除粉末粒表面的杂质和气体,并加快粉末的净、活、均化等效应[5]。SPS艺有其独特优势:加热均匀,烧结温度低且升温速度快,产品组织细小均匀且致密度高。研究表明,用MA技术与SPS技术结合制备出的TiAl合金,组织均匀,性能优良。
4.4粉末注射成形工艺
此技术是把塑料注射成形工艺和传统粉末冶金技术相互结合,而发展成为一种新型的近净成形的工艺。主要步骤为:混合粉末与粘结剂,注射成形,脱模,烧结。此工艺制备的制件致密度高,组织均匀,性能优越,能够制备质量要求高且精密复杂的制品,而且成本低,自动化程度高,材料利用率几近百分百。因此该工艺在国际上很热门,很受欢迎。采用PIM工艺制备出的TiAl合金组织细小均匀,相对密度高,性能优良,而且成本与传统工艺比大大降低,当然此方面的研究还有广阔空间。
5粉末冶金TiAl基合金的力学性能
作为高温结构材料,TiAl合金因为低的密度,高强度系数,良好的抗氧化性能和抗蠕变性能等,而备受关注与欢迎。然而因低室温延展性,难加工性,使其被广泛应用受到制约[6]。如何使其强度和延展性相平衡是一个很大挑战,有关此方面的研究工作一直在进行。研究表明,TiAl合金中增加Nb能改善TiAl合金高温抗氧化性能,适量Cr可以提高延性,B可以细化晶粒,提高抗蠕变性能。经过不断地改进和完善,粉末冶金TiAl合金的一些力学性能已得到了显著的提高。近期研究发现,合金添加Mo,V和Ag能改善显微组织,在1350度烧结能提高其致密度能达到96%,而抗压缩强度可达到1782MPa。然而,孔隙的难以彻底消除,间隙元素难于控制等问题,还需要不断地克服。
6结论
TiAl合金因其独特的性能在军工,航空等高技术产业占有重要地位,采用粉末冶金工艺制备TiAl基合金,优势明显,能够制备得精密度很高的制件。在TiAl合金制备技术中,极富吸引力,进而脱颖而出。然而,粉末冶金法制备TiAl基合金技术并不是完美至极的,还有一些工作需要进一步研究和拓展:控制间隙元素和杂质的污染;合金元素的合理选择与添加,改善TiAl合金的性能;进一步完善致密化技术,让显微组织更加均匀细化,消除孔隙缺陷等;进一步研发让生产低成本,高效率,规模化,不但为军用而且为民所用,促进经济的发展。粉末冶金钛铝合金技术有其独特的优势和地位,若得到进一步改进和完善,对我国的经济发展,国力的提升,具有重大意义。
参考文献
[1]Q.Liu,P.Nash.TheeffectofRutheniumadditiononthemicrostructureandmechanicalpropertiesofTiAlalloys[J].Intermetallics2011(19):1282-1290.
[2]赵瑶,贺跃辉.粉末冶金Ti6Al4合金的研制进展[J].粉末冶金材料科学与工程,2008,13(2).
[3]WangGX,DahmsM.PMI,1992,24(4):219-225.
粉末冶金行业现状篇2
关键词:粉末冶金;水雾化;铁基;专利
中图分类号:TB
文献标识码:Adoi:10.19311/ki.1672-3198.2016.18.103
1.前言
1965年,美国率先采用高压水雾化技术生产低碳钢粉末,虽然当时所得粉末成形性差,难以实际应用,但却具有成本低、纯度高等特点,从而引起了广泛的关注。在随后的70年代初,德国通过对水雾化铁粉进行高温还原,在很大程度上提升了水雾化铁粉的压缩成形性,为制备高性能的铁基粉末冶金零件奠定了基础,此后水雾化制粉技术得到快速发展。
2.水雾化铁基粉末专利分析
专利申请人所在的国家一般是某项技术的原创技术国。一般而言,一个国家在某项技术中拥有的专利越多,就表明其在该技术上的原创技术越多,说明其在该技术领域的研发能力和技术实力越强。由图1可以看出,目前,水雾化铁基粉末的相关专利主要集中在日本、美国、德国和加拿大等国家。
结合表1可以看出,中国之所以排在第二,首先与国外申请人在中国申请大量专利有非常大的关系,其次也与中国的高校在相关方面进行的研究密不可分。这在一定程度上说明了,我国在水雾化铁基粉末的研究方面有一定的成绩,而在其实际的生产及应用等方面则比较落后,相关的核心技术依然掌握在国外企业的手里,这不利于我国快速发展的粉末冶金企业的长远发展。
由表2可以看出,在全球的专利申请量上,排名前三的申请人分别为日本川崎制钢公司、日本神户制钢公司和瑞典的Hoganas公司,而这三者也是世界上目前较大的几家水雾化铁基粉末的生产企业。3我国水雾化铁基粉末专利分析
表3为中国专利申请中的中国申请人排名。由表可以看出,我国水雾化铁基粉末的相关专利申请中,科研院所占的比重较大。其中,北京科技大学、中南大学和钢铁研究总院三家科研院所的水雾化铁基粉末相关专利申请总数为31件,占中国水雾化铁基粉末相关专利申请总数的9.3%。这三家科研院所的相关专利多为实验研究性质的专利,其实际工业应用的可能性比较小,对我国水雾化铁基粉末的制备和相关产品生产的实际贡献很小。
对比国内外主要申请人的相关专利,可以发现,国内申请人的主要研究方向为:粉末成分的微调、制粉设备(特别是喷嘴)的改进、制粉工艺的改善等。这些方面都是在国外相关技术上的部分改进,这些改进虽能提高粉末的性能,但提高却十分有限,其所制备出的粉末往往是接近国外相同技术制备出的粉末。与国内申请人不同的是,国外的申请人则往往以大幅度提高粉末的性能,尤其是提高粉末在成形方面的稳定性为主要的研究方向。而且其在申请专利时,会故意保留该专利的核心部分不予公开,在获得了专利保护的同时,又避免其核心技术外泄。
粉末冶金行业现状篇3
【关键词】粉末冶金;球磨粉末;Ti-45Al-5Nb合金
【中图分类号】TH【文献标识码】A
【文章编号】1007-4309(2013)07-0055-1.5
TiAl金属间化合物具有低密度、高强度、优异的高温抗蠕变和抗氧化性等优点,在航空航天以及汽车工业等领域具有广泛的应用前景。高Nb含量TiAl合金保持了TiAl合金上述一系列优点,同时高含量难熔元素Nb的加入提高了合金的熔点及有序温度,降低了扩散系数,改善了高温抗氧化性能,被视为最具有开发潜力的新一代高温结构材料之一。然而,该合金存在严重的室温脆性,断裂韧性和裂纹扩展抗力也很低,且该合金属于难塑性加工材料。这些缺点阻碍着该合金的广泛应用。目前,该合金制备的工艺主要是铸锭冶金,该工艺存在成分偏析和组织粗大等缺点,且成本高,工序复杂。近年来,粉末冶金制备技术引起广泛关注。与铸态合金相比,粉末冶金合金的组织更均匀细小,而且,由于粉末冶金工艺可以实现近净成形,从而避免对合金的后续塑性加工,成为国内外学者制备TiAl基合金广泛关注的工艺。本文采用元素粉末冶金法制备高Nb-TiAl合金,对组织性能进行了研究。
一、实验
将平均颗粒尺寸小于48μm的高纯Ti、Al粉以及平均颗粒尺寸小于45μm的高纯Nb粉,按Ti-45Al-5Nb(at.%)成分配比,在行星式球磨机中进行机械球磨,球磨参数为:球料质量比为20∶1,转速为400r/min,球磨罐和磨球材料均为不锈钢,球磨时充高纯氩气保护,球磨时间为8h。随后,利用真空热压烧结系统对球磨获得的Ti/Al/Nb复合粉末进行反应烧结,烧结工艺参数为:烧结温度分别为1250℃、1300℃、1350℃,压制力为40MPa,保温保压时间为2h,整个烧结过程中真空度不低于10-2Pa,最后得到Φ60×13mm的三种烧结块体材料。
应用XRD分析材料物相组成,利用光学显微镜(OM)和配有能谱(EDS)分析系统的场发射环境扫描电子显微镜HitachiS4700(SEM)观测粉末的颗粒形貌演变、烧结块体试样组织。为选择典型粉末形貌,球磨粉末试样首先在烧杯中用酒精分散振荡,用滴管滴到钢制载物台,风干使酒精挥发制得粉末扫描样品。
二、实验结果与分析
1.球磨粉末特性
图1为复合粉末随球磨时间增长形貌演变的扫描和背散射图像。从中可以看出,球磨时间累计至4h,Ti、Al颗粒均为明显片状形貌,部分片状颗粒已发生破碎和粘合。随时间进一步延长,片状颗粒不断破碎,8h时片状颗粒破碎基本完成,形成了大量的碎小颗粒。通过背散射图像对比可以发现,Ti和Al的粉末颗粒在变形过程中形成明显的片状结构,而Nb元素颗粒则更多以碎小颗粒存在,并粘附在其他两种粉末上。这是由于Ti和Al的塑性比Nb较好,特别是低温环境下Nb有很严重的脆性。在巨大外力的快速作用下应力集中严重,从而直接破碎成细小颗粒。
图1不同球磨时间下Ti-45Al-5Nb粉末形貌(BSE)
(a)4h;(b)6h;(c)(d)8h
Ti-45Al-5Nb复合粉末经8h球磨得到的XRD分析结果如图2所示。从图中可以发现,复合粉末中并未产生新相,说明机械球磨过程中Ti、Al、Nb三种元素粉末仅实现机械结合,并未发生合金化反应。在球磨过程中,由于采用间隙球磨方式,粉末和罐体的温度得到很好的控制,这也限制三种元素之间的扩散速度,而且粉末的能量不足以推动Ti、Al元素之间的扩散反应,另外,Nb元素在低温环境中的扩散系数非常低,基本不考虑其反应。利用XRD结果计算复合粉末中三种元素的平均晶粒尺寸为19.7nm,三种粉末的晶粒均得到明显的细化。
2.烧结坯物相分析
利用X射线衍射仪分析三种烧结坯所得结果如图3所示。从图谱可以看出,三种烧结温度下合金中单质元素相完全消失,表明Nb元素完全固溶于TiAl合金中。同时,三种合金新生成的物相均以γ-TiAl为主,α2-Ti3Al次之,同时都有少量的B2相形成。对比发现,随着烧结温度提升,α2相含量有所减少,γ相含量增加。另外,1300℃和1350℃烧结合金的衍射峰相对于1250℃烧结合金向左有小角度偏移。这可能是由于Nb元素在更高烧结温度下扩散更加充分,其分布更加均匀,使三种物相的晶格常数变化引起的。
图2Ti-45Al-5Nb合金烧结XRD图谱
三、结论
1.采用元素粉末+机械球磨工艺制备Ti-45Al-5Nb复合粉末,充分的细化和均匀了三种元素粉末,Ti、Al粉末发生塑性变形成细小片状,而Nb则破碎成细小颗粒。经过8h球磨可以得到较好的复合粉末。经过球磨的复合粉末未发生合金化反应。
2.采用真空热压烧结工艺制备高致密的Ti-45Al-5Nb合金材料,在1250℃和1300℃烧结得到细小的近γ组织,在1350℃烧结得到的是近片层组织,同时三种烧结坯组织中均有B2相颗粒生成。
【参考文献】
[1]APPELF,OEHRINGM,WAGNERR.Noveldesignconceptsforgamma-basedtitaniumaluminidealloys[J].Intermetallics,2000,8.
[2]DUANQin-qi,LUANQing-dong,LIUJing,etal.MicrostructureandmechanicalpropertiesofdirectionallysolidifiedHighNbcontainingTiAlalloys[J].Materials&Design,2010,31(7).
[3]王衍行,等.高Nb-TiAl合金粉的制备及其特性[J].航空材料学报,2007,27(5).
[4]LIUB.,LIUY,ZHANGW,etal.HotdeformationbehaviorofTiAlalloyspreparedbyblendedelementalpowders[J].Intermetallics,2011,19(2).
[5]胡连喜,王尔德.粉末冶金难变形材料热静液挤压技术进展[J].中国材料进展,2011,30(7).
粉末冶金行业现状篇4
摘要:本文首先介绍了机械合金化技术的概念和技术原理,并讲述了机械合金化技术在材料科学与工程中的应用。并结合材料科学与工程专业课程的教学内容,探讨了机械合金化技术在材料科学与工程专业的教学实践中的研究和应用,并为合理利用机械合金化技术在材料科学与工程专业教学实践中发挥更大的作用提出了建议和意见。
关键词:机械合金化技术材料科学与工程教学实践
对于材料科学与工程专业的本科生来说,到了大三和大四就要学习许多专业课程和专业选修课程。其中有些课程属于材料合成与制备方法方面的内容。在材料合成与制备方法的课程教学中就需要涉及到材料的某些制备工艺,例如某些金属合金的制备工艺方法。对于金属合金的制备方法,很多教科书都详细地讲述铸造技术、焊接技术、粉末冶金技术、金属熔炼技术等,但也会涉及到机械合金化技术。机械合金化技术是近年来发展起来的一种制备高性能合金的新技术。这种技术主要是利用机械球磨工艺把不同种金属粉末通过机械球磨方式通过一定时间的球磨,最终使这些金属元素粉末通过机械球磨工艺形成金属合金,所以最终能够得到需要的新型金属合金材料。由于机械合金化工艺可以在常温下进行,不像金属熔炼技术那样需要较高的温度才能熔化金属,因此机械合金化技术更为实用,成本较低,而且材料的制备工艺简单。所以机械合金化技术近些年来发展较快,机械合金化技术所能够制备的金属合金材料的范围和种类也在不断地扩大,所制备的材料的性能也逐渐得到提高。由于机械合金化技术制备金属合金粉末的制备工艺简单,成本较低,使用的金属元素种类较多,而且可以用于实验室进行教学实验,所以机械合金化技术也逐渐应用到了材料科学与工程专业的课程教学与实践教学中。采用机械合金化技术制备金属合金粉末可以作为本科生实验课程的教学实验,也可以作为本科生的课程设计和毕业设计的教学内容。所以机械合金化技术将在材料科学与工程专业的教学实验中具有非常广泛的用途。
一、机械合金化技术的原理和应用
在机械合金化过程中,粉末受到磨球强烈的碰撞和挤压。极平的、纯净的金属表面在常温下加压可焊接在一起,这就是冷焊,也称为压力焊。塑性较好的金属粉末,在磨球的碾压、冲击下发生形变并以十分纯净的表面彼此接近到原子作用力的距离,同样可以冷焊在一起,形成相互交叠的层片组织,而脆性粉末或塑性粉末加工硬化变脆后,在冲击下直接破碎,所以球磨过程因体系不同而不同。在延性的金属-金属混合粉末中,粉末的变化分为三个阶段:颗粒粗化-破碎-粉末粒度的稳态分布,相应的称为初期、中期和后期。在机械合金化过程的初期,主要是冷焊过程,塑性粉末含量越多,粗化越明显,颗粒直径可到数毫米,同时颗粒表面也相当平滑;在机械合金化中期,冷焊和破碎交替进行,层片状较大颗粒与细小颗粒共存,细小颗粒是从大颗粒上脱落下来的,这一阶段各层内积蓄了能使原子充分扩散所需的空位、位错等缺陷,不同组元的扩散距离也接近原子级水平,合金化过程开始。在机械合金化过程的后期,基本上只有粉末颗粒破碎的过程,颗粒粒度趋向于最小值,因此也比较均匀。延性的金属与脆性的非金属或化合物组成的体系,脆性组元首先发生破碎,延性组元则首先发生变形,细小的脆性粒子处于延性颗粒之间。随后延性组元逐渐加工硬化,发生断裂和脆性组元一样尺寸不断减小。
机械合金化(MA)方法(塑性-塑性混合粉末)原理是:将金属粉末在磨球的碾压和冲击下发生形变,并以十分纯净的表面彼此之间接近到原子作用力的距离,实现冷焊,最终形成相互交叠的层片状组织。这个过程一般要经历颗粒粗化、破碎、粉末粒度的稳态分布三个阶段,其中初期以冷焊过程为主,粉末明显粗化,中间过程冷焊与破碎交替进行,层片大颗粒与细小颗粒共存,各层内积蓄了能使原子充分扩散所需要的空位和位错等的缺陷,使不同组元的扩散距离接近于原子级水平,合金化过程开始;在后期只有破碎过程,颗粒趋向于最小。机械合金化工艺可获得纳米颗粒,能使固溶、沉淀、弥散三种强化结合于一体,从而制备出性能优异的高温合金。
二、机械合金化技术在材料科学专业的课程教学与实践教学中的应用
在材料科学与工程专业的一些专业课程,例如材料合成与制备方法、纳米材料、功能材料等课程都讲述了机械合金化技术。例如在材料合成与制备方法这门课程中,有讲述金属合金材料的制备方法,除了传统的铸造工艺、焊接工艺、粉末冶金工艺以及金属熔炼技术之外,重点讲述机械合金化技术,因为机械合金化技术可以制备很多种金属合金材料,而且制备工艺简单,可以在常温下进行。由于机械合金化技术可以在实验室中进行,所以可以很方便开设实验课程。在纳米材料这门课程中讲述了纳米粉末的制备工艺,其中主要讲述了机械合金化工艺。因为机械合金化工艺制备纳米粉末的种类最多,涉及到很多种金属材料以及金属基复合材料的制备与合成等。还可以利用机械合金化技术制备复合材料,例如用机械合金化工艺球磨不同种元素粉末,使不同种金属元素通过机械球磨工艺形成金属合金粉末,所以通过机械球磨工艺原位合成金属基复合材料。在功能材料这门课程中,讲述利用机械合金化工艺制备纳米粉末颗粒和功能材料,例如制备贮氢合金Mg-Ni合金等。或者利用机械合金化技术制备铁磁合金材料、非晶态材料、纳米功能材料等各种先进功能材料。
利用机械合金化技术可以制备具有纳米尺寸量级的金属合金粉末。采用机械合金化技术制备的金属合金有很多种,例如采用机械合金化技术可以制备Fe-Al金属间化合物粉末、Ni-Al金属间化合物粉末,Ti-Al金属间化合物粉末,以及Ni-Fe合金、Fe-Si合金、Cu-Al合金等多种金属合金材料。以上讲述的都是利用机械合金化工艺制备二元合金材料。也可以利用机械合金化技术制备三元合金、四元合金以及多种成分的金属合金材料。例如利用机械合金化工艺制备Fe-Ni-Cr合金、Fe-Al-Ni合金,以及利用机械合金化技术制备具有多种成分的非晶态合金等。还可以利用机械合金技术制备贮氢材料,例如采用机械合金化工艺制备Mg-Ni合金等。采用机械合金化工艺制备的金属合金材料有很多种,有些金属合金材料的机械合金化制备工艺可以作为材料专业的教学实验,可以为学生演示如何利用机械合金化工艺制备高性能金属合金材料。例如采用机械合金化工艺制备Fe-Al金属间化合物粉末材料。采用机械合金化工艺可将固溶、沉淀和弥散三种强化方式结合与一体,制备一系列具有优异性能的高温合金。对Fc-Al合金的机械球磨或Fe-Al元素混合粉末的机械合金化已开展了一定的研究。Fe,Al纯元素混合粉末在球磨过程中,粉末受到强烈的碰撞、挤压,冷焊和破碎的相互作用使粉末细化,并在一定阶段形成金属合金。经过机械合金化工艺后就得到了粉末粒度极细的Fe-Al金属间化合物粉末。同时还可以采用机械合金化技术制备Ni-Al合金粉末、Ti-Al合金粉末等。
通过机械合金化工艺可以制备多种新型的金属合金粉末,而且成本较低,实验过程简单,可以作为本科生的实验教学课程内容。例如可以开设纳米材料的制备工艺的实验课程,使本科学生通过机械合金化工艺制备多种具有纳米结构的金属合金粉末,并对所制备的金属合金粉末进行性能表征,使学生通过实验课程认识和了解纳米材料的整个制备工艺以及表征方法。还有使学生通过机械合金化工艺制备先进的金属功能材料,如贮氢材料、纳米材料、铁磁性材料等,通过制备工艺结合性能表征使得学生对新型功能材料有了一定的认识和了解。
通过实验教学使学生认识和了解到机械合金化技术在材料科学与工程中的研究发展与应用,使学生加深课程教学知识内容的认识和掌握,使学生在课程学习的过程中既增加课本知识又锻炼了实践能力。所以在材料专业的实验教学中应该增加一些材料制备技术的教学实验,例如使学生利用机械合金化工艺球磨得到新型金属合金粉末材料,并研究机械合金化工艺球磨过程对金属合金粉末的物相组成和显微结构的变化,使学生通过实验课程对材料的制备和检测方法有了较深的认识,从而为材料科学与工程专业课程的学习打下了坚实的基础。
三、机械合金化技术在材料科学中的发展趋势与应用
机械合金化技术由于制备工艺简单,成本较低,材料合成温度较低,所以被广泛地应用到材料的合成与制备中。利用机械合金化技术可以开发新型的金属合金材料以及复合材料等。采用机械合金化技术可以开发出很多种类型的金属合金粉末,也可以开发金属基复合材料等,而且现在有越来越多的研究者从事机械合金化工艺制备金属合金材料和金属基复合材料以及功能材料的研究和开发,所研究和开发的材料种类也逐渐增多,应用范围也越来越广泛。机械合金化技术在材料科学与工程教学与实践中也得到广泛的推广和应用,已经成为材料科学与工程专业实践教学课程必须进行的实验内容。所以本文作者认为应该在材料科学专业的教学实践中增加机械合金化技术的实验课程,使得学生通过课程学习和实践学习来加深材料科学与工程专业课程知识和内容的认识和掌握。
综上所述,本文首先介绍机械合金化技术的概念和技术原理,讲述机械合金化技术在材料科学与工程中的应用,并结合材料科学与工程专业课程教学研究和探讨了机械合金化技术在材料科学与工程专业的教学实践中的研究和应用。采用机械合金化技术可以制备多种材料,这为材料科学与工程专业实验课程的教学实践提供了丰富的教学内容,可以在材料科学与工程专业的实验课程中开设一些关于机械合金化工艺制备新型金属合金材料的实验课程。
参考文献
[1]李青虹,晋芳伟,机械专业实验课程教学改革的研究[J].机电技术,2011(1):149—151
[2]刘宏达,马忠丽.高校实验课程教学质量评价体系的构建[J].中国现代教育装备,2009(3):60-63
[3]罗乐,张春早,黄英等.加强实验课程教学质量管理的探索[J].合肥工业大学学报(社会科学版),2005,19(1):16-18
[4]谢秀红,贾天钰.大学实验课程教学改革新探[J].航海教育研究,2007(2):74-76
粉末冶金行业现状篇5
0引言
激光熔覆技术是20世纪70年代随着大功率激光器的发展而兴起的一种新的表面改性技术,是指激光表面熔敷技术是在激光束作用下将合金粉末或陶瓷粉末与基体表面迅速加热并熔化,光束移开后自激冷却形成稀释率极低,与基体材料呈冶金结合的表面涂层,从而显著改善基体表面耐磨、耐蚀、耐热、抗氧化及电气特性等的一种表面强化方法[1~3]。如对60#钢进行碳钨激光熔覆后,硬度最高达2200HV以上,耐磨损性能为基体60#钢的20倍左右。在Q235钢表面激光熔覆CoCrSiB合金后,将其耐磨性与火焰喷涂的耐蚀性进行了对比,发现前者的耐蚀性明显高于后者[4]。
激光熔覆技术是一种经济效益很高的新技术,它可以在廉价金属基材上制备出高性能的合金表面而不影响基体的性质,降低成本,节约贵重稀有金属材料,因此,世界上各工业先进国家对激光熔覆技术的研究及应用都非常重视[1-2、5-7]。
1激光熔覆技术的设备及工艺特点
目前应用于激光熔覆的激光器主要有输出功率为1~10kW的CO2激光器和500W左右的YAG激光器。对于连续CO2激光熔覆,国内外学者已做了大量研究[1]。近年来高功率YAG激光器的研制发展迅速,主要用于有色合金表面改性。据文献报道,采用CO2激光进行铝合金激光熔覆,铝合金基体在CO2激光辐照条件下容易变形,甚至塌陷[1]。YAG激光器输出波长为1.06μm,较CO2激光波长小1个数量级,因而更适合此类金属的激光熔覆。
同步注粉式激光表面熔覆处理示意图[8]
激光熔覆按送粉工艺的不同可分为两类:粉末预置法和同步送粉法。两种方法效果相似,同步送粉法具有易实现自动化控制,激光能量吸收率高,无内部气孔,尤其熔覆金属陶瓷,可以显著提高熔覆层的抗开裂性能,使硬质陶瓷相可以在熔覆层内均匀分布等优点。
激光熔覆具有以下特点[2、9]:
(1)冷却速度快(高达106K/s),属于快速凝固过程,容易得到细晶组织或产生平衡态所无法得到的新相,如非稳相、非晶态等。
(2)涂层稀释率低(一般小于5%),与基体呈牢固的冶金结合或界面扩散结合,通过对激光工艺参数的调整,可以获得低稀释率的良好涂层,并且涂层成分和稀释度可控;
(3)热输入和畸变较小,尤其是采用高功率密度快速熔覆时,变形可降低到零件的装配公差内。
(4)粉末选择几乎没有任何限制,特别是在低熔点金属表面熔敷高熔点合金;
(5)熔覆层的厚度范围大,单道送粉一次涂覆厚度在0.2~2.0mm,
(6)能进行选区熔敷,材料消耗少,具有卓越的性能价格比;
(7)光束瞄准可以使难以接近的区域熔敷;
(8)工艺过程易于实现自动化。
很适合油田常见易损件的磨损修复。
2激光熔覆技术的发展现状
激光熔覆技术是—种涉及光、机、电、计算机、材料、物理、化学等多门学科的跨学科高新技术。它由上个世纪60年代提出,并于1976年诞生了第一项论述高能激光熔覆的专利。进入80年代,激光熔覆技术得到了迅速的发展,近年来结合CAD技术兴起的快速原型加工技术,为激光熔覆技术又添了新的活力。
目前已成功开展了在不锈钢、模具钢、可锻铸铁、灰口铸铁、铜合金、钛合金、铝合金及特殊合金表面钴基、镍基、铁基等自熔合金粉末及陶瓷相的激光熔覆。激光熔覆铁基合金粉末适用于要求局部耐磨而且容易变形的零件。镍基合金粉末适用于要求局部耐磨、耐热腐蚀及抗热疲劳的构件。钴基合金粉末适用于要求耐磨、耐蚀及抗热疲劳的零件。陶瓷涂层在高温下有较高的强度,热稳定性好,化学稳定性高,适用于要求耐磨、耐蚀、耐高温和抗氧化性的零件。在滑动磨损、冲击磨损和磨粒磨损严重的条件下,纯的镍基、钴基和铁基合金粉末已经满足不了使用工况的要求,因此在合金表面激光熔覆金属陶瓷复合涂层已经成为国内外学者研究的热点,目前已经进行了钢、钛合金及铝合金表面激光熔覆多种陶瓷或金属陶瓷涂层的研究[1、10]。
3激光熔覆存在的问题
评价激光熔覆层质量的优劣,主要从两个方面来考虑。一是宏观上,考察熔覆道形状、表面不平度、裂纹、气孔及稀释率等;二是微观上,考察是否形成良好的组织,能否提供所要求的性能。此外,还应测定表面熔覆层化学元素的种类和分布,注意分析过渡层的情况是否为冶金结合,必要时要进行质量寿命检测。
目前研究工作的重点是熔覆设备的研制与开发、熔池动力学、合金成分的设计、裂纹的形成、扩展和控制方法、以及熔覆层与基体之间的结合力等。
目前激光熔敷技术进一步应用面临的主要问题是:
①激光熔覆技术在国内尚未完全实现产业化的主要原因是熔覆层质量的不稳定性。激光熔覆过程中,加热和冷却的速度极快,最高速度可达1012℃/s。由于熔覆层和基体材料的温度梯度和热膨胀系数的差异,可能在熔覆层中产生多种缺陷,主要包括气孔、裂纹、变形和表面不平度[1]。
②光熔敷过程的检测和实施自动化控制。
③激光熔覆层的开裂敏感性,仍然是困扰国内外研究者的一个难题,也是工程应用及产业化的障碍[1、11]。目前,虽然已经对裂纹的形成扩进行了研究[1],但控制方法方面还不成熟。
4激光熔覆技术的应用和发展前景展望
进入20世纪80年代以来,激光熔敷技术得到了迅速的发展,目前已成为国内外激光表面改性研究的热点。激光熔敷技术具有很大的技术经济效益,广泛应用于机械制造与维修、汽车制造、纺织机械、航海[12]与航天和石油化工等领域。
目前激光熔覆技术已经取得一定的成果,正处于逐步走向工业化应用的起步阶段。今后的发展前景主要有以下几个方面:
(1)激光熔覆的基础理论研究。
(2)熔覆材料的设计与开发。
(3)激光熔覆设备的改进与研制。
(4)理论模型的建立。
(5)激光熔覆的快速成型技术。
粉末冶金行业现状篇6
关键词:新型;铸造工艺;航空发动机;成本;应用;
中图分类号:O434文献标识码:A
1前言
航空发动机被认为是迄今为止最为精密和复杂的机械系统(图1,英国罗.罗公司的遄达900涡扇发动机),它也是一个国家的科技和工业水平标志之一,航空发动机的恶劣工况对在中低温条件下工作的低压涡轮叶片、整体叶盘和涡轮机匣等高温铸件的低周疲劳寿命提出了更高要求,目前它的关键热端部位如机匣、燃烧室、涡、叶片等都采用高温合金制作,占到航空发动机重量的40-60%。由于机匣、涡、叶片等零件主体结构大多为薄壁回转体,且内型、外型复杂,因此零件的设计难度大、周期长【1】。
在制作工艺上,普通精铸形成的等轴晶铸件已经很少用于航空发动机的零部件,源于于机匣等部件的形状结构复杂化、大型化和高精度要求、壁厚差大,这些要求均对铸造过程构成巨大挑战,传统铸造易于形成晶粒粗大、偏析严重、缩孔、疏松等缺陷。其次,涡等复杂铸件在普通熔铸生产工艺条件下,一般为粗大的树枝晶或柱状晶,由于晶粒粗大及组织、性能上的各项异性,很容易导致铸件在使用过程中疲劳裂纹的产生和发展[2]。因此,为保证发动机零部件的使用寿命,采用常规的“铸造+锻造+机加工”工艺制作的零部件才能满足使用寿命,但此工艺的原材料浪费多,不利于节约资源。
2航空发动机零部件铸造工艺的形成及意义
2.1工艺形成基础
随着国防科技的发展,由于航空发动机工作温度提高,对叶片等合金的热强性能提出了进一步要求,使发动机零部件高温合金化程度不断提高,这就给压力加工过程带来很大的困难。因此针对复杂、高合金化航空发动机零部件的铸造工艺应运而生。本工艺利用国内现有生产设备优势,采用“真空感应+真空自耗+粉末冶金(PM)+热等静压(HIP)+热处理”的铸造工艺,有效地克服了零件大型化关、复杂关、质量关、资源浪费关。该工艺生产的制品性能与“冶炼+精密铸造”和“冶炼+铸造+机加工”等常规工艺的制品相比具有一系列优点:(1)材料无偏析,均匀性、稳定性、力学性能、抗腐蚀性能均好;(2)材料的晶粒比常规加工的细,因此可以方便地使用超声波无损探伤或100%的红外线探伤检测,故产品的可靠性高;(3)可直接做成最终尺寸的产品,因此比常规工艺可少用料50%以上,有效地节约了稀缺战略资源;(4)目前“PM+HIP”工艺中使用的模具可以用焊接组成,形状任意变化,部件的设计自由度较大,可制作各种异形体及整体部件,提高了制品整体的可靠性和成品铸件的力学性能和表面质量;(5)L.S.Ng等人用热等静压处理工艺处理M200高温合金粉末,结果表明:热等静压提高烧结试样的密度达到一个很好的值,这个值为99.6%。热等静压提高屈服强度,其平均数达到1123MPa,比真空烧结试样提高7.8%[3]。因此,用“真空感应+真空自耗+PM+HIP+热处理”工艺生产的发动机零部件,可使其力学性能、晶粒度、表面及内部质量均达到要求。
2.2工艺形成的战略意义
因此该铸造工艺的发展,将同时解决发动机生产周期长、产品质量不满足使用寿命、战略资源短缺等问题;目前我国新型战机对动力系统的需求主要依赖从俄罗斯、乌克兰进口,这样必将受制于人。该铸造工艺生产的发动机零部件将有效填补我国完全依赖进口的空白。同时,受到国内制造工艺水平以及理论基础等的限制,在某些关键材料使用寿命问题上与国外有较大程度的差距。因此开展航空发动机用关键铸造工艺开发,对解决我国重要型号研制的物资需求,对于推动我国新型航空飞机的研制乃至对国防建设具有重要意义。
3新型铸造工艺路线具体方案
近十几年,国内外高温合金研究者经过大量的技术、工艺改进,使高温合金铸件的晶粒组织得到了明显改善,铸件整体趋于均匀、细化。然而,因为细晶工艺的凝固过程有很强的形成显微疏松的倾向,其内部一般都存在不同程度的疏松等缺陷,使其力学性能和使用可靠性降低。本工艺采用“真空感应+真空自耗+PM+HIP+热处理”能同时解决航空发动机零部件的力学性能、尺寸精度、异型尺寸、表面和内部质量问题。
3.1新型铸造工艺路线
3.2工艺技术关键点
航空发动机零部件大部分采用高温合金钢制作而成,因其使用环境的特殊性,本工艺的关键技术是突破点:
3.2.1航空发动机零部件质量的特殊要求
(1)公差等级:因发动机铸件为大型、复杂、异型零部件,同一截面尺不均匀、精度要求高;
(2)力学性能:航空发动机的零部件承受多种载荷如轴向力、扭矩、弯矩以及内压等,因此对于发动机零部件的力学性能要求极高;
(3)表面质量:航空发动机零部件具有精密的外形尺寸,因此铸件表面及内部质量不允许有裂纹、冷隔、欠铸、缩孔及高密度夹渣对应和穿透性的缺陷;表面粗糙度、尺寸公差等也有严格要求;
3.2.2工艺技术关键点
(1)母合金成分设计与试样力学性能的匹配,试样力学性能合格与否关系着成分设计的成熟性;
(2)粉末冶金制备技术的优化,根据零部件性能大小要求选择粉末制剂方法;
(3)热等静压制备技术的理论和实际生产的结合成熟性;
(4)铸件热处理:对于复杂形状铸件的热处理工艺将是一种新的探索;
(5)粉末冶金和热等静压成型模具材料的选择与尺寸公差的设计;
3.3具体实施方案
(1)、根据各钢中各元素的不同作用,缩小化学成分范围,设计出理论上能达到铸态组织下的性能要求;
(2)、制定初步冶炼技术条件,采用小真空炉(约25Kg)冶炼,浇铸成小试样,试样热处理后,分析力学性能;
(3)、试样性能如不符合标准要求,则重新调整化学成分和热处理工艺;
(4)、试样性能测试达到标准值,则将该工艺固化进行大生产;
(5)、氩气雾化法制造粉末(AA粉)【4】,采用粉粒度相对细小、夹杂物尺寸小的AA粉,可有效提高发动机零部件的低周疲劳寿命、可靠性和使用寿命;其次,对粉末进行双真空脱气和双韧化处理,可提高铸件的致密度和改善材料的强度和韧性;
(6)、用3D打印技术设计制造接近成品尺寸的钢模;
(7)、将制作好的高温合金粉末按照设计好机匣尺寸的模具包套,制造成与机匣尺寸接近的毛坯件;
(8)、将粉末铸件包套,装入HIP装备中,在1000-2000℃和≤200MPa压力下进行4小时热等静压工艺处理;
(9)、铸件热处理:因铸件结构复杂、尺寸不均匀等,毛坯热处理制度参照小试样的制度执行;
(10)、铸件毛坯表面局部处理后用红外线探伤,合格品交付;
4应用与发展趋势
近几年来,随着国际技术交流合作不断加强,航空领域材料生产工艺制备也逐渐进入更深层次的合作研制,粉末冶金和热等静压技术在应用开发和设备改进方面的技术也得到了大幅度提高,产品质量走向高端成熟阶段。在未来几年,PM和HIP技术将向更高层次发展:
4.1PM发展方向主要有:(1)纯净度冶炼和粉末粒度细小、非金属夹杂含量低;(2)先进的热处理技术和合金致密化程度;(3)开发新型高温、超高温难熔金属技术。
4.2HIP发展方向:(1)成熟的计算机软件开发在HIP技术方面的研究;(2)开发大尺寸HIP设备以适用于更多领域;(3)提高我国HIP设备的设计制造水平、自动化水平。
5仍需要解决的问题
在当前技术条件下,尽管“PM+HIP”技术能用于工业生产的各个领域,但随着产品质量的要求越来越高、稀缺金属锐减、航空发动机等产品产业化趋势增强等一系列问题,给现阶段的PM、HIP和装备带来严峻的考验,新型铸造工艺的开发和大型精密装备的研制将是科技工作者下一步需要解决的工作重点。
6结语
21世纪,科技进步已进入稳定增长轨道,但国内航空发动机的研究水平和国外相差约10年,性能与国外航空强国相比还存在一定的差距,还难以满足我国第四、第五代新型战机研制及产业化需要。而作为航空高端装备制造产业中的项目之一,突破航空发动机关键工艺技术、加快推进航空发动机产业化,自主研制新型发动机,对提升我国的国际影响力和军事威慑力具有重要战略意义。因此PM和HIP技术以其先进的技术特点、低成本优势和高质量的生产制品应用于航天航空等制作复杂备件的各个领域,将是国内外关注和研发的热点。
参考文献
【1】刘林,高温合金精密铸造技术研究进展.铸造杂志2012,11:1273-1274.
【2】刘林,高温合金精密铸造技术研究进展.铸造杂志2012,11:1274-1275.
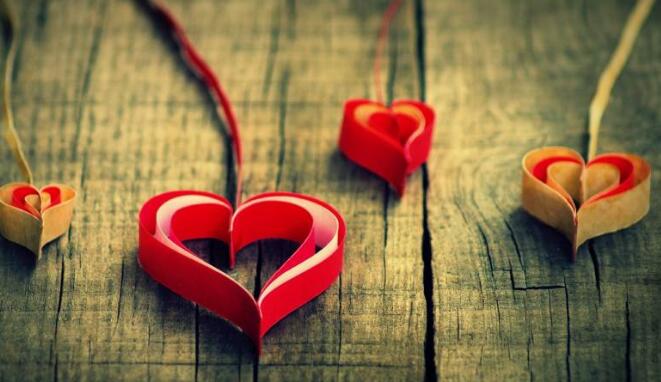
通知开会怎么写模板范文600字(精选
- 阅0通知开会怎么写模板范文【篇1因参会人员有会议冲突,原定于___月___日上午11:00召开的会议管理制度宣讲会推迟至___月___日11:30在会议室(2)召开,请大家准时参会。注:《会议管.....
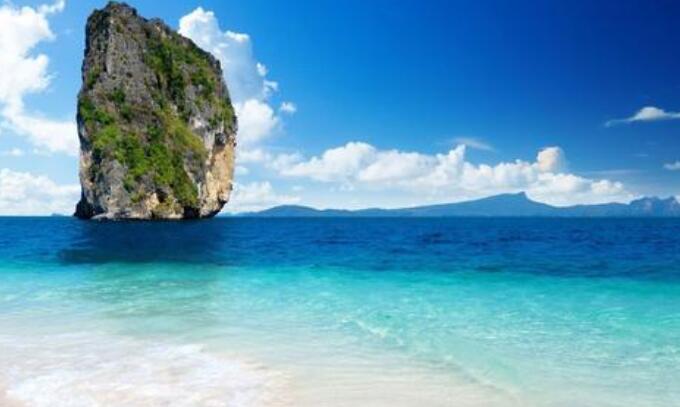
铁路通知范文(精选5篇)
- 阅0铁路通知范文【篇1辞职报告也称为辞职申请书,是个人离开原来的工作岗位时向单位领导或上级组织提请批准的一种申请书。本文给大家提供辞职报告范文,欢迎大家阅读。xx:您好!首.....
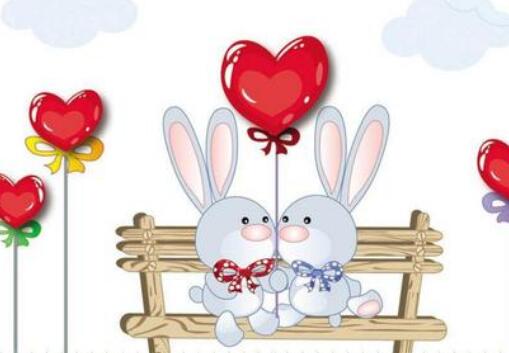
初中毕业到高中范文,初中毕业迎来高
- 阅0有关初中毕业到高中范文(推荐)篇1各位家长、老师、同学们:下午好!炎炎六月,百花争艳、云雀欢唱,滚滚而来的热浪激荡着我们的心潮。今天,我们欢聚一堂,心絮飞扬,无限欣喜的.....
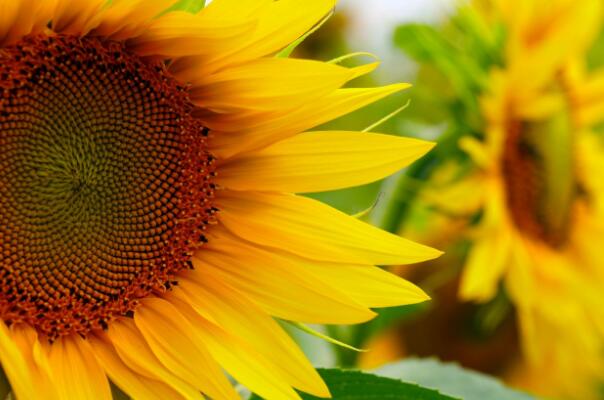
有关个人年度工作总结范文(整理4篇
- 阅0个人年度工作总结篇1转眼间,我们印刷部又跨过了一个年度之坎,虽然没有轰轰烈烈的战果,但也算经历了一段不平凡的考验和磨砺。作为一名基层管理者,工作共有苦有乐,偶尔有些惆怅,但.....